Outsourcing machining and welding in the Oil & Gas industry has become a key solution to ensure efficiency, speed, and precision in environments where every second counts. In this sector, where operational pressure is at its peak and technical failures can lead to million-dollar losses, having access to specialized services makes the difference between a prolonged shutdown and a rapid recovery.
At Asimer Group, we understand that outsourcing is not just a matter of resources but a strategic decision to ensure operational continuity, technical quality, and regulatory compliance.
When it comes to maintaining the reliability of pumps, valves, or compressors operating under extreme conditions, maintenance teams face several simultaneous challenges: tight deadlines, deteriorated critical components, difficulty manufacturing complex or discontinued parts in-house, and the need to comply with strict technical regulations.
To meet these demands, Asimer Group designs and executes technical solutions specific to each critical component that arrives at our facilities. Whether through CNC machining processes, certified welding, or specialized coatings, we work on elements such as flow control valves, axial flow check valves, industrial piping systems, or diaphragm valves, always adapting to the specific requirements of each client.
These components typically operate in demanding environments such as petrochemical plants, naval systems, or Oil & Gas installations, where effective technical intervention makes the difference between a long stoppage or immediate recovery. They are also common in applications involving fittings and critical parts exposed to extreme conditions, especially in the energy and petrochemical sectors.
Challenges of industrial maintenance in the oil & gas industry
Equipment operating under extreme conditions
On offshore platforms, refineries, petrochemical, or cryogenic plants, industrial equipment is subjected to aggressive conditions: high temperatures, constant pressure, corrosive fluids, cyclic loads, and explosive atmospheres.
These conditions accelerate wear and cause structural failures if not addressed quickly and precisely. We specialize in machining and welding industrial components on offshore platforms, where error margins are zero. We also offer industrial machining services in refineries, tailored to the precision, safety, and speed requirements of these critical facilities. Additionally, we have experience in extreme environments, such as those requiring cryogenic valves for transporting and controlling gases at very low temperatures, or in machining large-diameter valves.
Recurring failures in pumps, valves, and compressors
In facilities with industrial pumps, damage from cavitation, vibration, or demanding operating conditions is common—especially in systems operating under continuous pressure, such as a centrifugal pump. These issues also affect components like butterfly valves, which suffer wear due to frequent opening or corrosive conditions. In many of these cases, we apply specific welding techniques for corrosive environments that extend service life and reduce downtime.
Components such as casings, shafts, covers, seats, or impellers often suffer from erosion, cavitation, corrosion, or cracks. Many of these damages cannot be fixed in-house, especially when specialized welding or high-precision machining is required. The repair of industrial pumps demands high-precision welding processes and deep knowledge of operating conditions. Proper inspection and control of these elements can prevent failures, ensuring tightness in critical areas. That’s why we use non-destructive testing and techniques like dye penetrant inspection to verify the integrity of each component.
In-house limitations in maintenance and manufacturing
Not all plants have advanced CNC technology, qualified personnel, or the capacity to apply special coatings. And even when resources are available, they are often overloaded or the turnaround time doesn’t allow waiting. In such cases, outsourcing processes to a specialized technical partner like Asimer Group enables quick recovery of operability with precision and technical assurance. Additionally, as an indirect benefit, improvements in energy efficiency in industrial valves can be achieved, which is also critical for operational continuity.
Benefits of outsourcing machining and welding in critical environments
One of the key technical approaches we apply is chip removal machining, ideal for ensuring precision in parts subjected to wear or strict dimensional requirements.
Outsourcing does not mean losing control. On the contrary, when you have a trusted technical partner, outsourcing becomes an efficient extension of your maintenance or engineering department, bringing speed, precision, and solutions tailored to your operational context. Industrial maintenance outsourcing allows plants to focus on their core activity without giving up technical control. In many cases, subcontracting industrial machining represents a strategic solution when seeking specialization, regulatory compliance, and reduced response times.
Reduced lead times and improved operability
Compared to in-house manufacturing or waiting for OEM spare parts, outsourcing the machining or repair of a critical component reduces downtime and restores system functionality in days—or even hours. In industries like pulp and paper, desalination, or water treatment, every minute matters.
Access to advanced technology without internal investment
Partnering with a specialized provider gives access to state-of-the-art machining centers, automated welding processes, high-resistance coatings, coordinate measuring systems, and dimensional control with traceability. In this regard, having infrastructure like our metrology room is crucial to ensure precision in every inspection. We also use high-precision measuring instruments like the measuring arm to ensure compliance with technical specifications. All of this is supported by connected environments aligned with the principles of Industry 4.0.
Increased reliability in critical parts
A poorly repaired part may fail again. With an applied engineering approach, outsourced machining and welding solutions not only restore geometry but also optimize functionality, material, and durability of components. This applies to parts as well as industrial piping systems that require reinforcement or coatings to withstand corrosive or abrasive conditions. The entire process begins with the correct selection of machining tools and techniques tailored to each need.
Specialized outsourcing helps reduce lead times, ensure exact tolerances, and increase reliability in demanding industrial environments.
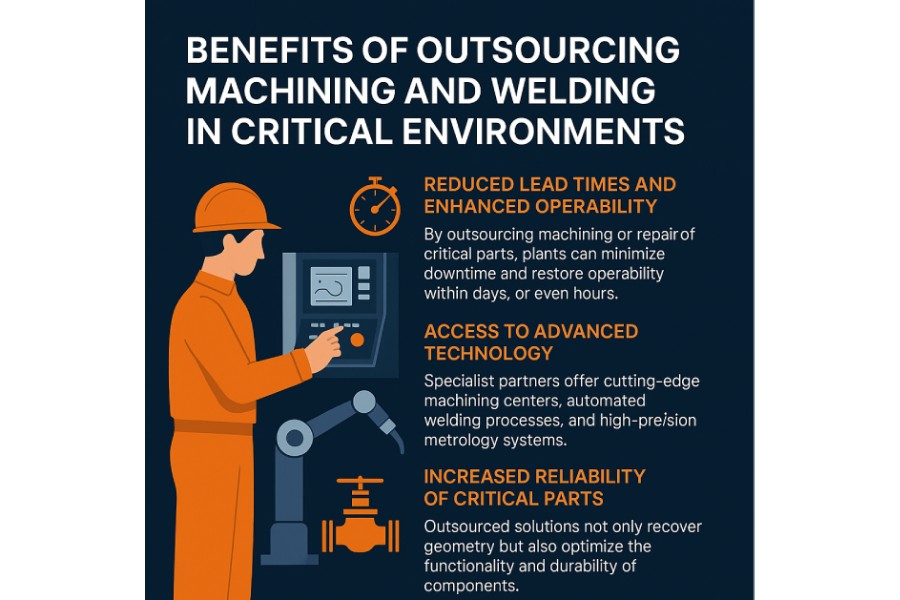
How Asimer Group leads technical outsourcing in oil & gas
At Asimer Group, we understand that every plant shutdown is a race against time. That’s why we offer our Oil & Gas clients a unique combination of technical capacity, precision technology, and experience in extreme environments.
Precision CNC machining for complex parts
Our experience includes machining pumps and valves in stainless steel, where precision, strength, and surface finish are key to ensuring performance in aggressive environments.
We have high-capacity machining centers, applying high-precision machining processes for the Oil & Gas sector. This infrastructure guarantees the precision required by critical sectors like Oil & Gas—whether from drawings, samples, or reverse engineering. We guarantee exact tolerances and optimal finishes. We have CNC machining technology for industrial valves operating in highly corrosive environments. We also machine components for offshore platforms, with solutions adapted to the technical standards of the energy sector. You can learn more about our capabilities in the Trevisan machining center, which plays a key role in the production of complex parts and CNC machining projects geared toward high-precision machining for cryogenic applications in industrial pumps and valves.
MIG, TIG, and PTA welding for extreme conditions
Our experience in specialized MIG welding allows us to restore or reinforce critical parts with metallic overlays resistant to corrosion, abrasion, and high temperatures. We also use automated MIG welding equipment, ideal for ensuring repeatability, quality, and speed in projects where every minute counts. Additionally, we apply PTA welding techniques to components requiring high performance against wear, especially in aggressive fluid pumping applications. We work with stainless steels, special alloys, and demanding materials. We use TIG welding in the Oil & Gas sector to ensure the integrity of critical components under pressure.
Applied engineering for component recovery
We don’t just execute processes—we design technical solutions. We rework geometries, improve thicknesses, redesign fluid flow paths, or reinforce structural areas. This way, a damaged component can come out stronger thanks to our engineering solutions designed to optimize costs in machining pumps and valves or even reduce the carbon footprint in industrial valves and pumps.
Dimensional control and guaranteed traceability
We rely on advanced metrology technology such as portable measuring arms, 3D scanners, or inspection rooms to ensure that every part meets the required dimensional specifications.
Real Cases of Successful Outsourcing in Machining and Welding
Machining and welding of swing check valves for french oil & gas customer
At Asimer Group, we completed a project for 16” 150# BW Swing Check valves for a French client specializing in high-engineering valves for the Oil & Gas sector. The scope included all critical process phases: pre-machining, non-destructive testing using dye penetrant (PT) in pre-machined areas, welding operations according to ASME standards, and in compliance with WPS and PQR procedures validated under an ITP (Inspection and Test Plan).
Asimer Group holds the ISO 3834-2 certification, ensuring compliance with the highest welding quality standards.
Final machining and NDT (PT and VT) were then carried out by Level II certified operators. Swing Check valves provide reliable performance in demanding petrochemical applications thanks to an optimized design that prevents backflow, improves sealing, and reduces friction wear. Their construction ensures long service life, low emissions, and optimized flow capacity for high-temperature and high-pressure services.
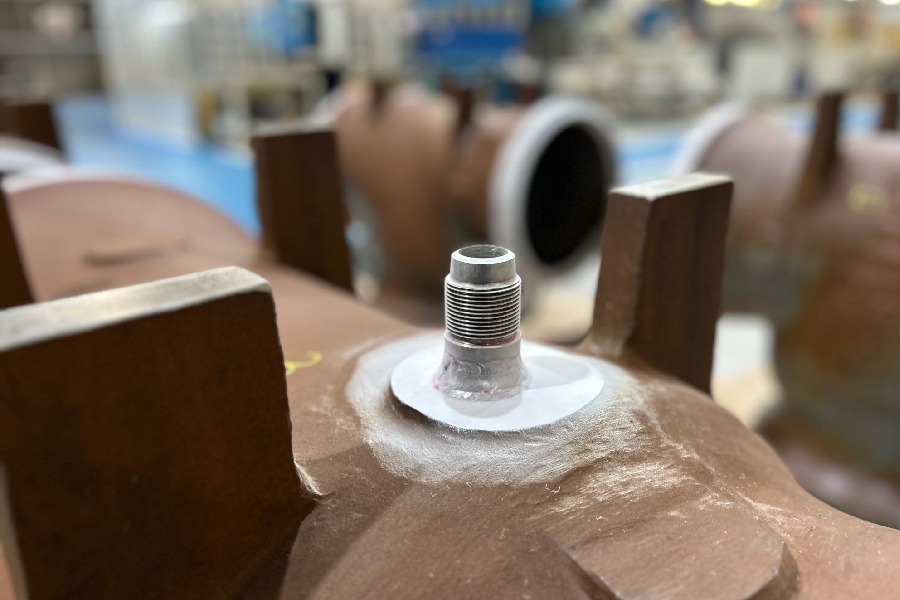
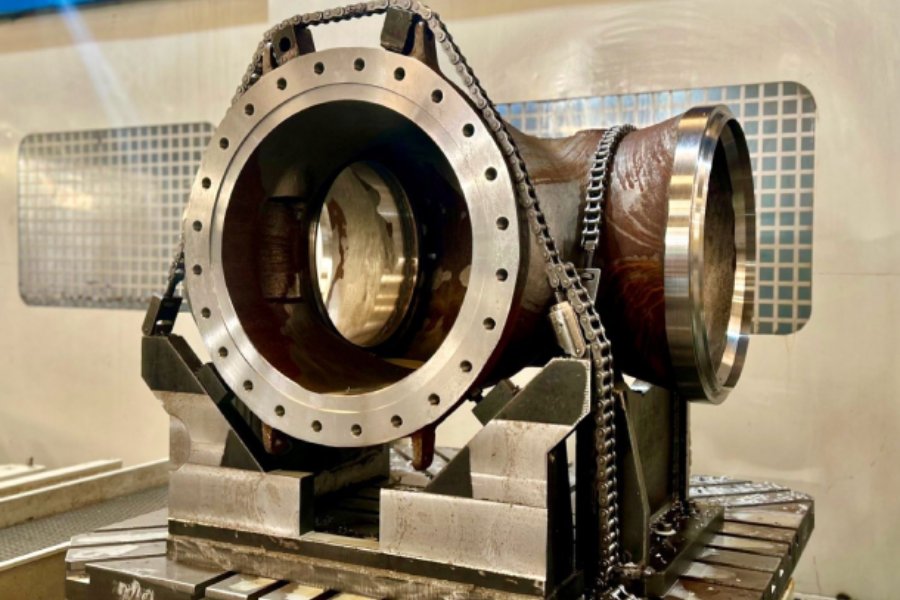
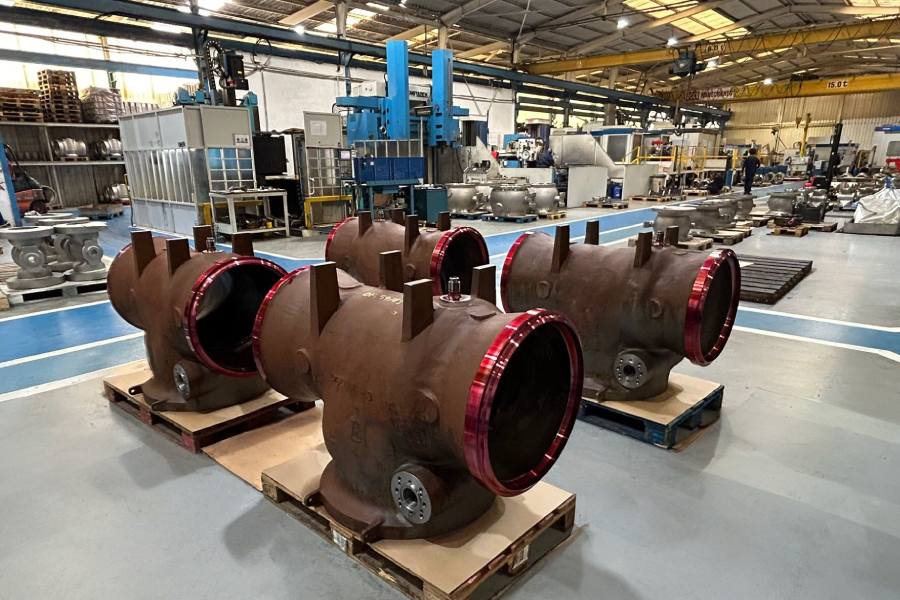
20” trunnion ball valve project for french oil & gas customer
Another standout project developed by Asimer Group involved producing five 20” 300# Trunnion-type ball valve bodies for a French end customer specializing in Oil & Gas solutions.
The scope included full management of material procurement, with A182 F44 forged rings certified 3.2, non-destructive testing, final precision machining, and final tests (PT, VT, and PMI) in the presence of TÜV certification body, all in accordance with inspection plans (ITP).
This type of valve stands out for its robustness, ease of operation, and low torque. Thanks to its trunnion-supported design, it offers excellent sealing performance even at high pressures, reducing seat wear and extending system service life.
Final machining and dimensional control of 20” 300# Trunnion valve bodies, developed by Asimer Group under technical outsourcing criteria for an energy sector client in France.
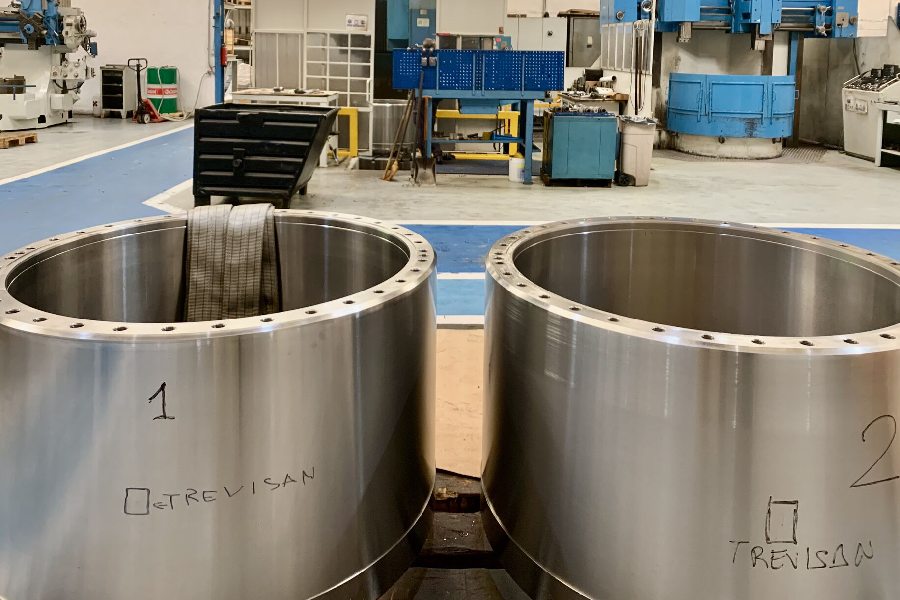
When to Outsource Machining and Welding Processes?
Knowing when to outsource is just as important as knowing who to outsource to. In sectors like Oil & Gas, where there’s no room for error, identifying the right time can be the difference between shutting down or continuing production.
Urgent or unplanned downtime
If a pump or valve fails unexpectedly and there’s no immediate replacement, outsourced machining or welding can restore functionality in record time.
Lack of technical capacity or tight deadlines
When internal infrastructure lacks sufficient resources or staff is overloaded, outsourcing relieves the system without affecting production.
Discontinued parts or no original drawings
In older or discontinued equipment, many parts are no longer available on the market. Asimer Group can replicate or improve them through reverse engineering.
Do you need to outsource the machining or welding of your components?
Check ✔ if any of these apply:
- You have a damaged critical part (pump, valve, piping, or compressor)
- You’re facing an urgent or unplanned technical shutdown
- Your internal workshop is lacking resources or overloaded
- You need to recover a part that’s no longer manufactured
- You work with special materials (stainless steel, superalloys, etc.)
- You require certified welding or technical coatings
- You must meet strict dimensional tolerances
- You can’t afford errors in pressure- or corrosion-sensitive equipment
💡 If you’ve checked at least 2 boxes, it’s time to contact a technical partner like Asimer Group.
Outsourcing is not subcontracting: It’s gaining control, quality, and efficiency
At Asimer Group, we don’t see outsourcing as a last resort, but as a strategic decision based on technical trust. We don’t compete on price—we compete on lead times, precision, and expertise.
Outsourcing with us means keeping control of the process, with the peace of mind that every part will be treated as if it were our own. We are your technical ally so you never have to stop production due to lack of solutions.
Restore your operations with precise, fast, and safe solutions.