In the industrial sector, the need to reduce the carbon footprint in pumps and valves is becoming increasingly urgent. This commitment not only addresses environmental demands but also drives competitiveness and operational sustainability. At Asimer Group, we specialize in solutions that integrate advanced technology and innovation to minimize the environmental impact of our machining and contributions to industrial valves and pump bodies. This article explores how our initiatives in CNC machining, welding, and sustainable design help transform the industry.
The importance of sustainability in manufacturing
Sustainability has become a cornerstone of the manufacturing industry, particularly in sectors like industrial pumps and valves. Adopting sustainable practices not only minimizes environmental impact but also enhances competitiveness and operational efficiency.
On one hand, sustainability fosters technological innovation, driving the development of more efficient and less polluting processes, supported by advances such as Industry 4.0 and the integration of digital tools in manufacturing. On the other hand, compliance with increasingly strict environmental regulations translates into economic benefits, such as reduced operating costs and access to markets with high sustainability standards.
Moreover, customers and business partners increasingly value companies’ environmental commitment, strengthening corporate reputation and opening new business opportunities. For Asimer Group, sustainability is not just a trend but a key strategy to lead change in the industry.
What is the carbon footprint in the manufacturing of pumps and valves?
The carbon footprint measures the amount of greenhouse gases (GHG) emitted directly or indirectly during industrial processes. In the manufacturing of pumps and valves, these emissions primarily come from:
- Machining and welding processes: Energy consumption in machinery and emissions associated with the use of gases and materials, such as in TIG welding and automatic MIG welding.
- Transport and logistics: Movement of materials and finished products.
- Materials used: Production and processing of raw materials.
Reducing this footprint not only helps protect the environment but also improves operational efficiency and enables companies to align with international regulations. At Asimer Group, we integrate advanced methodologies to address each of these factors, promoting sustainable practices that go beyond manufacturing.
We also work closely with our clients to understand their specific challenges and tailor our solutions to their needs, creating long-term strategies that generate positive impacts for both their operations and the environment.
Factors contributing to the carbon footprint in pumps and valves
The environmental impact in the industrial pumps and valves sector is influenced by various factors, from manufacturing to the supply chain. Below are some critical aspects:
CNC machining: key to reducing the carbon footprint
CNC machining plays a crucial role in reducing the carbon footprint in industrial manufacturing, especially in the pumps and valves sector. This process, driven by advances in CNC technology, allows precise control over each operation, minimizing errors and reducing material waste. At Asimer Group, we employ advanced technology that optimizes every stage of machining to ensure more efficient resource usage.
One of the most significant benefits of CNC machining is its ability to operate with high energy efficiency. Modern machines are designed to consume less energy without compromising precision. Additionally, the integration of heat and energy recovery systems in our facilities significantly reduces the environmental impact.
The use of digital simulations is another key aspect. Before any operation, our teams use specialized software to plan every step of the process. This not only reduces operation time but also ensures that only the necessary amount of material is used, thereby reducing waste and emissions. In this context, tools such as measuring instruments, the articulated measuring arm, and computer-aided design are indispensable for achieving accuracy in CNC machining.
Additionally, we work with a wide range of CNC machining tools that optimize processes such as chip removal machining, essential for complex components like valves and pumps. These technologies not only ensure precise results but also reduce associated waste.
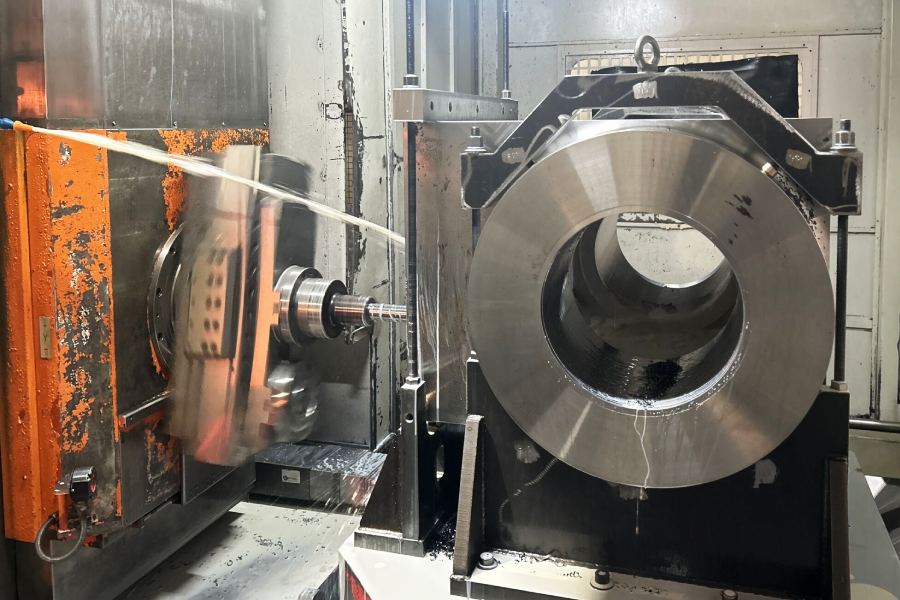
Sustainable welding
Our TIG and automatic MIG welding processes are designed to maximize efficiency, reduce material consumption, and minimize direct gas emissions. The integration of robotic automatic welding ensures consistent results and shorter operation times, further contributing to a lower carbon footprint.
We also promote the use of less polluting gases, such as specialized blends that generate fewer emissions during the process. Additionally, we develop specific protocols to reduce waste associated with consumables by implementing internal recycling systems that maximize material reuse and minimize waste.
The development of hybrid technologies, such as PTA welding, allows us to tackle highly complex projects, including the maintenance of valves and components used in sectors such as petrochemicals, oil and gas, water treatment, and cryogenics.
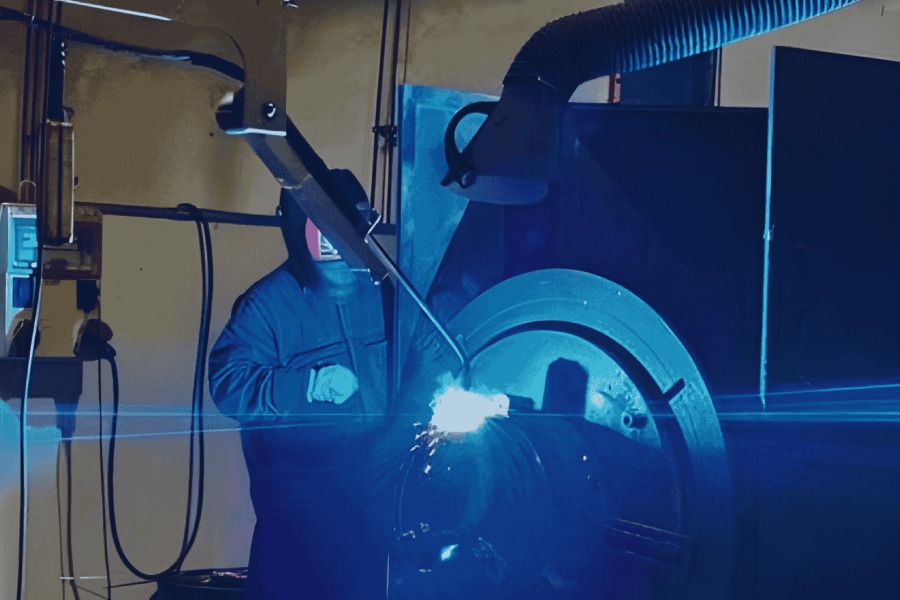
Sustainable design and engineering
Our engineering team develops custom solutions to optimize pump and valve projects, reducing material use and improving product efficiency. We analyze different industrial valve types to ensure each meets the specific requirements of its application, whether for high pressure, controlled flow, or critical systems.
Using advanced simulations, we test the efficiency of designs before production. By integrating recyclable and lightweight materials, we create components that meet high technical standards while reducing environmental impact.
Technologies like the Trevisan machining center, advanced tools like the articulated arm, and our metrology room ensure unmatched precision, contributing to more sustainable designs. Improved sealing in valves and pumps is another critical aspect for reducing energy losses and enhancing performance in industrial systems.
We also explore the use of non-destructive testing methods, such as liquids penetrant, to ensure the quality and durability of components, particularly for demanding applications like desalination and the naval sector.
Sustainable strategies at Asimer Group
At Asimer Group, we actively work to reduce the carbon footprint of our processes and those of our clients through innovative strategies:
Efficient CNC machining
- Advanced technology: Latest-generation CNC machines ensure maximum energy efficiency by working faster and more precisely.
- Material optimization: Simulation software minimizes raw material waste.
- Real-time monitoring: Systems identify opportunities to improve efficiency during machining.
- Continuous training: Operators are trained to maximize machine efficiency.
Sustainable welding
- Automation: Automatic MIG welding optimizes time and resources, delivering consistent, high-quality results.
- Eco-friendly gases: Innovative gas use reduces harmful emissions.
- Material reuse: Recycling consumables minimizes waste and boosts sustainability.
- Hybrid processes: Combined welding techniques enhance efficiency and adapt to specific client needs.
Engineering focused on sustainability
- Lifecycle analysis: Evaluating the environmental impact of products from manufacturing to end-of-life.
- Sustainable materials: Partnering with suppliers of recyclable and low-carbon options.
- Optimized designs: Components maximize operational efficiency and minimize environmental impact.
- Digital tools: 3D modeling and simulations ensure sustainable designs before production.
3D simulation to analyze and optimize designs, ensuring maximum sustainability.
Benefits for our customers
Asimer Group’s sustainable solutions offer clear advantages to manufacturers of pumps and valves:
- Regulatory compliance: Helping clients meet strict environmental regulations, avoiding penalties, and enhancing their reputation.
- Operational cost savings: Process optimization reduces energy and material consumption.
- Enhanced reputation: End customers increasingly value companies adopting sustainable practices.
- Innovation and competitiveness: Advanced, sustainable technologies position clients as industry leaders.
- Improved efficiency: Rational resource use translates to more agile and profitable operations.
Innovation and sustainability in action
Innovation is key to reducing the carbon footprint in the industry. At Asimer Group, we focus on solutions that integrate advanced technology and sustainability.
Collaboration with clients and suppliers is another cornerstone of our strategy. By sharing knowledge and setting joint goals, we achieve significant improvements that benefit the entire value chain. These initiatives not only contribute to a cleaner planet but also generate tangible savings and reinforce our position as industry leaders.
Asimer Group: Your partner in sustainability
At Asimer Group, we don’t just deliver high-quality industrial projects; we also help our clients achieve their sustainability goals. Our expertise in CNC machining, welding, and engineering solutions allows us to offer processes that reduce the carbon footprint and promote a greener future.
If you’re looking to transform your industrial processes and make them more sustainable, contact us today. Together, we can lead the change towards a responsible and environmentally committed industry.