What is Non-Destructive Testing (NDT)?
Non-Destructive Testing (NDT) is a test and analysis technique used in the industry, and especially in the industrial valve and pump sector, to evaluate the properties of a material, component and/or metal structure in search of discontinuities and/or irregularities in them, without causing damage to the original part.
In industry, non-destructive testing plays a crucial role in assessing the integrity of critical equipment and components. Did you know that these tests are also essential in the inspection of key components in industrial pumps?
Non-destructive testing is any test performed on a material that does not change its physical, chemical, mechanical, or dimensional properties. Various non-destructive test methods are based on physical phenomena such as electromagnetic, acoustic, elastic waves, subatomic particle emission, capillarity, absorption and/or any type of test that does not cause serious damage to the test sample.
In general, ENDs provide less precise information about the state of the variable that is being measured than destructive tests. However, since it does not involve the destruction of the inspected part, in many cases it is the only inspection option, for example in sectors such as the automotive sector where it is necessary to inspect 100% of the manufactured parts, or inspect welds or pipes in sectors such as petrochemicals.
In the fascinating world of machining and welding, non-destructive testing plays a fundamental role in ensuring the integrity of manufactured parts. These tests allow for the detection of possible hidden defects without compromising the quality of the material, thus avoiding costly errors and potential structural failures. However, the importance of non-destructive testing is not limited solely to defect detection but also extends to the rigorous process of accuracy in CNC machining. In this sense, the implementation of non-destructive techniques contributes to ensuring that specified tolerances and measurements are met precisely and reliably. Precision in machining is a paramount requirement in the industry, and by combining it with the application of non-destructive testing, an integral approach is achieved that guarantees quality and reliability in the production of components and structures. Furthermore, to carry out these tests accurately and efficiently, it is crucial to have high-quality and precise measuring instruments, which play a crucial role in the metrology room. This metrology room becomes the heart of the inspection, ensuring that the parts meet the required standards.
When we delve into the realm of non-destructive testing and its vital importance in the industry, it is crucial to highlight how having advanced facilities, such as the Trevisan Machining Center, becomes an essential asset. These facilities, equipped with cutting-edge technology, play a pivotal role in the manufacturing of precise components, ensuring integrity and quality in non-destructive tests. This, in turn, contributes to safety and efficiency in various industrial sectors.
The convergence of non-destructive testing and Industry 4.0 along with the CNC Machining Revolution adds a new chapter to this story. Industry 4.0 has revolutionized manufacturing, ushering in the era of connectivity and intelligence. This synergy transforms the evaluation of materials and structures, catalyzing efficiency and precision in detecting potential defects. Learn more about how this alliance is shaping the future of industrial inspection and advanced manufacturing in our comprehensive article on Industry 4.0 and the CNC Machining Revolution at Asimer Group.
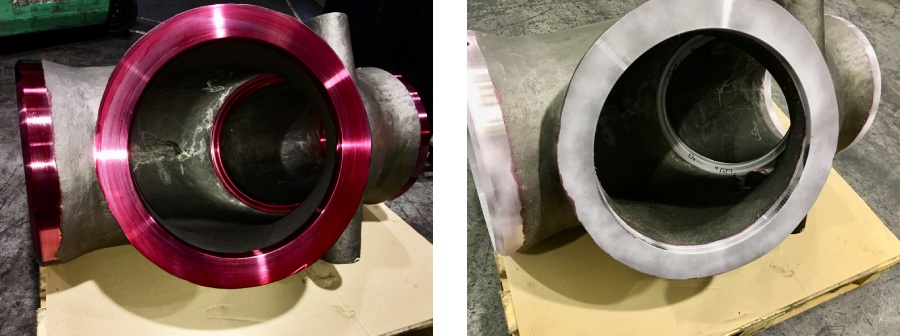
Welding Non Destructive Testing
With non-destructive testing, major and minor weld defects can be easily identified in each component that is tested. Without any required assumptions from visual inspection, the component can be used safely without compromising industrial operation or human life.
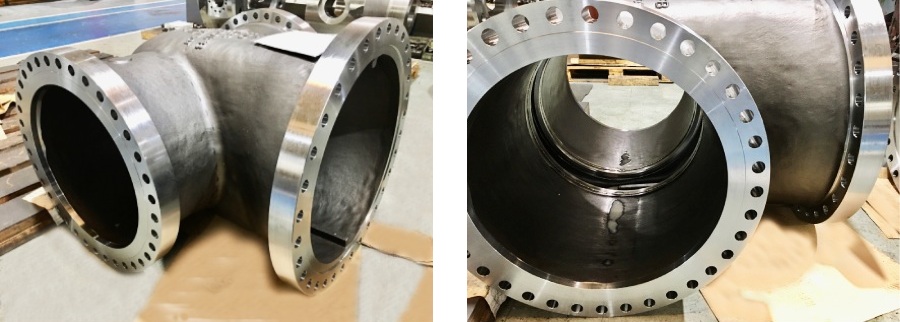
To ensure that welds meet quality and safety standards, different organizations have established guidelines, including the American Society for Nondestructive Testing (ASNT), the International Standard for Organizations (ISO), and the American Petroleum Institute (API). In certain industries and countries, understanding these guidelines is vital for analysts to ensure safety standards and maintain effective welding operations.
What is the difference between destructive and non-destructive testing?
Destructive testing destroys or changes the piece in some way, so that, if it passes the test, it is no longer fit for service.Some examples may be tensile tests, 3-point flexion tests, or macro section. ENDS do not destroy or change the part so that it remains fit for service if it passes the test.
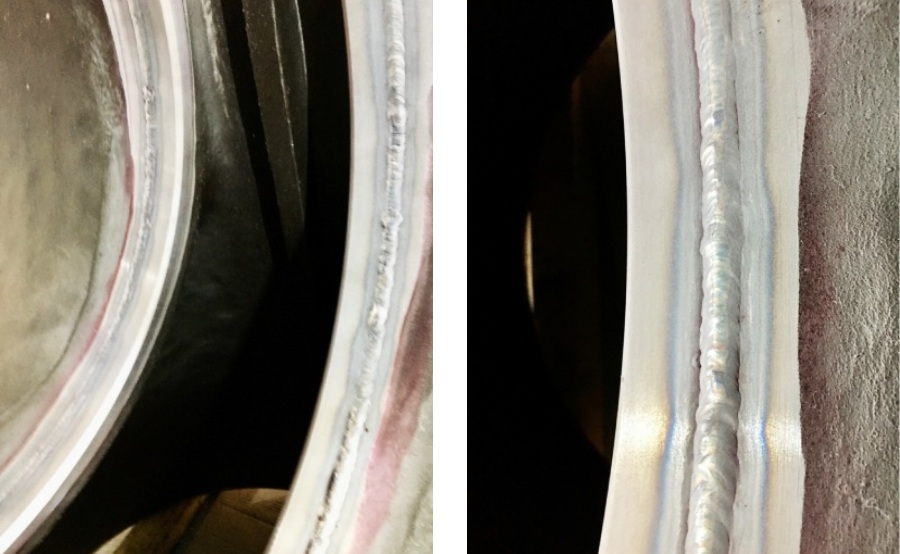
What are the advantages of using END?
There are a number of advantages. The most obvious is that the parts that are being tested are not damaged during the process, allowing an item to be repaired rather than replaced if a problem is found.
It is also a very safe testing method for operators, as the majority of the techniques are harmless to humans, although some types of testing, such as radiographic testing, still need to be done under strict conditions. This testing technique can also help prevent injury or death by ensuring that structures, components, and machinery are safe.
Non-destructive testing is also a very accurate form of inspection, as the tests are repeatable and multiple tests can be used together to correlate the results.
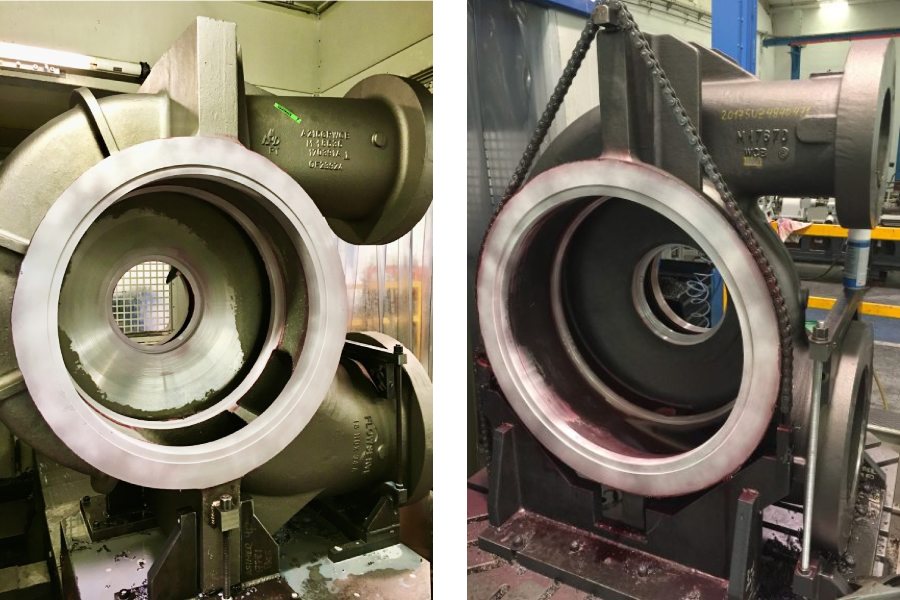
These test methods are also inexpensive. Unlike destructive testing, END is profitable as it can avoid the need to replace an item before a malfunction occurs without destroying the part itself.
This testing technique also offers operators peace of mind, knowing that the equipment is working as it should, preventing future accidents, and determining steps that can be taken to extend useful life.
It is also useful for verifying welding procedures and for ensuring that a welding process has been completed to the correct specification within the limits of quality control, for example, to ensure that the base metal has reached the correct temperature, cooled to specified rate and that compatible materials have been used to avoid weld defects.
The main NDT groups
These tests provide information about the surface state of the inspected materials. The main methods are:
- VT – Visual Inspection,
- PT – Penetrating Liquids
- MT – Magnetic Particles
- UT – Ultrasound Test
In the case of using VT and PT, they serve to detect only superficial discontinuities (open to the surface); while with MT and UT it is possible to detect both surface and subsurface discontinuities (those found just below the surface).
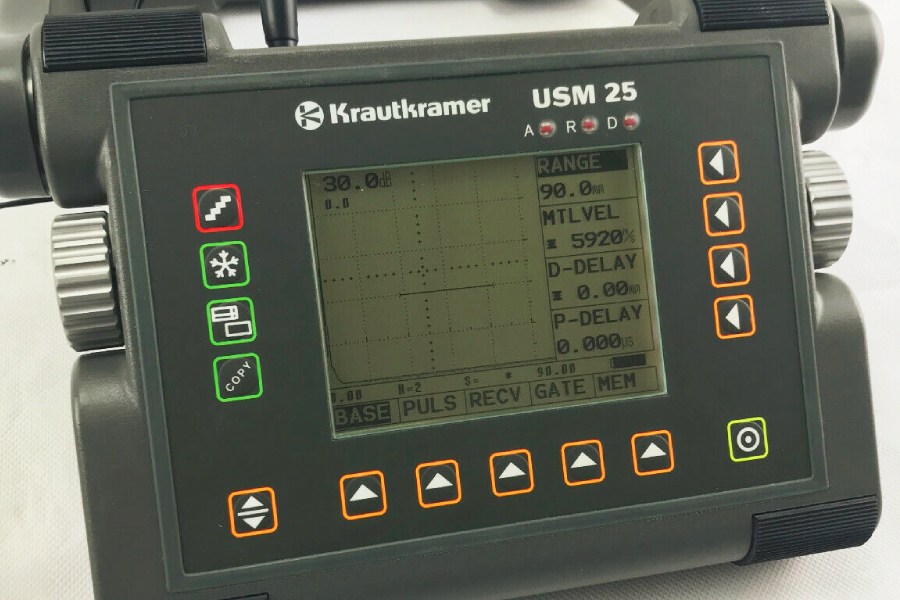
Where is Non-Destructive Testing used?
It is used in most industries, including aerospace, automotive, power, marine, and oil & gas.
The industry is increasingly adding to the use of this type of test not only for the final inspection of manufactured parts, but also to control production processes. An example of this can be found in the automotive industry, especially in the control of welding points, where welding points are usually inspected using ultrasound. This ensures that the point is welded correctly.
The trend in NDT is to use techniques that allow greater automation and detection of defects, location and dimensions without human intervention.
Therefore, techniques such as magnetic particles or fluid penetration, where workers must judge whether or not defects exist, are being replaced by other techniques that also allow for computerized recording of results.
Starting with the Zero inspection that is carried out before the element goes into operation and managing the data of each inspection to see the evolution of the defects and decide if it is necessary to increase or otherwise, reduce the inspection interval. If possible, devices and sensors are also installed in the most critical places, which monitor failures in real time and can take the necessary measures without maintenance shutdowns.
Operator qualification levels in Ends
A person certified to carry out ENDs must be classified, based on their training, in one of the three levels indicated below.
Level 1
Certified workers as Level 1 have demonstrated their qualification to carry out NDT operations according to written instructions and under the supervision of Level 2 or Level 3 operators. They may be authorized by the employer to perform the following jobs:
- Carry out the tests.
- Adjust the NDT equipment.
- Register and classify the results in written terms.
- Report on the results. It will not be responsible for the choice of the test technique to be used, nor for the interpretation and evaluation of the corresponding results.
Level 2
The level 2 certified operator has demonstrated his ability to carry out and supervise the END in accordance with established procedures. It may be authorized by the employer to:
- Choose the END technique to be used during the trial.
- Define the limitations of the application of the test method.
- Understand the NDT standards and specifications and transform them into instructions adapted to real working conditions.
- Conduct and supervise trials.
- Adjust equipment and check settings
- Interpret and evaluate the results in accordance with applicable standards, codes, procedures or specifications.
- Prepare written essay instructions.
- Perform and supervise all tasks of level less than or equal to level 2.
- Provide assistance to operators below or equal to level 2.
- Report the results of non-destructive tests.
Level 3
A person certified as level 3 has demonstrated their ability to carry out and direct any operation in the NDT methods and sectors for which they are certified. Likewise, it has sufficient technical competence to manage, supervise, and establish criteria in all the test techniques included in the method in which it is certified.
The Integration of CNC Technology and Non-Destructive Testing in the Industry
In the continuous pursuit of enhancing quality and safety in the industry, non-destructive testing plays a crucial role. From defect detection to assessing material integrity, these tests are essential across numerous sectors, including the petrochemical industry. Exploring how CNC technology integrates with non-destructive testing processes can shed light on new ways to enhance efficiency and quality in this field. In this regard, the convergence of CNC machining precision and non-destructive defect detection offers a promising horizon for modern manufacturing.
In the manufacturing industry, the integrity of each component is paramount. Non-destructive testing is the primary tool to ensure this integrity, allowing for early detection of defects without compromising product quality. By linking this article with “Chip Removal Machining in the CNC Era,” we can explore how these tests are integrated into manufacturing processes to ensure excellence in every product.
Therefore, it invites us to delve into this fascinating intersection of technologies and processes in our upcoming comprehensive article on “CNC Technology: Enhancing the petrochemical industry with efficiency and quality.“
Asimer Group’s experience in Ends
At Asimer Group, we have been very familiar with ENDs for more than 15 years. Market demands (both for the valve and for the industrial pump) have made us increasingly demanding with all non-destructive tests, mainly for 2 reasons:
- Non-destructive tests on machining casting parts.
A large number of the total parts machined at ASIMER Group refer to parts from casting. Parts whose origin is foundry, are susceptible to suffer incidents at the surface level, which can be mitigated with ENDs prior to final machining under drawing.
Thanks to the fact that ASIMER Group has qualified Level II personnel for certain ENDs, it can offer this type of services to its final clients, mainly LPT, and VT.
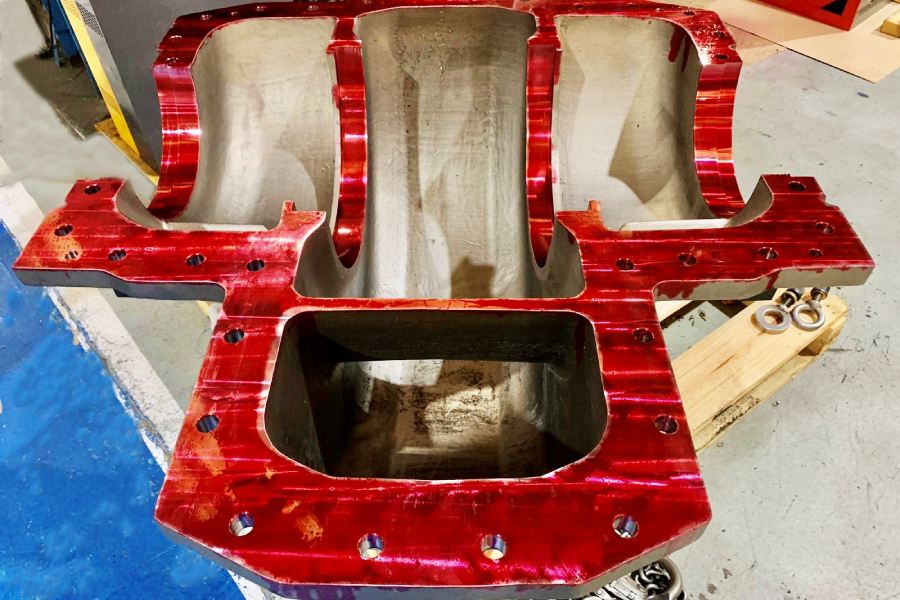
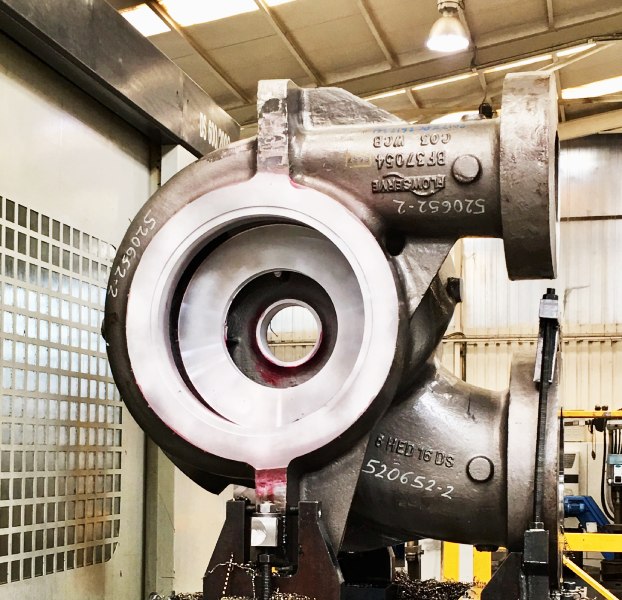
- Non-destructive tests on the piece with welding and/or provided with Overlay. Another significant amount of the parts that ASIMER Group supplies to its customers have welded or OVERLAY joints.
- Welded joints can occur, for example, in the welding of the rings to the corresponding bodies, mainly in gate, globe or retention bodies. With the LPI Inspection it is ensured that the quality of the welded joint is optimal.
- Another example where the use of ENDs is Mandatory refers to valve bodies with Overlay. ASIMER Group has carried out a large number of projects with Overlay, mainly carbon steel with Inconel 625 overlays. This type of project is ALWAYS subject to 2 groups of ENDs:
The VI (Visual Inspection) and LPI (Liquid Penetrant Test) tests make it possible to ensure that the recharged surface area conforms to the project requirements.