The types of coatings for industrial valves in extreme environments are essential for protecting critical valves and avoiding significant economic losses caused by accelerated deterioration, operational failures, and unexpected shutdowns. Asimer Group supports manufacturers of industrial pumps and valves in tackling these challenges through comprehensive CNC machining solutions, specialized welding, and advanced coatings, ensuring efficiency, durability, and cost-effectiveness. Thanks to our advanced CNC technology and in-house metrology lab, we deliver unmatched precision and proven results in the most demanding applications.
Understanding what a valve is and the challenges in extreme environments
A valve is a mechanical device designed to regulate, stop, or control fluid flow within industrial systems. In demanding sectors such as petrochemical, naval, cryogenics, desalination, water treatment, or pulp and paper, valves must withstand especially aggressive conditions.
Valve failures can disrupt critical operations, increase operational costs, and negatively impact productivity. Having a deep understanding of these specific industrial environment challenges allows for the selection of more effective coatings, minimizing operational risks.
Types of coatings for valves in extreme environments and their benefits
Comparative table of industrial coatings in extreme environments
Type of Coating | Applied by Asimer? | Associated Processes | Main Benefits | Typical Applications |
---|---|---|---|---|
Metallic anti-corrosion | Yes | TIG welding, PTA, machining | High chemical and thermal resistance | Oil & Gas, Petrochemical, Cryogenics |
Ceramic | No | Thermal spray (external) | Extreme hardness, wear resistance | Mining, heavy chemical industry |
Technical polymers | No | Surface coating | Chemical resistance, low friction | Chemical industry, diaphragm valves |
Tungsten carbide | No | PTA welding | Maximum resistance to abrasive wear | Pumps and valves in severe conditions |
In industrial environments where corrosion, temperature, or mechanical wear are extreme, specialized welding not only complements coatings but serves as a key technical solution to reinforce critical areas in industrial pumps and valves.
Asimer Group specializes in processes such as TIG welding, MIG welding, automatic MIG welding, and PTA (Plasma Transferred Arc), precisely applied to stainless steel components, special alloys, or parts exposed to harsh conditions. These processes enable:
- Application of alloy layers such as Inconel®, Stellite®, and Hastelloy® for protection against corrosion and wear.
- Extension of the lifespan of components subjected to impact, friction, or cavitation.
- Restoration of worn geometries with maximum precision thanks to our CNC machining capabilities after the welding process.
This know-how makes Asimer a strategic partner for manufacturers requiring customized components with high operational resistance.
In a recent project for the cryogenic sector, we applied PTA welding with Stellite® on valve seats exposed to extreme abrasion and cryogenic conditions. After post-welding CNC machining, the valves successfully passed non-destructive testing, achieving a 45% increase in estimated operational lifespan.
Metallic anti-corrosive coatings: protection for oil refining and oil & gas applications
Special alloys such as Inconel®, Hastelloy®, and Stellite® are primarily used in specialized welding processes such as TIG and PTA to coat critical areas exposed to high temperatures or highly corrosive environments. In certain cases, when parts are entirely made of these alloys, they are also machined using CNC technology. These alloys provide exceptional resistance in cryogenic valves and components used in the petrochemical and oil & gas industries, ensuring protection against severe corrosive agents.
Some of our featured projects:
- 16 diaphragm-type globe valve bodies DN80 1500#, made of forged A316L steel
A representative case of coating application on industrial valves for extreme environments was a project recently carried out for a French client specialized in high-performance control valves. In this project, we worked on 16 diaphragm-type globe valve bodies DN80 1500#, made of forged A316L steel with socket-welded ends, designed to operate under severe pressure and temperature conditions.
The project included Stellite Gr.6 deposition through specialized welding, in accordance with ASME standards and under a WPS approved by the end customer. This coating, applied to critical areas of the valve body, provided exceptional protection against erosion, cavitation, and corrosive agents—factors commonly encountered in sectors such as oil & gas, cryogenics, and petroleum refining.
After final precision machining and validation through non-destructive testing (PT and VT) conducted by Level II certified operators, a robust, durable, and technically reliable solution was achieved for highly demanding industrial applications. When applied correctly, Stellite® coatings not only extend the service life of components but also prevent unplanned operational failures and significantly reduce maintenance costs.
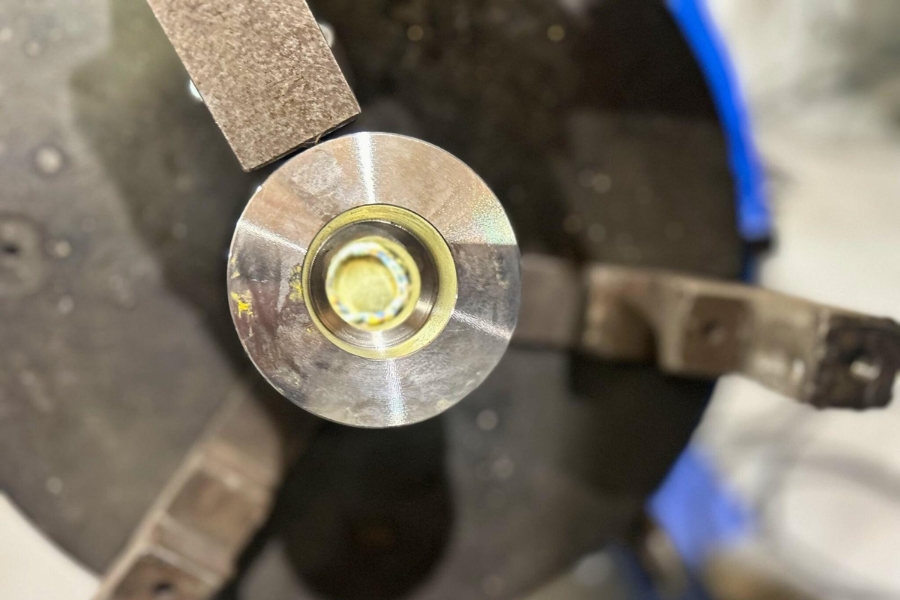
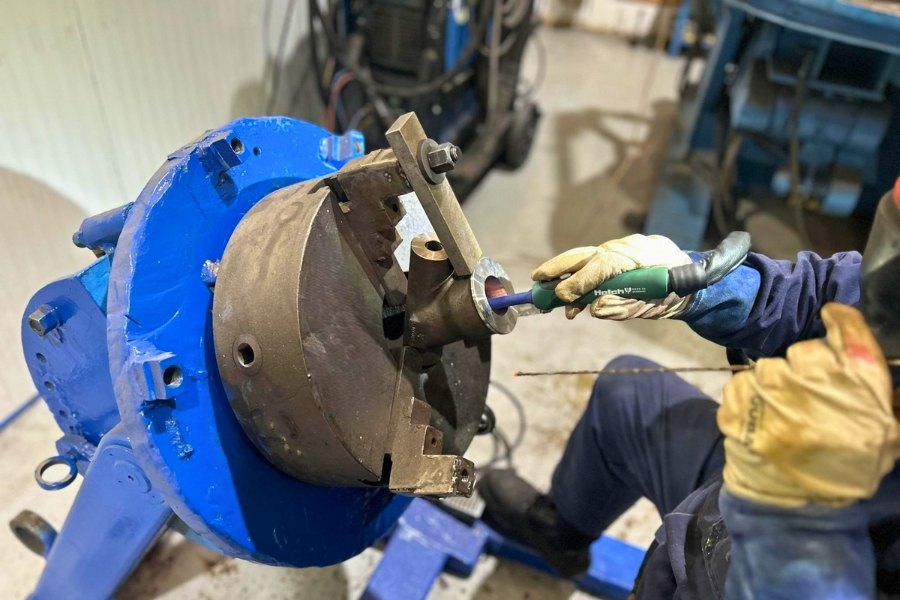
- Stellite application on high-pressure gate valves
Asimer Group applied Stellite coating on 18” 900# BW Pressure Seal gate valves made of A182 F22 steel, intended for high-pressure chemical service (+170 bar).
The process included pre-machining of critical geometries and Stellite welding in accordance with ASME standards, following approved WPS and PQR procedures. After deposition, the valves underwent rigorous non-destructive testing (PT, VT, and hardness testing), all performed by Level II certified operators.
Thanks to this coating, high resistance to wear, erosion, and chemical attack was achieved, significantly extending the service life of the valves under extreme operating conditions.
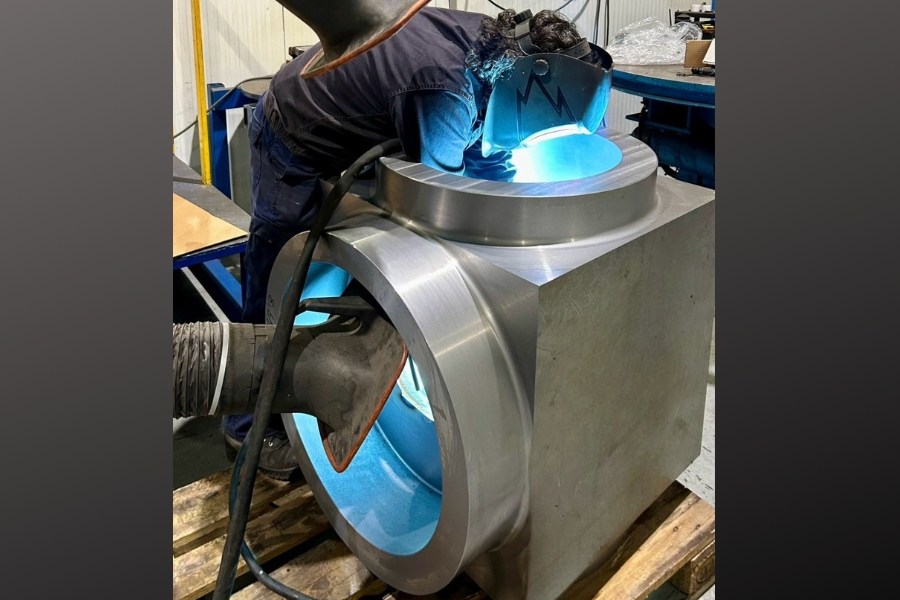
Ceramic coatings for high wear resistance
Although Asimer Group does not directly apply this type of coating, it is worth mentioning that ceramic coatings are widely used in the industry for applications requiring extreme hardness and resistance to abrasive wear. These are common in flow control valves and axial flow check valves in sectors such as mining or heavy chemical industry.
Technical polymers: solutions for industrial valves in the chemical industry
While this type of coating is not part of Asimer Group’s processes, its inclusion in this technical review provides a comprehensive overview of the available market solutions. Technical polymers are known for their chemical resistance and low friction coefficient, mainly used in diaphragm valves for aggressive or corrosive fluids.
Tungsten carbide: The ultimate solution against abrasive wear
Although Asimer Group does not currently apply tungsten carbide coatings, their relevance in improving resistance to wear and abrasion is noteworthy. These coatings are commonly used in valves and pump components operating in highly abrasive environments, significantly extending component life and reducing maintenance needs.
Specific industrial applications based on coating types for valves in extreme environments
Different industrial sectors require customized coating solutions depending on their operational conditions. For example:
- In the cryogenic industry, metallic coatings such as Inconel® applied through PTA welding ensure resistance to extremely low temperatures.
- In desalination and water treatment plants, protection against saltwater corrosion is achieved through special alloys that extend the service life of valves and pumps.
- In the petrochemical and oil & gas sector, coatings resistant to abrasion and aggressive chemical agents are used to prevent leaks and premature failures.
- In the marine industry, critical areas exposed to cavitation or seawater contact are reinforced through specific welding applications.
Asimer Group adapts the type of coating and welding process based on the environment and final application, ensuring performance and reliability under extreme conditions.
The importance of CNC technology in coatings for industrial valves in extreme environments
The success of a coating starts with proper surface preparation. Asimer Group applies high-precision CNC technology, including the use of the Trevisán machining center, to guarantee optimal tolerances before and after the coating or welding process.
This full control over the process allows for:
- Improved adhesion conditions.
- Homogeneous and repeatable finishes.
- Operations on large components without compromising critical geometry.
Our comprehensive approach combines CNC machining, metallic deposition through welding, and dimensional control in a single efficient workflow.
Quality control and precision for valve coatings in extreme environments
At Asimer Group, every coating undergoes rigorous testing to ensure durability and effectiveness. Our metrology lab is equipped with a measuring arm, high-resolution calipers, and other measuring instruments to verify critical tolerances after each stage.
Additionally, we perform non-destructive testing, including dye penetrant testing, to detect potential surface defects. This complete traceability ensures reliable results even in critical applications, such as cryogenic valves or pumps used in petrochemical plants.
Technological innovations in coatings for industrial valves in extreme environments
Asimer Group integrates Industry 4.0 principles into its machining and welding processes, allowing full traceability of every operation. The use of smart sensors, digitalized technical drawings, and automated CNC programming helps reduce intervention time and increase final quality.
Moreover, our continuous investment in innovation enables us to apply coatings precisely on critical areas, combining specialized welding with advanced metrological inspection.
In addition to material innovations, another critical aspect is the direct impact of these coatings on the performance of industrial pumps.
How valve coatings in extreme environments improve the performance of industrial pumps
Coatings applied to valves also positively impact the performance of industrial pumps. Particularly in centrifugal pumps, where erosion and cavitation can damage impellers, casings, or shafts, metallic coatings applied via TIG or PTA welding provide a protective layer that extends the lifespan of key components.
Asimer Group actively participates in centrifugal pump manufacturing projects, helping to reduce premature failures and improve hydraulic performance, even in environments with solid particles or corrosive fluids.
Advanced technical coating solutions for critical industrial sectors
Each sector requires a tailored technical response. In cryogenic applications, for example, Asimer applies low-temperature-resistant alloy coatings through PTA welding. In the oil & gas sector, CNC machining combined with welding ensures the tightness and chemical resistance of valves exposed to extreme pressures.
Similarly, in desalination and water treatment environments, components are protected against saltwater corrosion with materials specifically selected for each case.
These solutions not only enhance operational performance but also optimize machining costs for pumps and valves, extending their lifespan and reducing unplanned downtime.
Specialized welding and metal deposition: Key to protecting industrial valves
Beyond serving as a complement, metal deposition through welding is an advanced engineering solution with a direct impact on component durability and reliability. Asimer Group stands out in this field for its technical expertise in processes such as PTA, TIG, and automatic MIG welding, applied to a wide variety of materials and complex geometries.
Thanks to these metal additions, we can:
- Increase resistance to wear, abrasion, and localized corrosion in critical areas.
- Adapt the properties of the base material without needing to replace the entire part.
- Recover high-value components with precision, reducing downtime and costs.
In a recent project for the oil & gas sector, we reinforced check valve bodies exposed to continuous erosion from suspended particles using PTA welding. This intervention will extend operational life by over 50% without the need to manufacture new parts from scratch.
Specialized welding such as TIG, MIG, automatic MIG welding, and PTA effectively complement valve protection processes. The differences between TIG and MIG welding, as well as their applications in corrosive environments, highlight the importance of having a specialized partner like Asimer Group.
How to choose more sustainable industrial coatings
At Asimer Group, we also help our clients reduce the environmental impact of their industrial processes. Here’s a quick guide to check whether your coating solutions align with sustainable best practices:
♻️ Are coatings used that extend the service life of valves and pumps? Fewer replacements mean less waste and lower environmental impact.
⚙️ Are high-precision machining processes used to avoid rework? Precision reduces material waste and energy consumption.
🌡️ Do the selected coatings help reduce leaks or energy losses? Seal integrity directly contributes to energy efficiency.
🔩 Are components rehabilitated or recovered through welding instead of fully replacing them? Metal deposition allows reuse and avoids full remanufacturing.
🌍 Are solutions adapted to extreme conditions to prevent unplanned failures? Operational continuity reduces unnecessary consumption of energy and raw materials.
🛠️ Are corrosion-resistant alloys used to minimize frequent maintenance? Fewer interventions mean a smaller carbon footprint.
📏 Is quality control performed using non-destructive testing to avoid reprocessing? Testing before failure reduces energy use and machine time.
🔧 Is efficient CNC machining with optimized tools implemented? It lowers electricity consumption per production cycle.
📉 Are projects aligned with strategies to reduce the carbon footprint of pumps and valves? Key for clients seeking certified sustainability.
Comprehensive protection for industrial valves in extreme environments
Want to know how we can help improve the durability of your valves and pumps? Let’s talk.
This content was developed to help you identify the types of coatings for valves in extreme environments that best suit your industry. At Asimer Group, we specialize in the advanced application of coatings for industrial valves and pumps, ensuring lasting protection and optimal performance in the most aggressive environments. Contact our specialized technical team today to discover how our customized solutions can enhance the reliability of your operations, reduce your operating costs, and increase your competitive edge in the market.