Measuring instruments: What are they and what are they for?
Measuring instruments are the backbone of metrology, and CNC machining is the technique that ensures their perfection. From the creation to the machining of each component, CNC machining contributes to the precision and reliability of measurement instruments in the industry.
The Measuring instruments are crucial in the industry to ensure accuracy and quality in component manufacturing. However, to achieve precise and reliable measurements, it is essential to have state-of-the-art facilities that support this process. This is where the Trevisan Machining Center plays a crucial role. By enabling the production of precise components with the latest technology, this center of excellence significantly contributes to the efficiency and reliability of measurement processes.
Throughout history, various measuring instruments have been developed, which, thanks to technological advancements, can now provide accurate and reliable measurements.
In the industrial context, precision is an essential characteristic that determines the reliability of measurement and control instruments. This quality is reflected in an instrument’s ability to deliver consistent and repeatable results, even under the same conditions in multiple measurements. In a precision-critical environment, such as manufacturing and quality control, an accurate instrument ensures measurement uniformity and consistency, allowing companies to maintain high-quality standards in their products and processes. Precision not only ensures reliable measurements but also contributes to efficiency, waste reduction, and ultimately meets customer expectations in industrial production.
The importance of Metrology
Metrology is the science of measurement and is the key to achieving accuracy. The aim is to provide accurate and therefore reliable measurements for commerce, health, safety and the environment. It is especially important in precision engineering where products must meet strict tolerances.
Metrology is used in many industries to enforce, validate and verify predefined standards. The metrology study is divided into 3 subfields that are used to ensure accuracy, reliability and precision.
- The ‘Applied, Technical or Industrial Metrology’ establishes the importance of measurement and maintenance, quality control and calibration of instruments.
- ‘Legal metrology’ refers to regulatory measurement requirements for consumers to be protected and fair trade is respected.
- ‘Scientific metrology’ establishes a common understanding of measurements and units. It is therefore vital to achieve high levels of accuracy and reliability, particularly for precision engineers.
There is another technique, known as “deterministic metrology” which replaces measuring parts by measuring processes.
An example of deterministic metrology is a new technique known as 3D error compensation for computer numerical control (CNC) systems.
This technology is adopted in high precision manufacturing, machinery and control systems, to achieve micro and nanotechnology accuracies.
The Importance of Metrology in Asimer Group: Integration of Industry 4.0 and CNC Machining
In the constant pursuit of excellence in metrology, Asimer Group not only stands out for its advanced measurement techniques but also leads the forefront of Industry 4.0 and the CNC Machining Revolution. In the fascinating world of Instrumentation and Measurement Equipment (IMES), where precision and technology are crucial, the convergence of these technological advancements is shaping a new era in measurement instrument manufacturing.
From creation to the machining of each component, CNC Machining technique contributes to the precision and reliability of measurement instruments in the industry. This process is further enhanced by the integration of Industry 4.0, marking a revolution in the efficiency and quality of IMES. Asimer Group leads this transformation, thoroughly exploring the implementation of cutting-edge technologies and the disruptive influence of Industry 4.0 in our dedicated article to this technological revolution.
Measuring and testing instruments in machining production
Measuring tools are used for the levelling and alignment of parts or for geometric or dimensional measurement of parts. When we measure, we compare a magnitude with a measurement reference, that measurement reference can be an external standard, or incorporated into the measuring device, as with the gauge. The accuracy of a measurement will depend on the error made in making it.
Accuracy is measured neither in microns nor in hundredths. Accuracy is measured according to the requirements of each part. The important thing is stability throughout the process.
Measuring equipment is a necessary but not sufficient condition to ensure machining according to the required precision.
The strategy in the measurement and the coordination between production and quality, are the way to conclude in an excellent work.
Classification of the measuring tools
The measuring equipment is classified into the following three groups.
- Meters
- Comparators
- Verifiers
The meters are the devices in charge of comparing the dimension to be measured with the unit of measurement. To this group belong the rulers, the flexometers, the gauges…
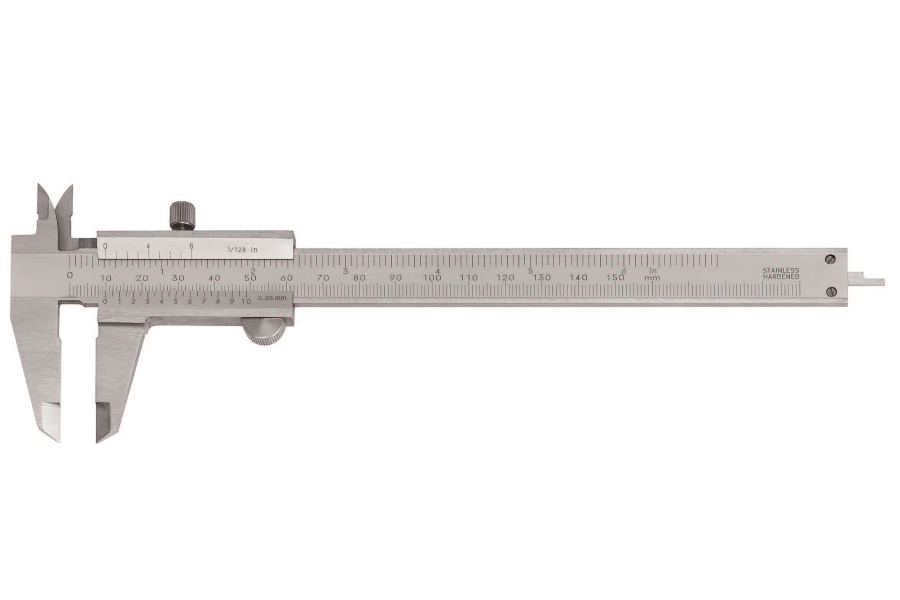
Comparators are basically used to compare dimensions. An example of this would be the dial gauge.
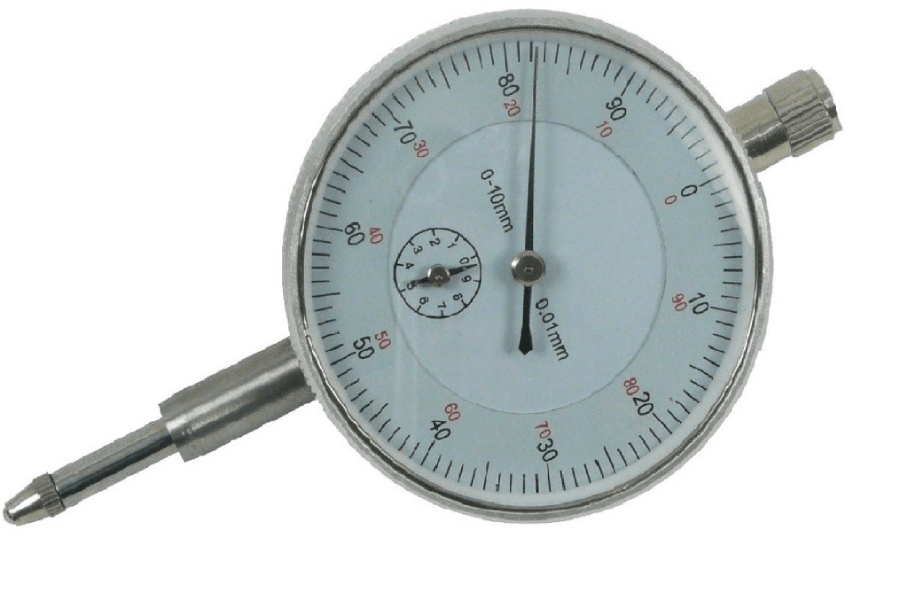
Verifiers are not used to make measurements, but to check whether the measurement is within limits or not.
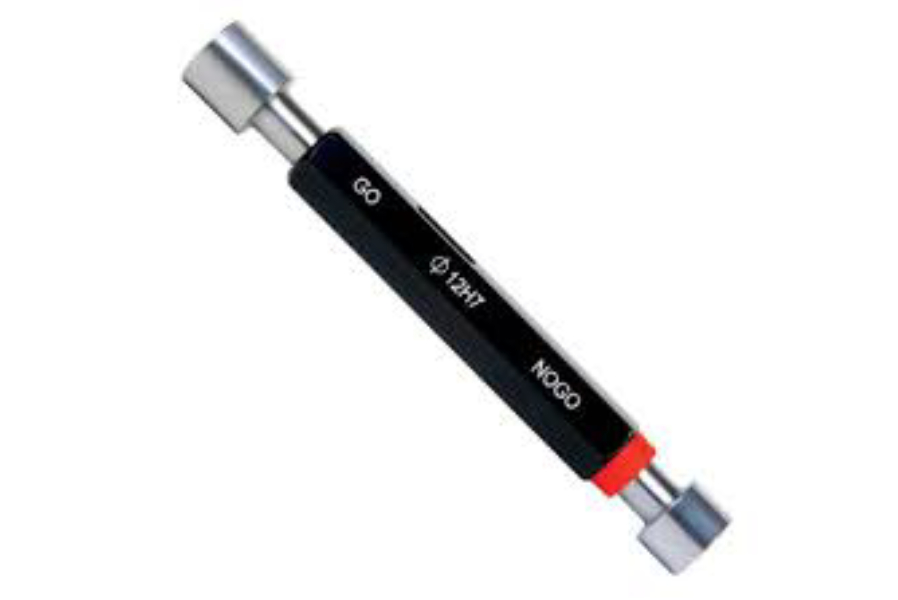
How are measurement instruments related to precision machining
In the field of CNC machining and TIG welding, measurement instruments are essential to ensure precision in part manufacturing and assembly. Precision machining, which is critical in various industrial sectors, requires a high level of accuracy in the dimensions of machined parts. Measurement instruments play a crucial role in verifying that these dimensions meet the required specifications, thus ensuring the quality of the final products.
TIG welding, being a widely used technique in metal joining, also demands precision to achieve strong and durable welds. From material preparation to final weld inspection, precise instruments are needed to ensure that dimensions and tolerances are appropriate. Any deviation in dimensions or alignment can compromise the structural integrity of the component, highlighting TIG welding’s sensitivity to precision.
In summary, measurement instruments are fundamental for both precision machining and TIG welding, ensuring the highest quality standards in the industry. Moreover, considering the importance of TIG Welding: The Cutting-Edge Solution for the Manufacturing of Industrial Pumps and Valves, its relevance as a cutting-edge solution for these specific applications is highlighted.
Dimensional measurements we make with measuring equipment
There are two methods to make measurements:
- The direct measurement
- The indirect measurement
In direct measurement, measuring devices such as gauges, micrometres and coordinate measuring machines are used to directly measure the size of an object. Measurements can be made within a wide range determined by the scale of the measuring device, but there is also the possibility that the measurement is incorrect due to incorrect readings on the scale.
In indirect measurement, dimensions are measured with measuring devices, such as spheres, that observe the difference between reference objects and devices, such as measuring blocks and measuring rings. They are also called reference measures because the comparison is made with an object of standard dimensions. The more predetermined the shape and dimensions of the reference device, the easier the measurement will be.
However, this method also has a limited measuring range. It is slow and laborious for the measurement of few parts and cost effective for the measurement of many.
Types of errors that occur in measurement
Length errors are the differences between the actual value of an object and the average value or the reference value and the measured value. They are expressed as “error = average value – true value”. In fact, it is difficult to obtain the real value regardless of the accuracy of the measurement, so the uncertainty of the average value is inevitable.
Errors can be classified into three types depending on the factor that causes the error. Such factors should be carefully considered to avoid errors.
Systematic errors
In this type of error, the measured value is biased for certain reasons.
Some examples include differences in measurements due to differences in individual instruments (instrument errors), temperature and certain measurement methods.
Random errors
This type of error is caused by random conditions during the measurement.
Errors due to negligence
This type of error is caused by inexperience or incorrect actions of the measuring staff.
Main causes of errors
Errors caused by the temperature
The volume of an object changes due to temperature fluctuations, which likewise leads to changes in the length of the object. This applies not only to the measuring object but also to the measuring instrument. Changes in temperature and length of an object can be expressed by the “coefficient of thermal expansion”. The coefficient of thermal expansion varies according to the type of material. ISO specifies the reference temperature for measuring length in 20°C (68°F).
Errors due to material deformation
Applying a force to an object causes it to change in a fixed proportion. The object returns to its previous state when no more force is applied. This change in shape of the object is called “elastic deformation”. The force applied to an object is called “stress”. In general, the ratio is proportional to the stress on the object. Therefore, this relation can be expressed by the “longitudinal modulus of elasticity (Young modulus)”.
The stronger the tension, the higher the tension. For example, when using an outdoor micrometre, be careful not to over-tighten the spindle when measuring the outside of the object.
Measuring units
In the machining production industry the unit of measurement is the millimetre (mm), as established by the Decimal Metric System. (The metric decimal system is a system of measurement having the metre and the kilogram as basic units, in which the multiples or submultiples of the units of the same nature follow a decimal scale).
It is also common to have to express measurements in inches.
The inch is a unit of length, which was, with different values, almost universal, and which is now used still and mainly in Anglo-Saxon countries (United States, United Kingdom, etc.). In almost all other countries, the metre is used as a measure of length. The inch equals 25.4 mm and is indicated with two quotation marks at the top right of the number.
The inch is divided into 16 parts, each of them equals 1/16 (a sixteen inch).
In the industrial valve and pump sector, the vast majority of the most common valve types and industrial pumps are measured by their size in inches, and their pressure in pounds, since many of the standards and norms on which they are governed come from Anglo-Saxon norms (American or British)
Main technicalities
- Calibration is the procedure of comparing what the instrument shows and what it “should show” with a standard of known value.
- Geometric measurement comes from the branch of mathematics that deals with the properties of geometric patterns in a plane or space, such as points, lines, planes, polygons, polyhedra, parallels, perpendiculars, curves, surfaces, etc.
- Levelling is a procedure to determine the level difference between two (or more) existing physical facts (blocks, columns, etc.). Several points (or levels) are compared with each other and their elevation in metres or centimetres is determined.
- Alignment is a procedure by which we compare the distance between two (or other) existing physical facts (bodies, pillars, etc.) in space.
- Tolerance can be defined as the allowed margin of error in the manufacture of a product. The higher the tolerance, the lower the margin of error
Types of measuring instruments in machining
The metro
It is a metal measuring tape with the shape of a half cane. Its lengths vary from 1 to 15 meters.
Graduated ruler
It is a measuring instrument in the shape of a thin metal or wooden plate, rectangular, which includes a graduated scale divided into units of length (centimetres or inches); it is a useful instrument for tracing straight segments in sheets or parts, with the help of the tip to trace. Their lengths are varied, ranging from 1 to 2 metres in length. They usually come with graduations of various units of measurement, such as millimetres, centimetres, and inches.
The plumb
It measures verticality and is formed by a body that acts as a counterweight, usually cylindrical, containing a rope axially for suspension of the body, at a fixed point. It is characterised because the rope is associated with a stop (two cones faced by their tips), equipped in its face of adaptation to the corresponding fixed support of a blind drill, in which is embedded and fixed a magnet of great power, in such a way that the fixing of the plumb line to the metal ruler, pillar or supporting element in question is occured automatically by simple approximation of the stop to it.
The tape measure
It is a measuring instrument, with the particularity that it is built in flexible sheet metal, divided into units of measurement (millimetres, centimetres, metres, etc.), and that is coiled inside a metal or plastic housing.
Squares and templates
A square is a template in the shape of a right angle (90 degrees) normally, although there are also other angles (120º). They can be of different sizes, materials and shapes.
Another variety of templates are feeler gauges, which are measurement verification instruments. They are made of alloy steel and are used to measure threads, thicknesses, drill angles, etc.
The level
It is a measuring instrument used to determine the horizontality or verticality of an element. There are different types, as it is a very useful instrument for construction in general; metal carpentry, aluminium carpentry, metal constructions, etc.
The principle of the level is in a small transparent tube (glass or plastic) which is filled with liquid with an air bubble inside ( the size of the bubble is less than the distance between the two marks). If the bubble is symmetrically between the two marks, the instrument indicates an exact level, which can be horizontal, vertical or other, depending on the position of the level.
The gauge or foot of king
It is an alloy steel instrument, which is used for measuring lengths, and is the most universal available. It consists of a “ruler” with a square at one end, on which another slide designed to indicate the measure on a scale.
It allows to appreciate lengths of 1/10, 1/20 and 1/50 millimetre using the nonius. By means of special pieces at the top and at the end, it is possible to measure internal dimensions and depths. It has two scales: the bottom millimetre and the top in inches.
We can differentiate different types of gauges, such as: universal gauge, exterior gauge, interior gauge, depth gauge, special gauges (for threads, etc.) gauge passes (measures hole diameters)
A goniometer
The goniometer or angle conveyor is an angle measuring instrument (sharp 90º>, flat 180º or obtuse >180º) in the form of a semicircle or graduated circle (from degree to degree), in 180º or 360º, used to measure or construct angles. This instrument allows to measure angles between two objects.
Micrometer
The Palmer micrometre or screw, is a measuring instrument whose operation is based on the micrometre screw that serves to measure the dimensions of an object with high precision, in the order of hundredths of millimetres (0.01 mm) and millimetres (0.001 mm) (micron). It is formed by two points that approach each other by means of a fine thread screw, which has engraved on its outline a scale. The scale includes a nonius and the maximum measurement lengths of the outdoor micrometre is usually 25 mm although they also exist at 30mm.
We can differentiate different types of micrometres such as: Universal micrometre or Palmer, outdoor micrometre, indoor micrometre, depth micrometre, special micrometres.
Dial gauge
A dial gauge is a measuring instrument that transforms the rectilinear movement of the contact points in circular motion of the hands.
It is used in workshops and industries for the verification of parts and that by its own means does not give direct reading, but it is useful to compare the differences that exist in the dimension of several parts that want to be verified. The ability to detect the difference in measurements is possible thanks to a mechanism of gears and levers, which are inserted into a metal box in a circular form.
Inside this box slides an axis, which has a spherical tip that makes contact with the surface. This axis, when moving, moves the clock needle, and makes possible the direct and easy reading of measurement differences.
The accuracy of a dial gauge can be one hundredths of a millimetre according to the scale at which it is graduated. They also occur in thousandths of an inch.
The mechanism consists of transforming the linear motion of the contact slider into circular motion that describes the clock needle. The dial gauge has to be incorporated into a check gauge or a support with a magnetic foot that allows it to be placed in the desired area of the machine. It is a very useful tool for the verification of different machining tasks, especially the eccentricity of rotation axes.
Alesometer
It is a measuring instrument used to measure or verify the concentricity or diameters of parts. Its operation and shape is very similar to that of the micrometre and is made up of probes housed in a steel housing at its end (which is what we measure), and a cylinder divided into millimetres next to a nonius, which can be normal, analog or digital.
Measuring machines
Measuring machines are a set of elements normally formed by a very heavy casting bed to give stability to the machine, a probe or a laser that take the measurements of the part held in a jaw or on the same support table thanks to flanges, this table is moved thanks to a gear system that allows moving to the coordinates X and Y if it is for 2 dimensions and X, And Z is for 3 dimensions, with these coordinates recorded on a monitor of the machine itself.
Other measuring instruments that are also considered as machines, because they take the measurement or verification work alone are the measuring or verification lasers.
IMEs in Asimer Group
Asimer Group has its own Metrology room where:
- Measurements are made of the most critical product measurements (valve and pump components) that are machined in the Production Department at Asimer.
- Keep the most important IMEs at the required temperature and humidity
- Annual calibrations of all IMEs available at Asimer.
In an environment where precision is key, measuring instruments are essential. From calipers to micrometers, each tool plays a crucial role in ensuring quality and accuracy in industrial production. By connecting this article with “Chip Removal Machining in the CNC Era,” we can explore how these instruments are used to further optimize machining processes, ensuring unparalleled precision in every manufactured component.
Among the most important IMEs for the control of parts and processes, we can highlight:
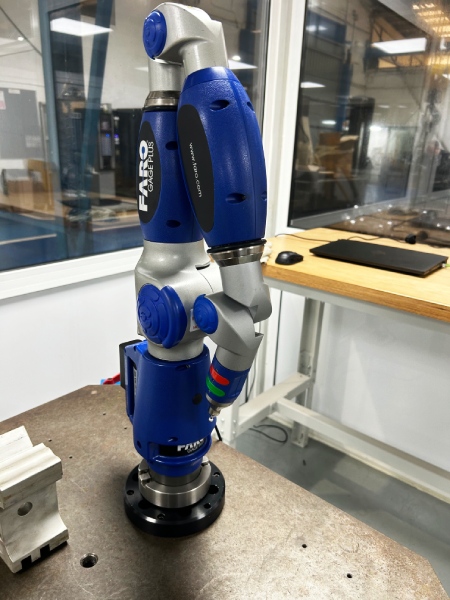
- Gauges or foot of king
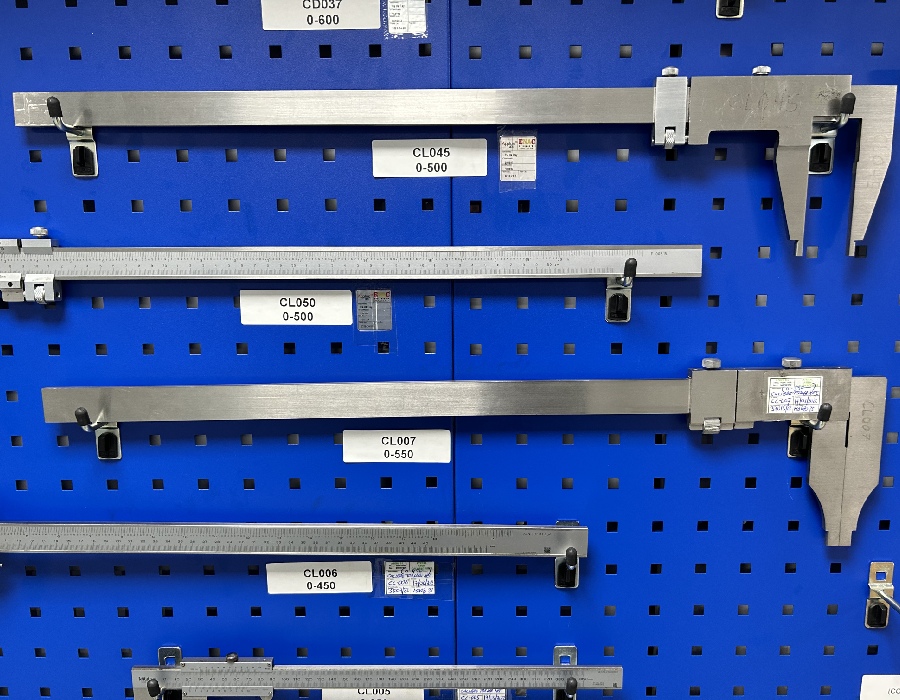
- External micrometres
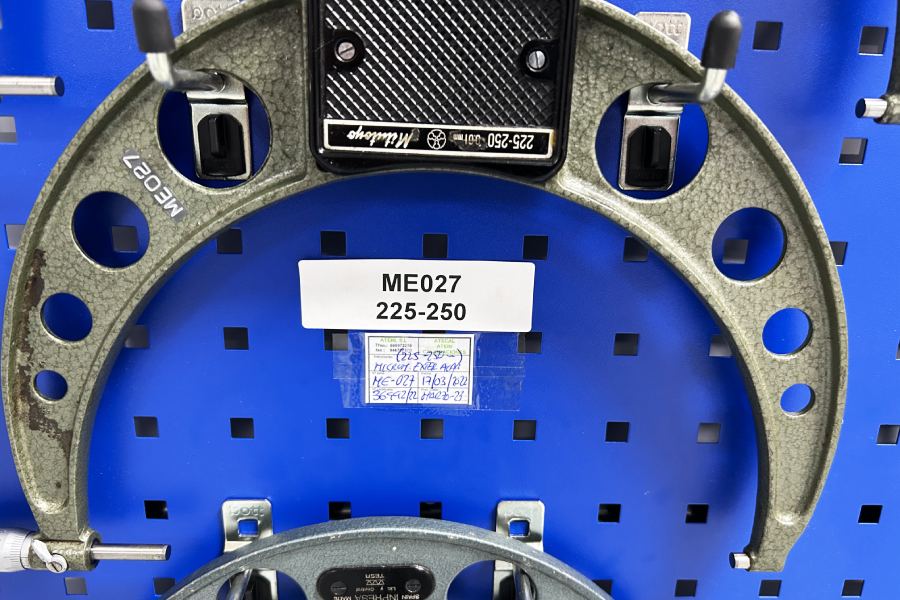
- Internal micrometres
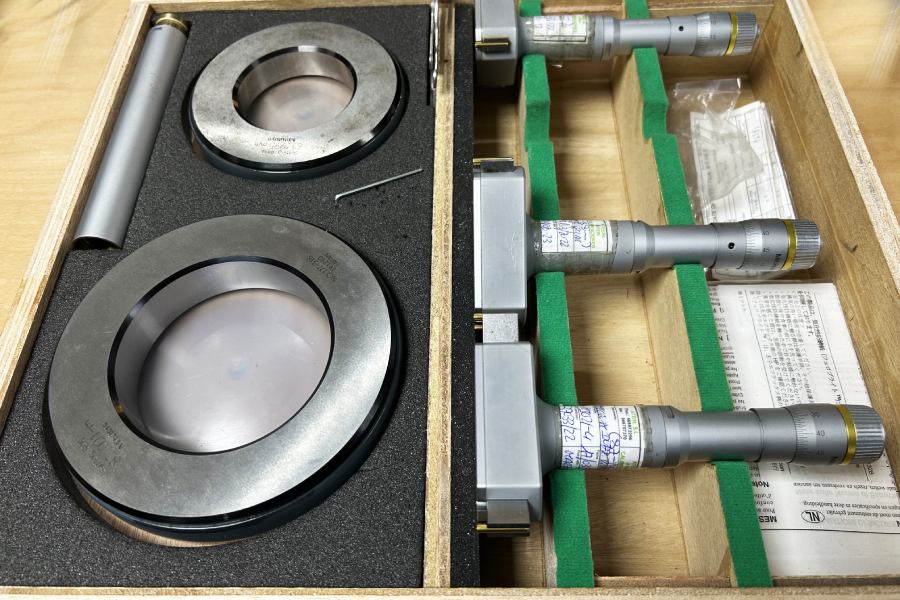
- Alexometer
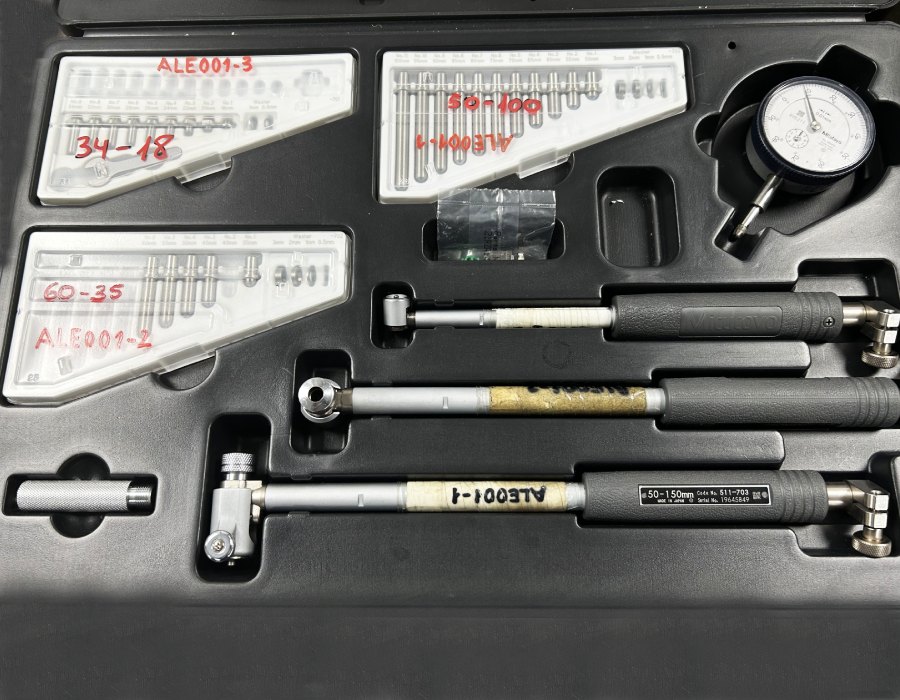
- Durometer
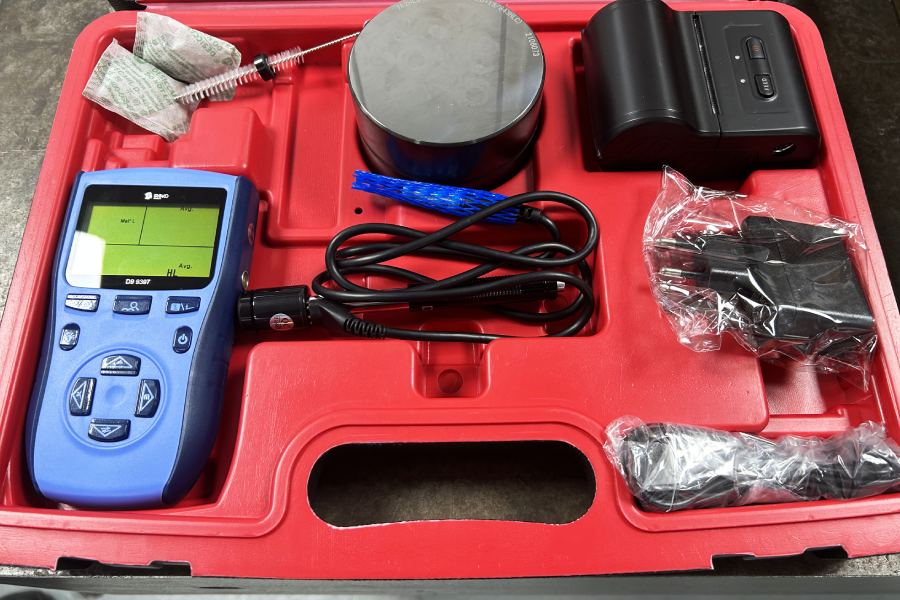
All IMEs in Asimer are kept in a perfect state of conservation in the Metrology room.
In addition, all IMEs are undergone annual External Calibration by Certified Company according to ENAC Standard, National Accreditation Entity. (The mission of ENAC is to evaluate organisations providing conformity assessment services, such as laboratories, certification and inspection bodies or verifiers, among others. These organisations play a critical role in the safety and well-being of people, the protection of the environment and the improvement of the quality and competitiveness of the products and services offered).
By accrediting ENAC, these evaluators demonstrate that they perform their work according to internationally accepted standards and that they have the required technical competence.
All IMEs are calibrated on the basis of the Calibration Procedures established for this purpose, and with their corresponding identification label, which reflects:
- Instrument and range of measurement
- Serial number
- Date calibration
- Certificate number
- Date next calibration
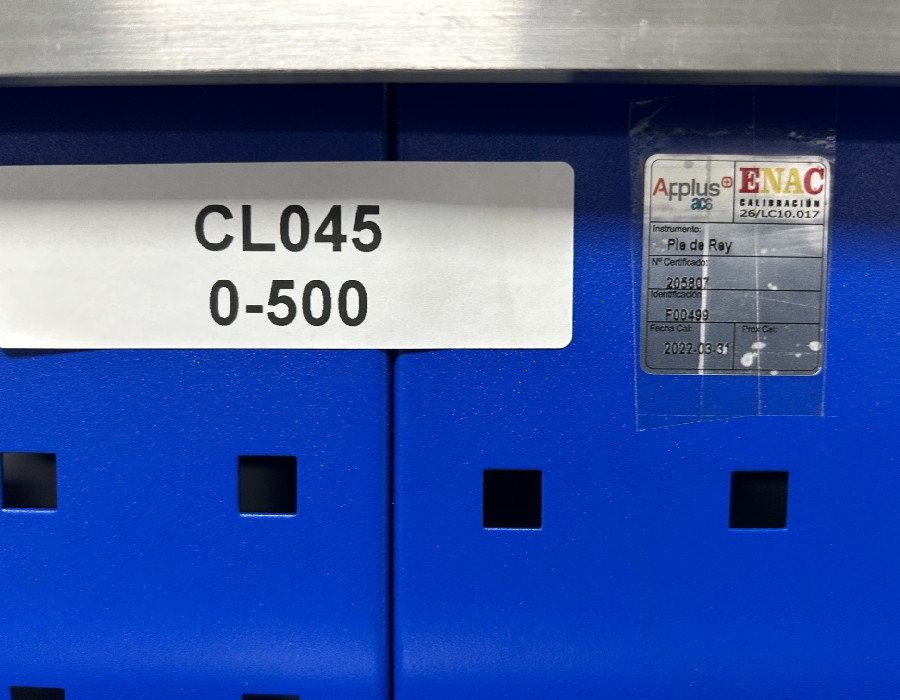