Centrifugal pumps are a cornerstone of modern industry, and their manufacturing requires a precise combination of materials and advanced techniques. Widely used in sectors such as water treatment, petrochemicals, mining, cryogenics, and food processing, these pumps are recognized for their ability to efficiently and reliably transport liquids.
However, behind their apparent simplicity lies a highly technical manufacturing process. Designing and constructing a centrifugal pump that meets the highest standards requires not only expertise in selecting suitable materials but also the application of advanced techniques like CNC machining, TIG welding, and Plasma Transferred Arc (PTA) welding. This article is tailored for industrial pump manufacturers looking to optimize their manufacturing processes and stay at the forefront of Industry 4.0.
Why Does Quality Matter in Centrifugal Pump Manufacturing?
The quality of a centrifugal pump directly impacts:
- Performance: Optimized designs minimize energy consumption and maximize flow rate, contributing to energy efficiency.
- Durability: High-strength materials extend the equipment’s lifespan.
- Safety: Poor manufacturing can compromise sealing integrity and even cause catastrophic failures, especially in critical applications.
Materials used in centrifugal pump manufacturing
Factors to consider when selecting materials
Industrial pump manufacturers face the challenge of finding materials that meet chemical, mechanical, and economic demands. Key factors include:
- Corrosion resistance: Essential for applications like water treatment and desalination.
- Ability to withstand high pressures and temperatures: Common in oil and gas and oil refining sectors.
- Cost-effectiveness: Particularly critical for large-scale projects.
Common materials
- Stainless Steel:
Ideal for handling corrosive liquids in applications such as cryogenics or pulp and paper mill. It is also compatible with techniques like TIG welding and automatic MIG welding. - Cast Iron:
Primarily used in parts of a centrifugal pump such as casings due to its wear resistance and cost-effectiveness. - Special Alloys:
Materials like titanium or nickel alloys are indispensable in extreme conditions, such as cryogenic applications or highly abrasive liquids.
Innovations in materials
Advanced coatings are enhancing durability and efficiency in machining applications for large-diameter valve fittings in the oil and gas industry.
Machining techniques in centrifugal pump manufacturing
Chip removal machining plays a critical role in producing essential components like impellers and shafts. This process is key to ensuring accuracy in CNC machining, especially for components subjected to tight tolerances.
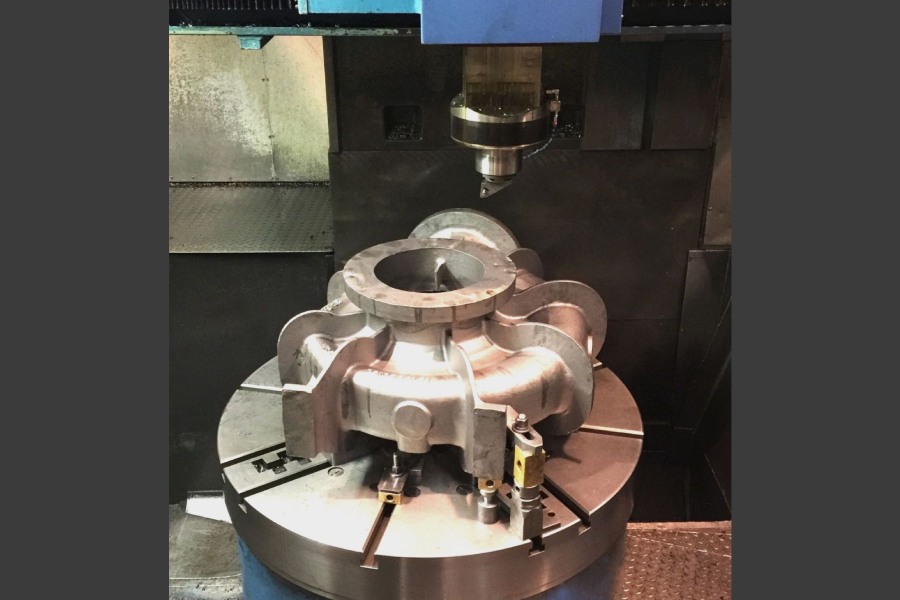
Key machining processes
- Turning and milling:
These processes contribute to the creation of complex surfaces in impellers and casings. Advanced CNC machining tools and equipment, such as the Trevisan machining center, are used for this purpose. - Drilling and alignment:
These ensure correct assembly of components to maintain sealing integrity.
Advanced technologies
- CNC machining:
Automation and CNC technology guarantee precision and efficiency. It is essential for machining large pumps and critical components in industries like oil and gas. - Electrical discharge machining (EDM):
Ideal for hard materials and complex shapes, such as measuring instruments used in high-precision processes.
Quality control in machining
The use of measurement arms and a fully equipped metrology room ensures that every component meets the required specifications.
Welding techniques in centrifugal pump manufacturing
Common welding methods
- TIG welding:
Excellent for joining thin materials like stainless steel in casings.The difference between TIG and MIG welding lies in their precision. While MIG welding is more efficient for high-volume projects, TIG welding is preferred for finer details. - Automatic MIG welding:
A versatile method used in large assemblies like pump casings and industrial valve types. - Plasma transferred arc (PTA) welding:
Used for coating components like impellers and shafts, especially in applications requiring wear resistance.
Welding innovations
The use of robotic MIG welding is gaining traction as it combines precision and speed, particularly in production lines where consistency is crucial.
Post-welding control and testing
Tests such as penetrant liquids inspection and other non-destructive tests (NDT) are essential to ensure there are no internal defects in welded joints.
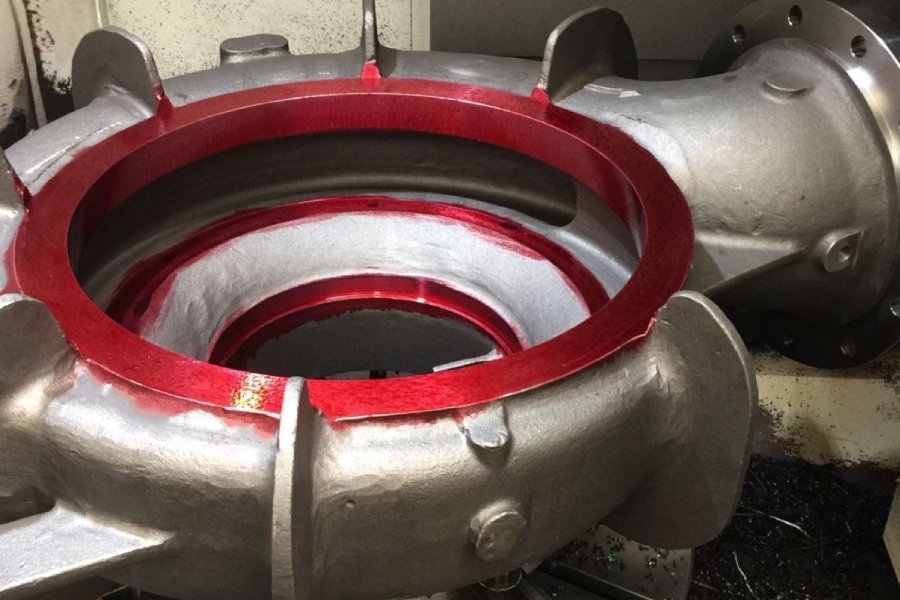
Engineering solutions in centrifugal pump manufacturing
Advanced engineering is crucial to ensuring centrifugal pumps meet the specific requirements of each industrial application, from cryogenics to petroleum refining.
Design optimization
CFD simulation helps to predict flow behavior in industrial centrifugal pump applications, optimizing energy efficiency.
Integration of smart technologies
In the context of Industry 4.0, sensors are being integrated to monitor variables like pressure, temperature, and flow rate in real-time. This enables predictive maintenance, reducing operational costs and extending pump life.
Custom design
Every client has unique needs. At Asimer Group, we collaborate with manufacturers to develop customized solutions, including advanced materials and modular configurations that simplify maintenance.
Sustainability in engineering
Designs prioritize material waste reduction and energy optimization, contributing to industrial sustainability goals.
Success stories and practical applications
At Asimer Group, we have led standout projects that demonstrate our ability to tackle technical challenges and deliver high-performance solutions:
- Pumps for desalination plants:
We have contributed to projects involving pumps for highly corrosive environments using stainless steel with advanced coatings. These pumps have shown exceptional performance in extreme salinity conditions. - Axial flow casings:
We collaborate with European manufacturers to produce axial flow casings through high-precision CNC machining. This ensures optimal delivery times and perfect fitment in complex systems. - Project with centrifugal pump casings in CF3M:
Recently, we completed a project for an Italian client in the Oil & Gas sector, which included:
- Premachining.
- Dye penetrant testing (PT) on critical sealing areas.
- Final machining.
- Non-destructive tests (NDT) such as PMI, hardness testing, and visual inspection.
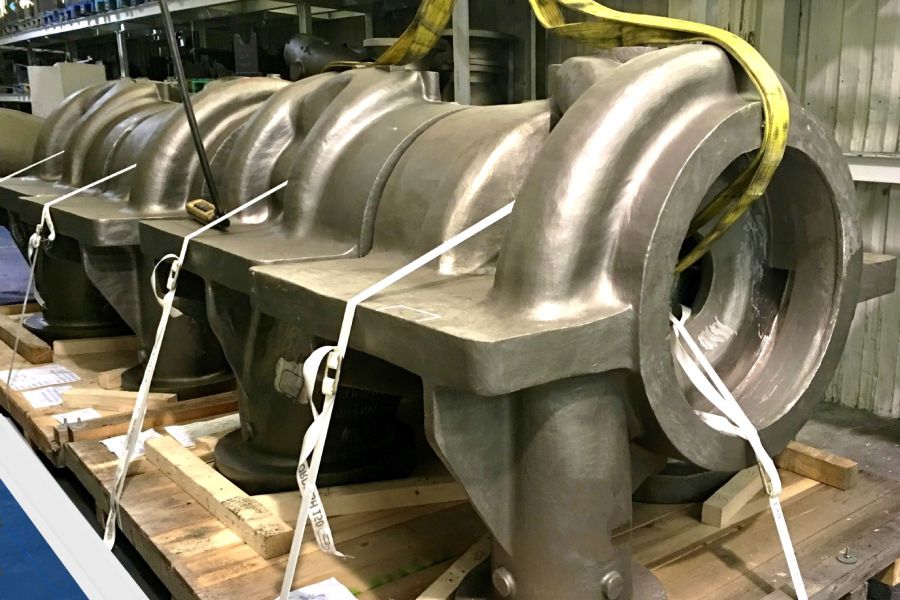
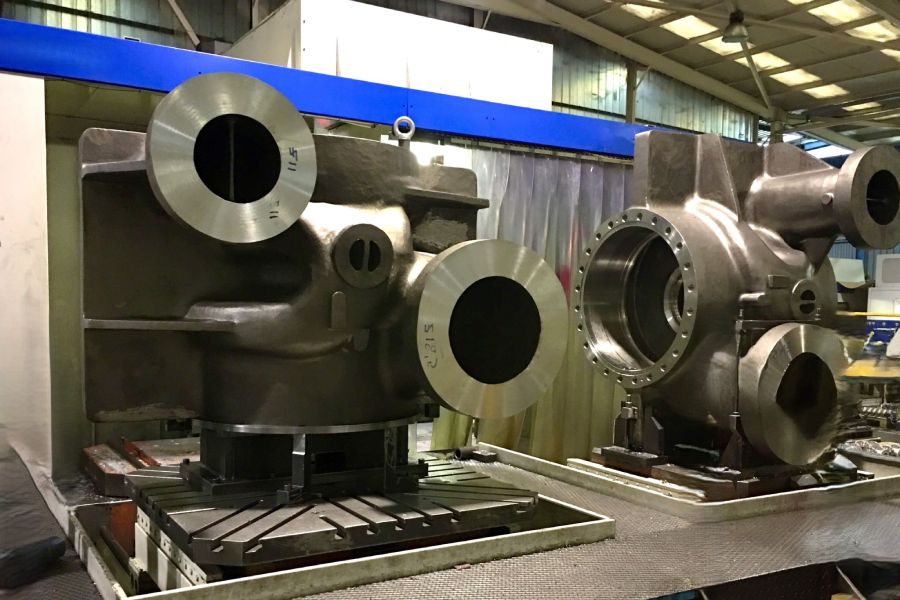
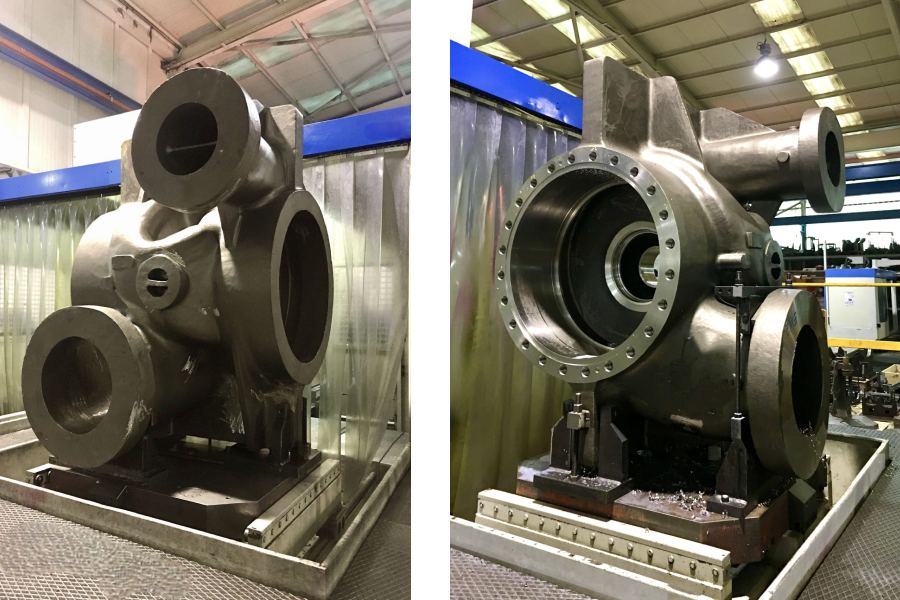
Conclusion
Centrifugal pump manufacturing is a discipline combining material science, advanced manufacturing techniques, and engineering solutions. At Asimer Group, we specialize in providing tailored solutions to meet the specific needs of our clients.
With a focus on energy efficiency and sustainability, our commitment is to deliver value through innovations in design, machining, and welding. If you are looking to optimize your processes or need specialized solutions, our team is ready to help take your projects to the next level.