TIG welding:
Accuracy and quality
for industrial pumps and valves
Tig welding:
Accuracy and quality
for industrial pumps and valves
What is TIG welding?
TIG welding (Tungsten Inert Gas) is an advanced technology that provides clean and precise welds, making it ideal for industrial applications where quality and structural integrity are essential.
At Asimer Group, a respected company in the field of engineering and machining, we utilize TIG welding to ensure maximum precision in the manufacturing of components for pumps, compressors, and industrial valves.
TIG welding uses a non-consumable tungsten electrode and an inert gas, typically argon, to shield the welding area from contamination. This process allows for precise, high-quality welds, especially for sensitive and delicate materials.
This advanced technique has become an indispensable part of our manufacturing process, ensuring the structural integrity and durability of our projects from the outset. Whether we are designing blueprints or finalizing production, TIG welding is our choice to meet and exceed the industry’s stringent standards.
Our firm commitment to excellence has driven us to efficiently incorporate TIG welding into all our operations. With this advanced technique, we achieve unmatched precision and control in every weld joint. This not only allows us to meet but exceed customer expectations in terms of strength, reliability, and performance.
TIG welding provides us with the flexibility to join a variety of materials with exceptional consistency and quality. From stainless steel to aluminum and specialized alloys, our expertise in TIG welding enables us to work with diverse materials, adapting our approach to meet the unique needs of each project.
Furthermore, TIG welding allows us to meticulously control the temperature and filler material feed rate, resulting in flawless welds that are both clean and highly resistant to corrosion. This meticulous attention ensures the quality and durability of every piece we produce.
TIG welding is not just a technique at Asimer Group; it is a cornerstone that drives our ability to deliver top-quality products to our clients.
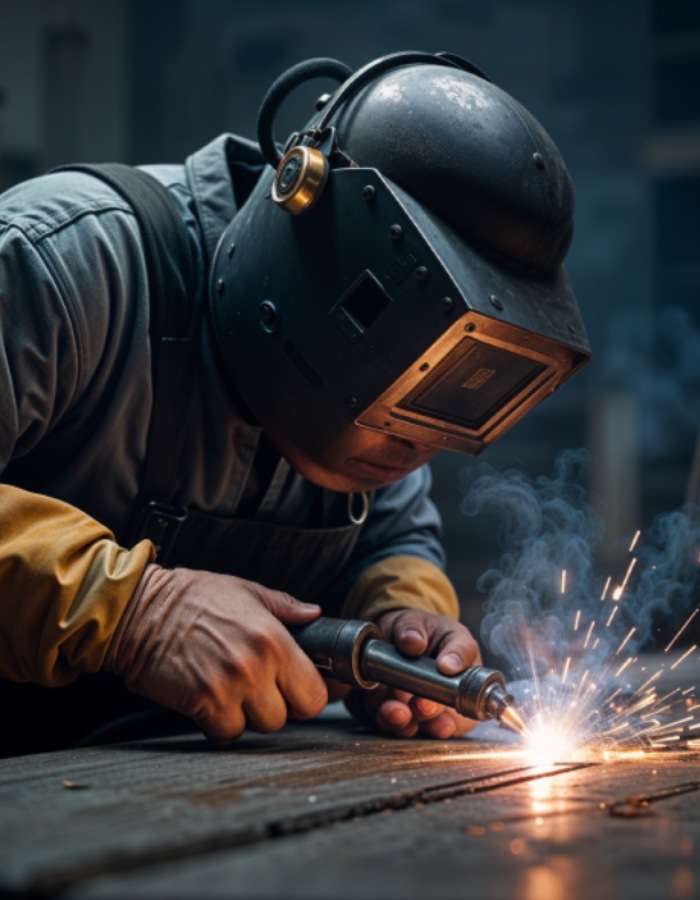
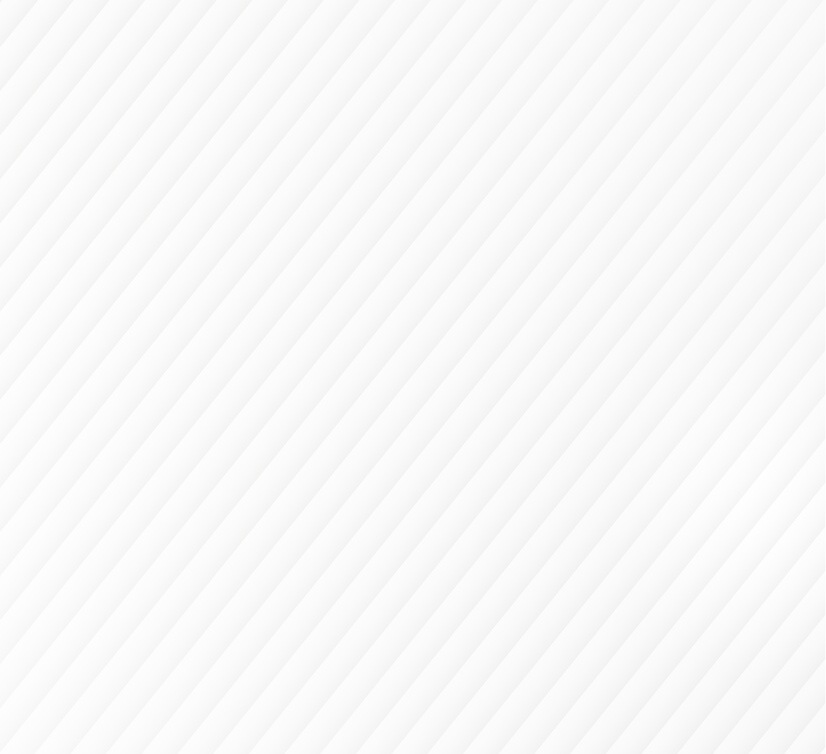
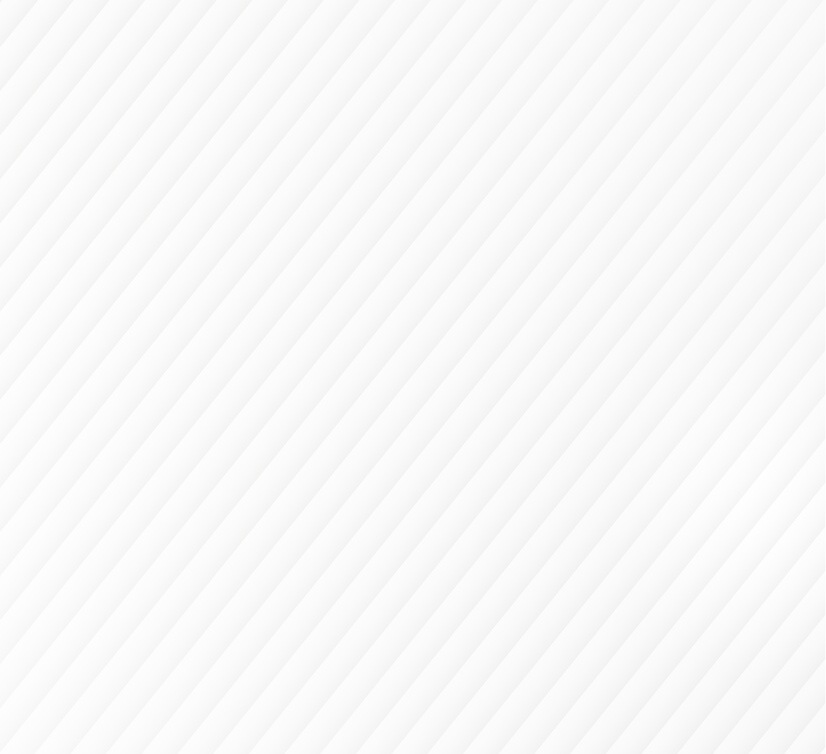
TIG welding process and quality certified at Asimer Group
At Asimer Group, we approach each TIG welding project by strictly following the welding specifications provided by the client in the corresponding project, as well as the Inspection Test Plan (ITP), which outlines the WPS (Welding Procedure Specification) and PQR (Procedure Qualification Record) to be followed. This ensures that our projects meet the highest standards of quality and durability.
Our experienced team of welders, highly skilled in TIG welding and backed by ISO 3834-2 certification, plays two fundamental roles: repairing cast parts (correcting porosities or defects from machining processes) and performing special overlays (using nickel and cobalt-based materials). These solutions are renowned for their high surface resistance and certified quality.
Each TIG weld begins with a thorough preparation of the materials and the welding area. Our welders rely on specialized cleaning equipment to remove any surface contaminants that could compromise the quality of the weld. In addition, preheating techniques are used to maintain optimal temperatures in the welding area, mitigating the risk of cracks and defects.
Once the welding area and filler materials are prepared, the key moment arrives: the TIG welding process itself. Our skilled welders use non-consumable tungsten electrodes to create the welding arc, ensuring precise control over weld penetration and bead shape while managing passes and corresponding temperatures.
To protect the weld area from atmospheric contamination, we use high-quality inert gases such as argon or helium. These gases create an oxygen-free environment around the welding arc, preventing the formation of oxides and ensuring clean, high-quality welds.
Throughout the welding process, we meticulously monitor the temperature and filler material feed rate to ensure proper fusion and uniform heat distribution. The final result is a robust joint that complies with industry standards.
After welding, each joint undergoes a rigorous inspection process to ensure its quality and integrity. We employ non-destructive testing methods such as VT (Visual Testing) and PT (Liquid Penetrant Testing), and for more demanding requirements, volumetric tests such as radiographic inspections (Rx) to detect any defects. This ensures that each component meets our stringent quality standards and complies with customer requirements, typically based on ASME or UNE-ISO standards.
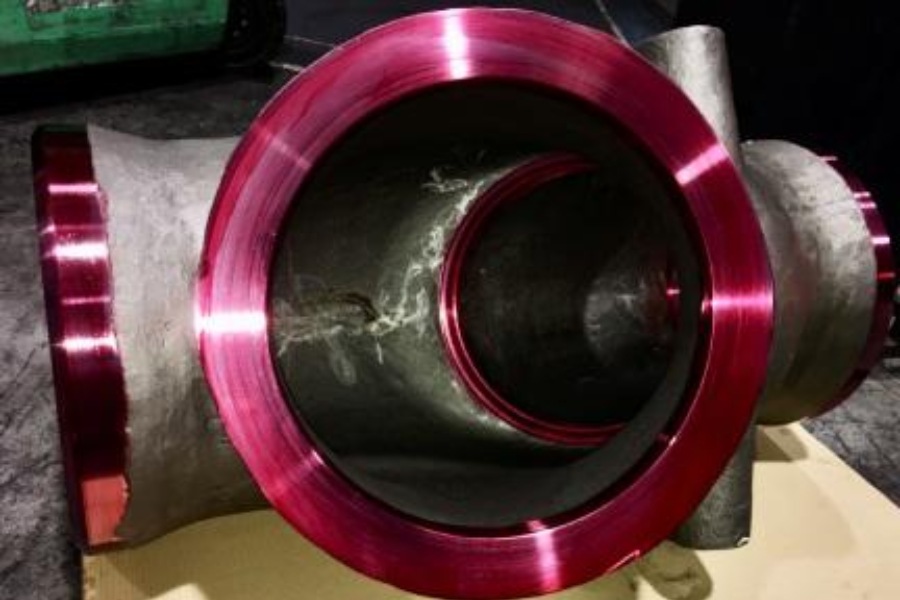
Energy efficiency in industrial valves
To maximize energy efficiency in industrial valves, Asimer Group is committed to implementing cutting-edge technologies in TIG welding and CNC machining. Our expertise in valve, industrial pump, and compressor projects allows us to offer customized solutions that not only meet the highest quality standards but also optimize energy consumption in industrial processes. By integrating advanced welding and machining techniques, we ensure that every component manufactured by Asimer Group contributes to the energy efficiency of industrial operations. With a focus on innovation and sustainability, we continue to lead the way toward a more efficient and sustainable future in the industrial valve industry.
Quality certification- ISO 3834-2
Asimer Group holds the UNE-EN ISO 3834-2 Certification, ensuring meticulous quality control at every stage of the welding process. This standard sets rigorous criteria to guarantee excellence in the fusion of metallic materials.
Approvals and welding processes
Our company takes pride in having 100 Welding Procedure Specification (WPS) approvals in compliance with ASME or EN-ISO-15614 standards. These certifications are a testament to our ability to meet the most demanding industry specifications. Additionally, our welding processes undergo a series of rigorous non-destructive tests required by our clients, including liquid penetrant inspections, ultrasonic testing, magnetic particle analysis, and hardness measurements.
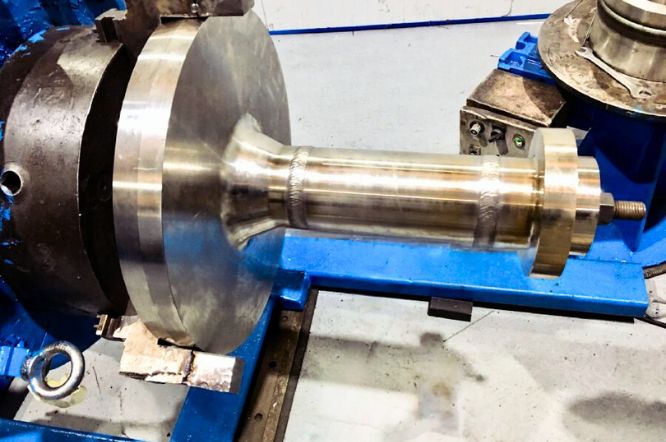
Advantages of TIG welding
High quality
Our dedication to quality leads us to use TIG welding, resulting in clean, flawless and highly corrosion resistant welds, ensuring the longevity and reliability of welded products.
Efficiency and productivity
TIG welding allows us to produce components quickly and efficiently, minimizing production times and maximizing productivity. In addition, it requires little or no post-processing work, allowing us to deliver finished products on time and within budget.
Versatility
TIG welding allows us to work with a wide range of materials, including carbon steels, stainless steels, cobalt base materials (stellite), nickel base materials (Alloys) and duplex and superduplex, This allows us to tailor our products to each customer’s unique needs.
Innovation and technology
We are committed to staying ahead of the industry by investing in state-of-the-art TIG welding equipment, which enables us to provide our customers with cutting edge engineering solutions that meet their most demanding expectations.
Advantages of TIG welding
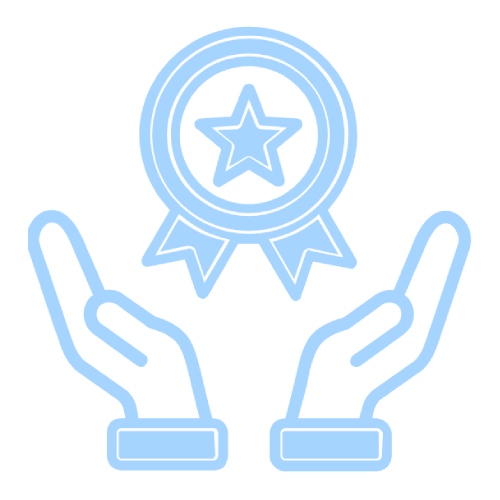
High quality
Our dedication to quality leads us to use TIG welding, resulting in clean, flawless and highly corrosion resistant welds, ensuring the longevity and reliability of welded products.
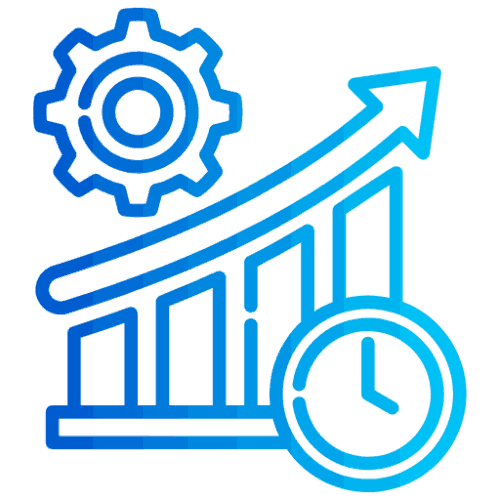
Efficiency and productivity
TIG welding allows us to produce components quickly and efficiently, minimizing production times and maximizing productivity. In addition, it requires little or no post-processing work, allowing us to deliver finished products on time and within budget.
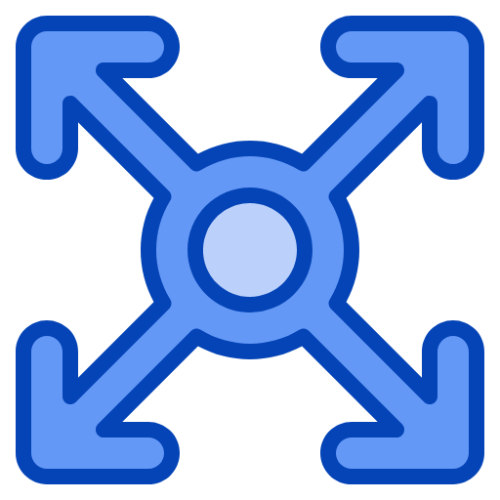
Versatility
TIG welding allows us to work with a wide range of materials, including carbon steels, stainless steels, cobalt base materials (stellite), nickel base materials (Alloys) and duplex and superduplex, This allows us to tailor our products to each customer’s unique needs.
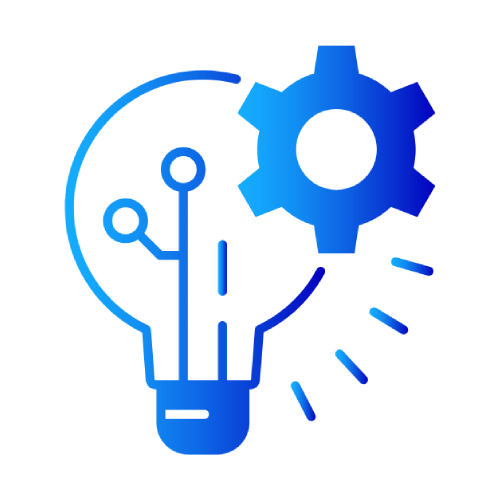
Innovation and technology
We are committed to staying ahead of the industry by investing in state-of-the-art TIG welding equipment, which enables us to provide our customers with cutting edge engineering solutions that meet their most demanding expectations.
Applications of TIG welding at Asimer Group
Our commitment to quality and innovation has positioned us as leaders in pump, industrial valve, and compressor projects for these critical applications. TIG welding is applied in various areas at Asimer Group, where we take pride in offering cutting-edge TIG welding solutions for a wide range of sectors, including oil & gas, naval, pulp and paper, petrochemical, cryogenics, desalination, water, and wastewater. Our experienced team and advanced welding techniques ensure durable and reliable products that meet the highest industry standards.
In this regard, TIG welding is used in the manufacturing of centrifugal pumps and diaphragm pumps for a wide range of industrial applications, as well as in the production of control and safety valves for fluid processing systems. Additionally, it is utilized in the fabrication of piping and duct system components for the transportation of chemicals, oil and gas, and other industrial fluids, ensuring the quality and durability of every manufactured product.
Industrial pumps
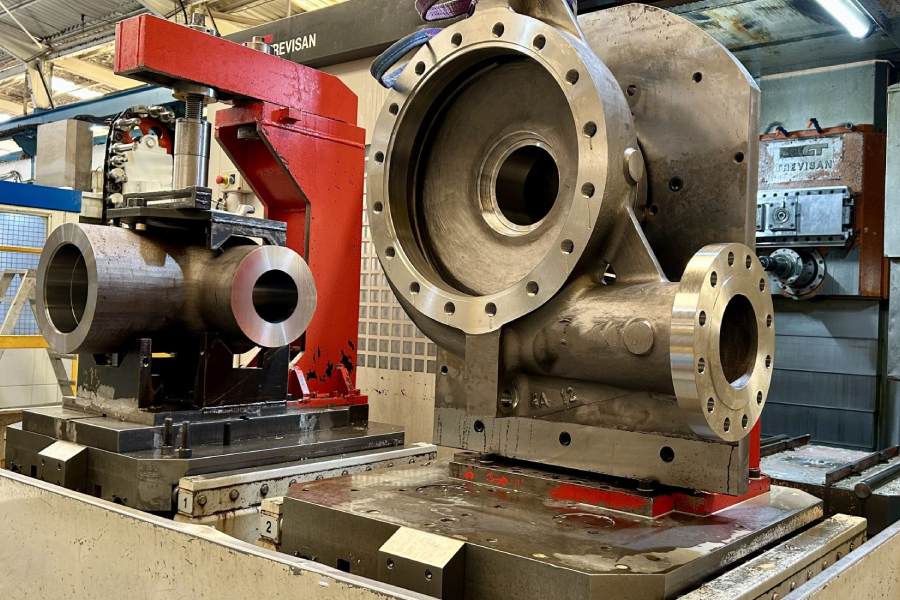
We use TIG welding to manufacture pump components that require high precision and corrosion resistance.
Industrial valves

Valves in the chemical and petrochemical industries significantly benefit from TIG welding due to the need for robust, corrosion-resistant connections in demanding environments.
Critical structures
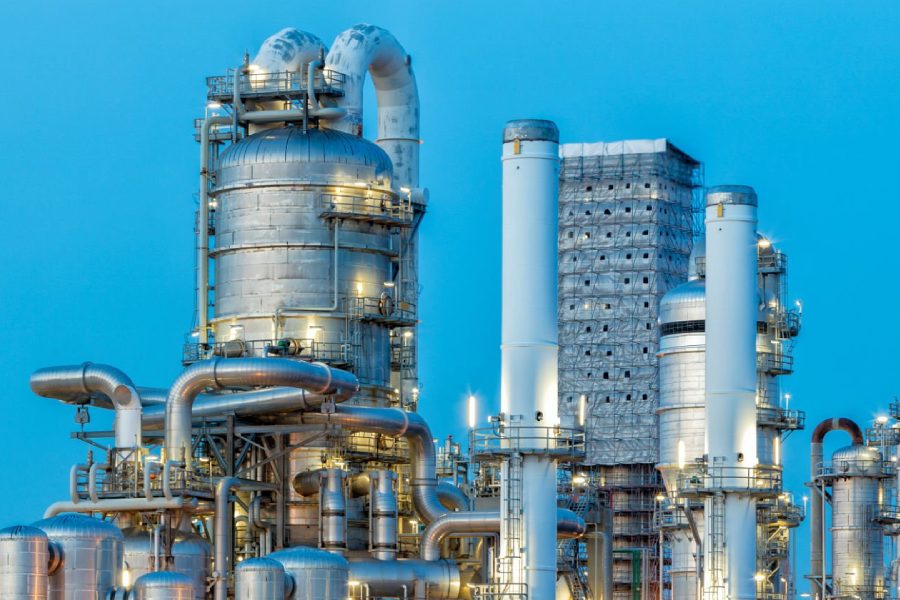
TIG welding is ideal for the fabrication of critical structures in chemical and petrochemical plants where structural integrity is essential.
Featured TIG welding projects
Why choose us?
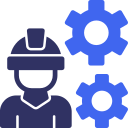
Experience in industry
With years of experience, we have worked closely with manufacturers of industrial valves and pumps to provide customized and efficient solutions. From welding axial flow check valves crucial in systems that require precise control of fluid flow in a single direction and with applications across various industrial sectors to the welding of cryogenic pumps and cryogenic valves, among many other types, we offer solutions tailored to the specific applications of the industry. These innovative technologies are integrated into our manufacturing processes, supported by rigorous quality controls and ISO 3834-2 certifications, ensuring excellence in every product we deliver.
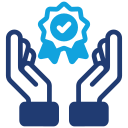
Quality commitment
Our procedures and materials meet the highest standards required by industry.
 
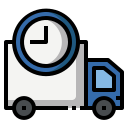
On-time delivery
We are aware of the importance of time in the industry. We commit to meet delivery deadlines rigorously.
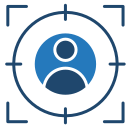
Customized approach
Each project is unique. We work closely with you to understand your requirements and adjust our solutions accordingly.
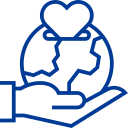
Sustainable approach and social commitment
Beyond our engineering and machining expertise, we are committed to sustainable practices and corporate social responsibility at Asimer Group.
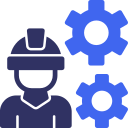
Experience in industry
With years of experience, we have worked closely with industrial valve and pump manufacturers to provide customized and efficient solutions. From welding axial flow check valves, crucial in systems requiring precise fluid flow control in a single direction and with applications in various industrial sectors, to welding cryogenic pumps and cryogenic valves, among many other types, we offer solutions tailored to industry-specific applications. These innovative technologies are integrated into our manufacturing processes, backed by rigorous quality controls and ISO 3834-2 certifications, ensuring excellence in each product we deliver.
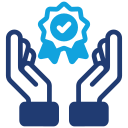
Quality commitment
Our procedures and materials meet the highest standards required by industry.
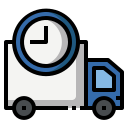
On-time delivery
We are aware of the importance of time in the industry. We commit to meet delivery deadlines rigorously.
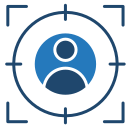
Customized approach
Each project is unique. We work closely with you to understand your requirements and adjust our solutions accordingly.
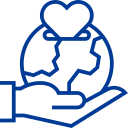
Sustainable approach and social commitment
Beyond our engineering and machining expertise, we are committed to sustainable practices and corporate social responsibility at Asimer Group.
We are constantly seeking ways to minimize our environmental impact and contribute positively to the communities in which we operate. This holistic approach ensures that we not only deliver quality products but do so ethically and responsibly.
At Asimer Group, our Metrology and quality inspection room stands as a testament to our commitment to sustainability and social responsibility. Equipped with state-of-the-art technology, including advanced measuring and testing instruments, this facility not only guarantees the precision and quality of our products but also plays a crucial role in our sustainability strategy.
By identifying and correcting potential defects in the early stages of production, we not only improve product quality but also reduce waste and optimize resource utilization. Our focus on total quality reflects our corporate ethics of providing reliable and durable products, thus strengthening long-term business relationships and contributing to customer satisfaction.
Guided by these principles, we will continue advancing in our mission to provide world-class engineering solutions while contributing to the sustainable development of the industry and society at large. At Asimer Group, excellence, innovation, and responsibility are the pillars of our continued success.