Liquid penetrant tests are an indispensable tool in the inspection industry and a form of non-destructive testing (NDT). This method is widely used to assess the integrity of critical structures in various industries, including metals, plastics, ceramics, and glass. In this article, we will thoroughly explore the process of liquid penetrant tests, their applications, advantages and disadvantages, and how they compare to other non-destructive testing methods.
What are liquid penetrant tests
Definition and purpose
Liquid penetrant tests are chemical substances designed to be applied to the surface of a material to identify surface discontinuities, such as cracks, pores, and fissures. These liquids are characterized by their low surface tension, allowing them to infiltrate small surface defects. After an adequate penetration period, the excess liquid is removed, and a developer is applied that absorbs the penetrant liquid from the discontinuities, making them visible.
History and evolution
Since their inception, the use of liquid penetrant tests has proven to be a valuable tool in preventive maintenance and the evaluation of critical components. The use of liquid penetrant tests began in the 1940s, developed as an efficient alternative to visual inspection methods. Over the years, improvements in formulations and techniques have optimized both the accuracy and safety of this process.
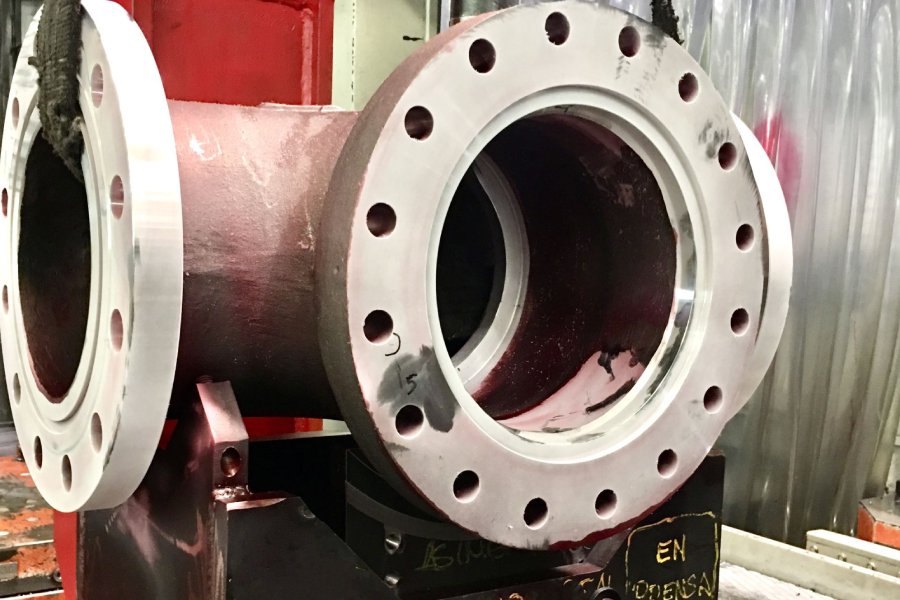
Liquid penetrant tests inspection process
- Step 1: Surface Preparation
Proper surface preparation is essential. This stage is critical because any contaminants can hide or mimic defects, leading to incorrect results. The material surface must be completely clean and free of contaminants such as grease, oil, paint, or dust. The cleaning method depends on the type of material and the contaminant to be removed. This is achieved through mechanical or chemical cleaning techniques, depending on the type of material and the nature of the residues present.
- Step 2: Application of the Penetrant Liquid
Uniform application of the liquid is crucial to avoid the formation of uninspected areas. The penetrant liquid is applied to the material’s surface using various methods, such as spraying, dipping, or brushing. Ensuring complete coverage is vital so the liquid can penetrate all existing discontinuities.
- Step 3: Penetration Time
This period must be carefully adjusted to ensure the liquid has enough time to infiltrate all discontinuities without drying on the surface. This is the time during which the penetrant liquid must remain on the material’s surface. The penetration period varies depending on the type of penetrant liquid used and the material under inspection and is crucial for effective defect detection.
- Step 4: Removal of Excess Penetrant
After the penetration time is up, it is vital to remove only the excess liquid and not the penetrant within the defects, as this could obscure them. This removal can be done by rinsing with water, solvent cleaning, or using clean towels.
- Step 5: Application of the Developer
The developer acts as a contrast agent, enhancing the visibility of the indications the penetrant highlights on the material’s surface. The developer is applied to the inspected surface to extract and absorb the penetrant liquid from the discontinuities, making any defects visible.
- Step 6: Visual Inspection
The visual inspection must be conducted in a well-lit area or under light specifically designed to highlight the penetrant indications. Finally, a detailed visual inspection is performed under appropriate lighting, depending on the type of penetrant liquid used.
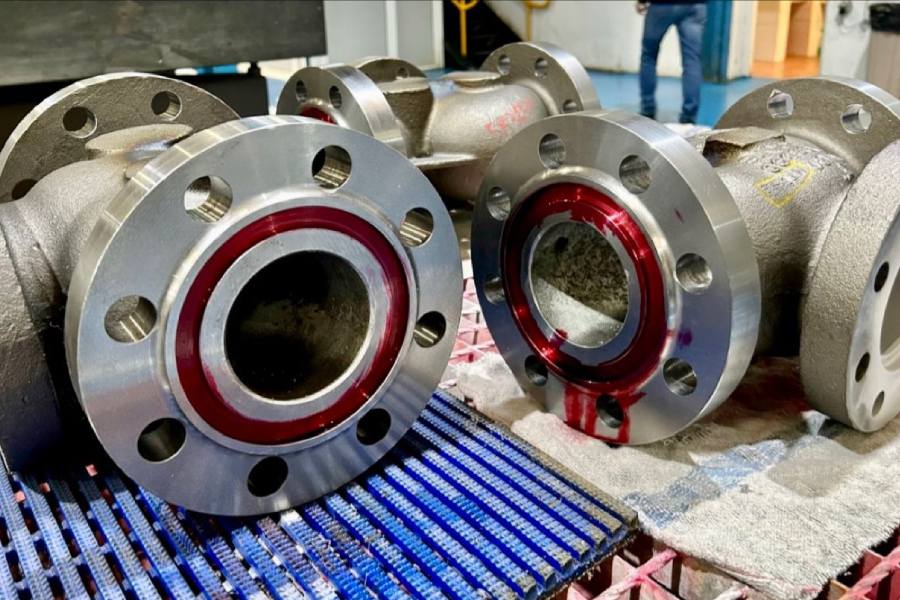
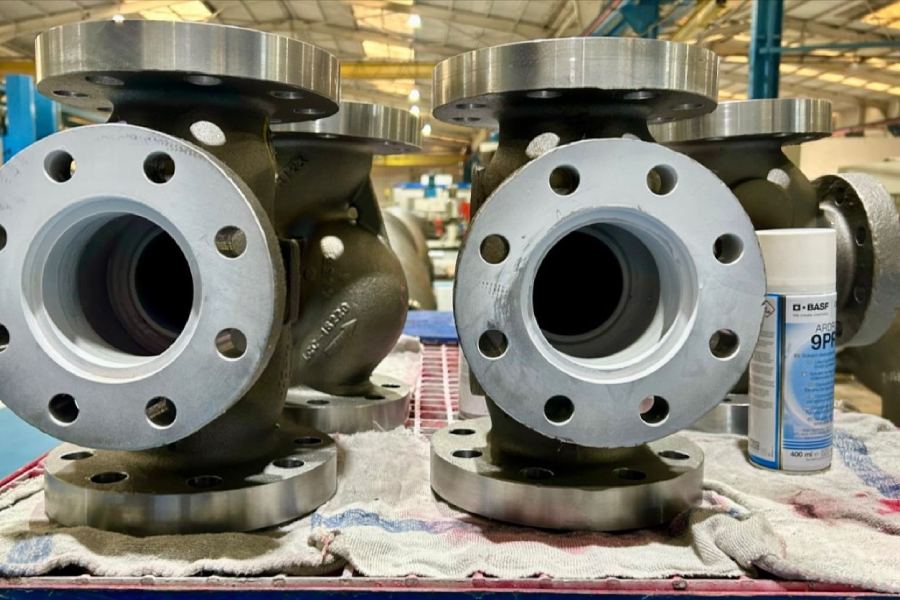
Applications of liquid penetrant testing
Industries using liquid penetrant tests
Liquid penetrant tests are used in various industries, including:
Aerospace
In the aerospace industry, the safety and reliability of components are crucial due to operational and safety demands. Liquid penetrant tests are used to inspect a variety of critical parts:
- Critical Components:
Wings, fuselages, and landing gear are essential parts of an aircraft that require regular inspection to detect cracks or defects that could compromise their performance and safety. Penetrant inspections can reveal micro-cracks in the material that could be dangerous if not detected in time.
- Welds:
Welds in structural components of aircraft undergo significant stress during flight. Liquid penetrant tests help identify defects such as surface cracks or lack of fusion in welded areas, ensuring structural integrity is maintained.
- Repairs and Maintenance:
During aircraft repairs or maintenance, liquid penetrant tests allow for quick and effective evaluation of repaired surfaces, ensuring the repairs are correctly done and free of hidden defects.
Automotive
In the automotive industry, liquid penetrant tests are used to ensure the quality and safety of a wide range of components:
- Engine Parts:
Critical engine components such as cylinder blocks, heads, and cast aluminum parts are inspected to detect cracks or defects that could affect engine performance or cause failures. Early detection of these defects can prevent catastrophic engine failures.
- Chassis and Structural Components:
The chassis structures and other vehicle parts are subjected to constant loads and stresses. Liquid penetrant tests are used to identify defects in welds, joints, and structural metal parts that could compromise vehicle safety.
- Body Repairs:
Damaged and repaired vehicles are also inspected to ensure the repairs have not left surface defects that could weaken the body integrity.
Construction
In construction, liquid penetrant tests are applied to verify the quality and safety of structural elements:
- Metal Structures:
Steel structures used in buildings, bridges, and other constructions are subjected to heavy loads. Liquid penetrant tests are used to detect surface defects in beams, columns, and other metal pieces, helping to prevent structural failures.
- Welds:
Welds in metal structures and construction elements must be inspected to ensure they are free of cracks and defects. Liquid penetrant tests allow for accurate evaluation of weld quality.
- Bridges and Other Infrastructure:
Bridges and other infrastructures require regular inspections to ensure their safety.Liquid penetrant tests are a useful tool for detecting defects in steel and other construction materials.
Manufacturing
In manufacturing, liquid penetrants tests are used to ensure the quality and reliability of produced parts:
- Metal Parts:
During the manufacturing process of metal parts, liquid penetrants tests are applied to detect surface defects such as cracks, porosity, and other issues that could affect part performance. This is crucial to ensure parts meet quality standards.
- Plastic Parts:
Although less common, liquid penetrant tests can also be used on certain plastic parts to detect surface defects that could affect functionality. This is especially relevant for high-performance components that must meet strict specifications.
- Quality Control:
The use of liquid penetrant tests in quality control during and after manufacturing helps identify and correct defects before parts are shipped to the customer, reducing the risk of product failures.
Cryogenics
In the cryogenic industry, liquid penetrant tests are used to inspect equipment and components operating at low temperatures, ensuring structural integrity and the absence of defects that could cause failures in extreme conditions.
- Cryogenic Components:
Storage tanks and pipelines transporting liquefied gases such as nitrogen and oxygen require regular inspection to detect cracks or defects that could compromise their performance and safety. Penetrant inspections can reveal micro-cracks in the material that could be dangerous if not detected in time.
- Valves and Pumps:
Valves and pumps in cryogenic systems are subjected to extreme conditions that can cause surface cracks or corrosion. Liquid penetrant tests help identify these defects, ensuring equipment functions safely and efficiently.
- Refrigeration Equipment:
During the maintenance of cryogenic refrigeration equipment, liquid penetrant tests allow for quick and effective evaluation of surfaces, ensuring no hidden defects that could affect performance.
Oil and Gas
In the oil & gas industry, liquid penetrant tests are essential for inspecting pipelines, storage tanks, and drilling components, detecting surface defects that could lead to leaks or catastrophic failures.
- Transport Pipelines:
Pipelines transporting oil and gas are subjected to severe pressures and environmental conditions. Liquid penetrant tests are used to detect cracks and corrosion in pipelines, preventing leaks and potential accidents.
- Storage Tanks:
Storage tanks for oil and chemicals require regular inspection to detect surface defects that could cause spills. Liquid penetrant tests allow for accurate evaluation of tank integrity.
- Drilling Equipment:
Drilling components such as bits and heads are exposed to extreme stresses. Liquid penetrants tests help identify cracks and other surface defects that could cause failures during drilling operations.
Petrochemical
In the petrochemical industry, liquid penetrant tests are applied to inspect processing equipment, pipelines, and pressure vessels, helping detect surface defects that could lead to leaks of hazardous substances or operational failures.
- Pressure Vessels:
Pressure vessels used in petrochemical processes must be inspected regularly to detect cracks and other defects that could compromise their safety. Liquid penetrant tests allow for early detection of these problems.
- Pipes and Ducts:
Pipes and ducts transporting chemicals need detailed inspections to ensure there is no corrosion or cracks that could cause leaks. Liquid penetrant tests are an effective tool for these inspections.
- Processing Equipment:
Reactors and distillation columns in petrochemical plants require precise surface evaluation to detect any defects that could affect the process. Liquid penetrant tests help ensure the quality and safety of this equipment.
Desalination
In desalination plants, liquid penetrant tests are applied to verify the quality and safety of structural elements, ensuring there are no surface defects that could affect operation and the quality of treated water.
- Saltwater Pipes:
Pipes transporting saltwater to the desalination plant are subject to corrosion and wear. Liquid penetrant tests help detect these problems before they cause system failures.
- Storage Tanks:
Tanks storing desalinated water need regular inspections to ensure there are no surface defects that could contaminate the treated water. Liquid penetrant tests allow for detailed evaluation of these tanks.
Processing Equipment:
Critical components of the desalination process, such as reverse osmosis membranes, require thorough inspection to ensure there are no cracks or damages that could affect their functionality. Liquid penetrant tests are ideal for these evaluations.
Naval
In the naval sector, liquid penetrant tests are used to inspect hulls, propellers, and other components, identifying surface defects that could affect vessel performance and safety.
- Ship Hulls:
Ship hulls are constantly exposed to adverse conditions, which can lead to cracks and corrosion. Penetrant testing allows for detailed inspection of the hull surface to detect these defects.
- Structural Welds:
Welds in the ship’s structure must be inspected to ensure they are free from cracks and defects. Penetrant testing offers precise evaluation of the quality of these welds.
- Mechanical Components:
Mechanical components, such as propellers and rudders, require inspection to detect any surface defects that could affect the vessel’s performance and safety. Penetrant testing is an effective tool for these inspections.
Water Treatment
In water treatment and desalination plants, this method is used to inspect pipes, tanks, and processing equipment, ensuring there are no surface defects that could affect operation and the quality of treated water.
- Water Pipes:
Pipes that transport water throughout the plant are subject to wear and corrosion. Penetrant testing helps identify these problems in a timely manner, ensuring safe and efficient operation.
- Storage Tanks:
Tanks that store treated water must be regularly inspected to ensure there are no surface defects that could compromise the water quality. Penetrant testing allows for a detailed evaluation of these tanks.
- Processing Equipment:
Filters, pumps, and other processing equipment need thorough inspection to detect cracks and other surface defects. Penetrant testing is ideal for these evaluations, ensuring the proper functioning of the water treatment system.
Pulp and Paper
In the pulp and paper industry, penetrant testing is used to ensure the quality and safety of equipment and products, detecting surface defects that could affect the performance and integrity of produced items.
- Paper Machines:
Paper machines, such as cylinders and rollers, are subject to constant wear. Penetrant testing allows for the detection of cracks and other surface defects that could affect the quality of the produced paper.
- Processing Equipment:
During the pulp and paper manufacturing process, penetrant testing is applied to detect surface defects in processing equipment, ensuring there are no issues that could compromise process efficiency.
- Pipes and Tanks:
Pipes and tanks used in the pulp and paper processing need regular inspections to detect corrosion and other defects. Penetrant testing allows for detailed evaluation of these components, ensuring their integrity and functionality.
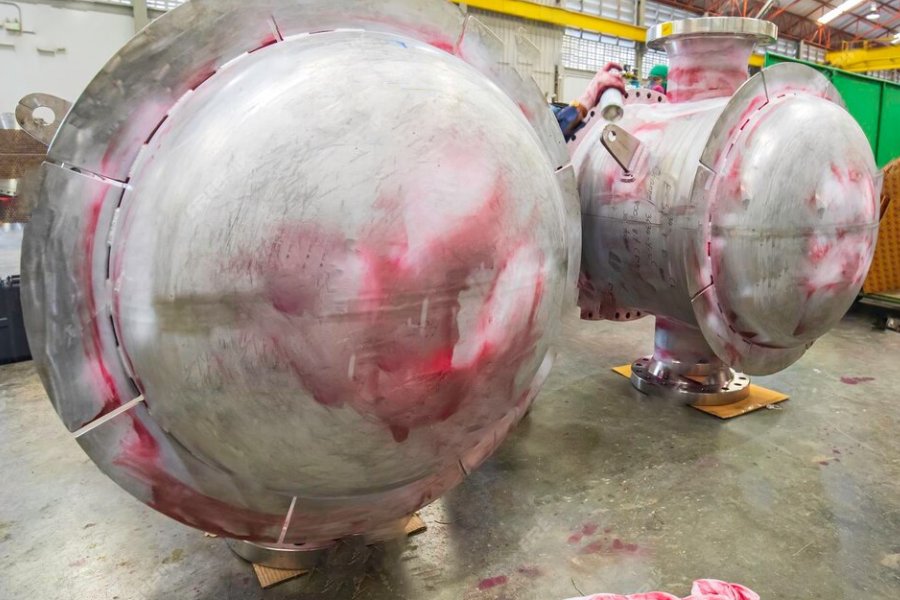
Types of detectable defects
This method is effective in detecting a wide range of surface defects, such as:
- Fatigue cracks
- Porosity
- Fissures
- Welding defects
- Delaminations
Advantages and disadvantages of liquid penetrant test
Advantages
- High Sensitivity: Liquid penetrant tests can detect even the smallest surface discontinuities, making them highly effective for quality control.
- Versatility: They can be used on a wide range of non-porous materials, including metals, ceramics, and plastics.
- Simplicity: The process is relatively simple and does not require highly specialized equipment.
- Cost-Effective: It is a cost-effective method compared to other NDT techniques.
- Quick Results: Penetrant liquid inspection provides immediate results, allowing for rapid decision-making.
Disadvantages
Surface Limitation: Liquid penetrant test can only detect surface defects and are not effective for internal discontinuities.
- Material Restrictions: This method is not suitable for porous materials, as the penetrant may not be effectively removed.
- Environmental Considerations: The chemicals used can be hazardous and require proper disposal and handling to minimize environmental impact.
- Preparation Time: The process requires thorough cleaning of the material’s surface, which can be time-consuming.
- Operator Dependence: The accuracy of the inspection largely depends on the skill and experience of the operator.
Comparison with other NDT methods
Penetrant Liquid vs. Radiography
- Surface vs.Internal: While liquid penetrant tests are effective for detecting surface defects, radiography can reveal internal discontinuities.
- Safety: Liquid penetrant tests are generally safer to use as radiography involves exposure to radiation.
- Cost: Penetrant liquid inspection is typically more cost-effective compared to radiography.
Penetrant Liquid vs. Ultrasonic Testing
- Surface Sensitivity: Liquid penetrant tests are more sensitive to surface defects, while ultrasonic testing can detect both surface and internal discontinuities.
- Equipment: Penetrant liquid inspection requires less specialized equipment compared to ultrasonic testing.
- Application: Ultrasonic testing is suitable for a wider range of materials, including those that are porous or have complex geometries.
Penetrant liquid vs. magnetic particle testing
- Material Type: Liquid penetrant tests can be used on non-ferromagnetic materials, whereas magnetic particle testing is limited to ferromagnetic materials.
- Surface Defects: Both methods are effective for detecting surface defects, but magnetic particle testing can also detect near-surface discontinuities.
- Sensitivity: Penetrant liquid inspection is generally more sensitive to small surface cracks and discontinuities.
Conclusion
Liquid penetrant tests are an invaluable tool in the arsenal of non-destructive testing methods. Their ability to detect surface defects with high sensitivity and versatility across various materials makes them indispensable in ensuring the safety, reliability, and quality of critical components in many industries. While there are certain limitations and considerations, the benefits of this method make it a preferred choice for many applications. Understanding the nuances of the penetrant liquid inspection process, its advantages, and its comparison with other NDT techniques can help industries make informed decisions about the most appropriate testing methods for their specific needs.
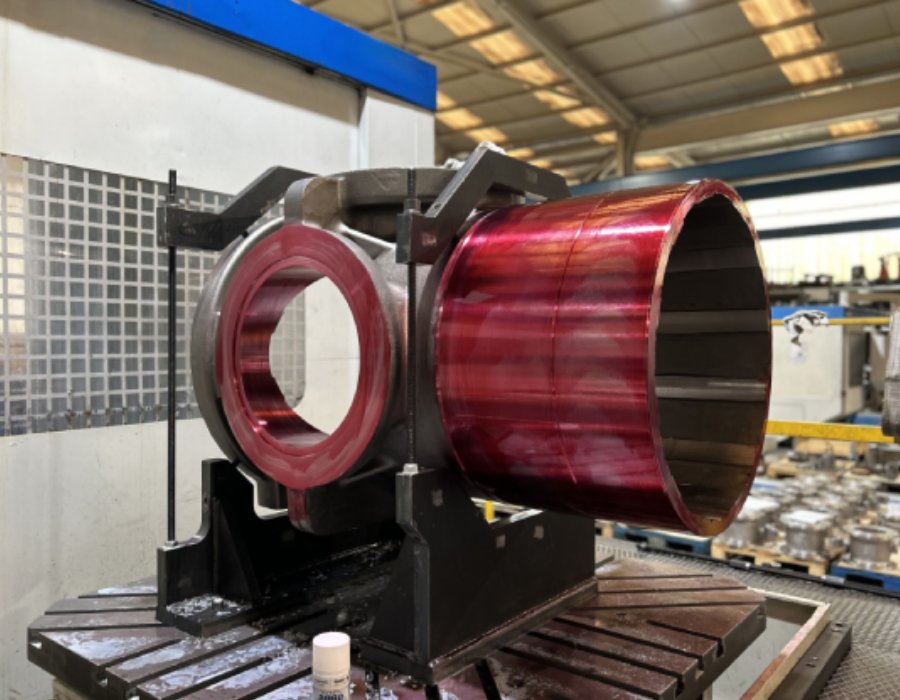