How optimize costs in the machining of pumps and valves, is a key factor in ensuring profitability and competitiveness in a demanding market. In this article, we explore practical strategies you can implement to reduce expenses without compromising quality, helping you stand out in the industry.
Why is cost optimization in the machining of pumps and valves important?
Cost control not only impacts financial results but also the ability to meet customer expectations. Inefficient production can lead to:
- Increased operational expenses.
- Delays in delivery times.
- Lower-quality products resulting in returns and complaints.
At Asimer Group, we understand that every industrial project has unique needs. That’s why we work closely with our clients to identify areas for process improvement and provide tailored solutions that maximize efficiency and minimize costs.
Strategies for reducing costs in the machining of pumps and valves
Incorporating engineering solutions
At Asimer Group, we develop customized engineering solutions to optimize machining processes and reduce costs. These solutions focus on key sectors such as water treatment, where component optimization enhances the efficiency of industrial pumps, and valve manufacturing, ensuring high precision and durability.
Adopting advanced CNC technology
Using CNC (Computer Numerical Control) machinery is one of the most effective strategies for cost optimization in machining. Its benefits include:
- Extreme Precision: Reduces errors and material waste.
- Automation: Faster and more consistent processes.
- Flexibility: Capability to handle complex designs and customizations.
At Asimer Group, we use the latest CNC technology, including Trevisan machining centers, capable of machining valve and centrifugal pump components with high precision. This approach guarantees high-quality products optimized to meet the demands of industrial applications, such as machined components for centrifugal pumps used in sectors like water treatment and petrochemicals.
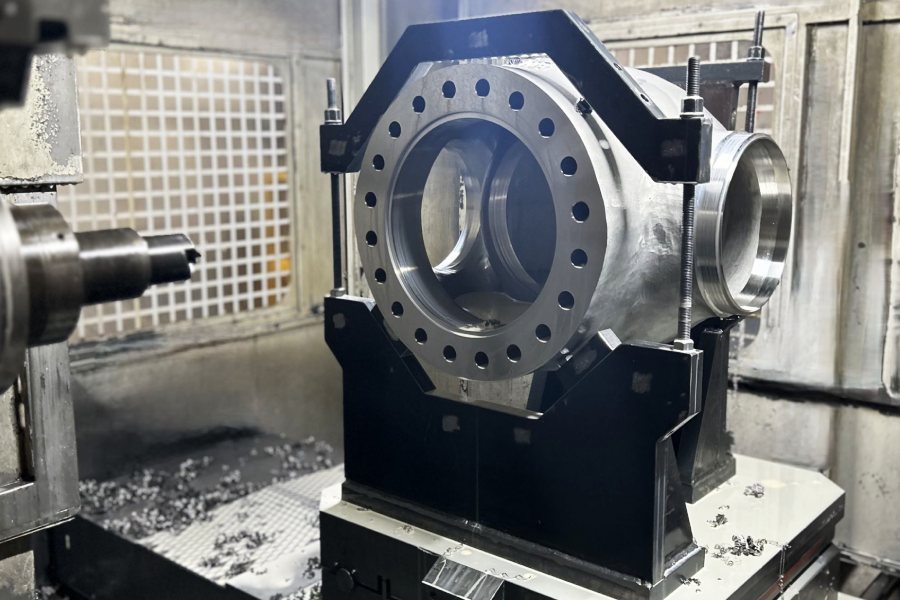
Efficient component design
Efficient component design can make a significant difference in the final production cost. Some approaches include:
- Simplifying Designs: Reducing unnecessary elements that complicate machining.
- Selecting Suitable Materials: Opting for options that are easy to work with and meet technical specifications.
- Collaborating Early: Involving machining experts from the initial design stage to foresee issues and optimize processes.
At Asimer Group, we offer technical design consulting services to ensure every component is optimized for manufacturing. This not only saves time and money but also improves the performance of the final product.
Preventive maintenance of machinery
Preventive maintenance ensures the continuity of production processes and reduces costs associated with unexpected downtimes. Essential practices include:
- Regular Inspections: Identifying potential machine failures before they impact production.
- Replacing Worn Parts: Preventing major breakdowns and extending equipment life.
- Proper Lubrication and Cleaning: Maintaining optimal performance and minimizing wear.
At Asimer Group, we perform rigorous maintenance on our machines to ensure efficient and precise operations. Additionally, we apply non-destructive testing (NDT) methods, such as liquid penetrant testing, directly on pumps and valves to detect surface defects without damaging the components. This ensures reliable parts that meet the highest standards.
Our experience and certifications in non-destructive testing reflect our commitment to industrial quality. These practices not only guarantee reliable, high-performance products but also enhance our ability to provide optimized solutions for key industrial sectors such as petrochemicals, desalination, cryogenics, and naval applications. Moreover, we incorporate Industry 4.0 principles into our operations, leveraging advanced technologies to improve precision, efficiency, and traceability in all processes. This holistic approach translates into direct benefits for our clients, such as increased component durability, reduced operational failures, and optimized production processes.
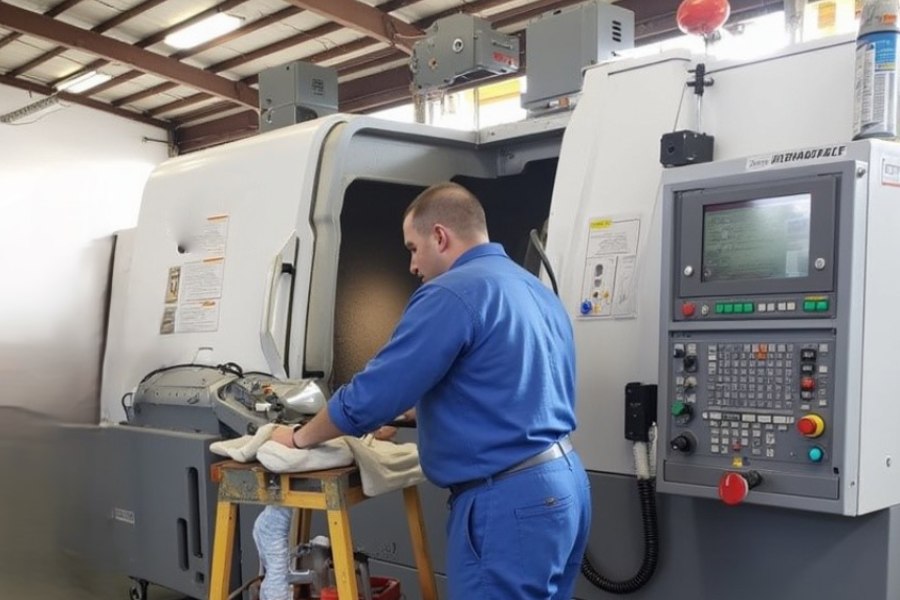
Certifications: A pillar of cost optimization
Having recognized quality certifications, such as ISO 9001, not only ensures efficient processes and reliable results but also reduces costs associated with errors and optimizes productivity in sectors like naval and oil refining. At Asimer Group, we are committed to the highest international standards, including ISO 9001 and ISO 3834-2, which validate our ability to provide machining and welding solutions with guaranteed precision and quality. These certifications strengthen our credibility and enable cost optimization by implementing standardized and rigorous processes that minimize errors and maximize efficiency.
Our expertise includes key projects where we apply advanced techniques to ensure reliable and durable components. For instance, we have developed specific solutions to prevent leaks in critical parts, such as butterfly valves, ensuring optimal performance even in extreme conditions.
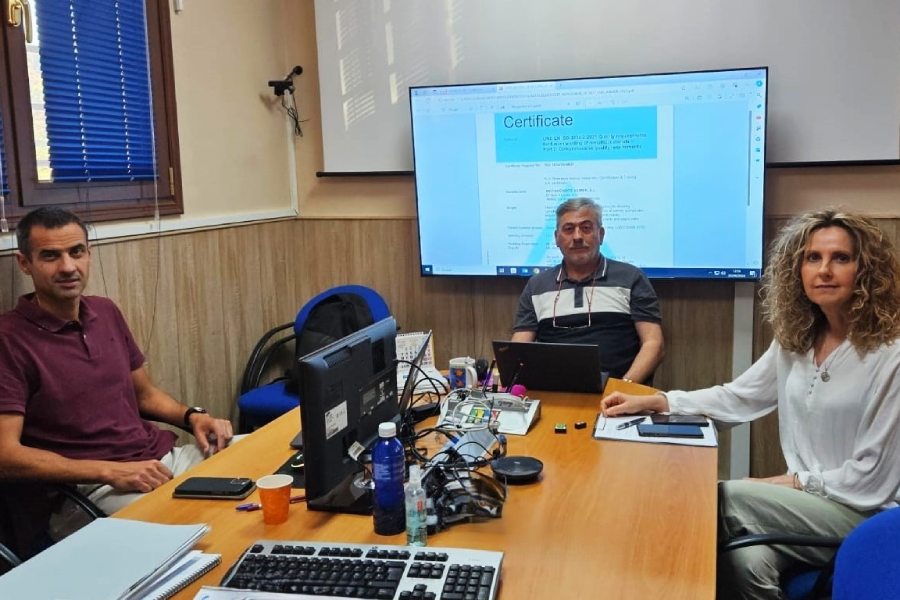
Benefits of cost optimization in machining of pumps and valves
At Asimer Group, we implement advanced strategies that combine technology, sustainability, and innovation to ensure efficient and responsible processes. For example, the use of CNC machining tools allows us to reduce production times and operational costs while ensuring precise and durable components.
Additionally, we promote sustainable practices that reduce the carbon footprint in the manufacturing of industrial pumps and valves, contributing to a lower environmental impact. This approach ensures competitiveness in key sectors such as water treatment and petroleum refining.
Our solutions are designed to meet the demands of complex industries, such as petrochemicals, cryogenics, and desalination. In the oil and gas sector, for instance, we work with high-resistance fittings that minimize operational failures under extreme conditions. Similarly, in cryogenic applications, accuracy machining and optimized component design ensure exceptional performance.
To achieve this level of quality, we use advanced measurement instruments, such as measuring arms and inspection tools in our metrology room. These technologies ensure every component meets the most stringent requirements.
Key benefits of cost optimization
- Cost Reduction: Achieved through efficient processes driven by CNC technology and preventive maintenance.
- Higher Quality: Ensuring precise and durable components, even in projects involving large-scale valve machining.
- Enhanced Competitiveness: Delivering sustainable products that meet the standards of industries like petrochemicals, cryogenics, and desalination.
We stand out for our ability to integrate advanced technologies, such as TIG and MIG automated welding, into complex projects. These strategies not only optimize production times and minimize errors but also ensure sustainable solutions that benefit both the environment and our clients’ profitability.
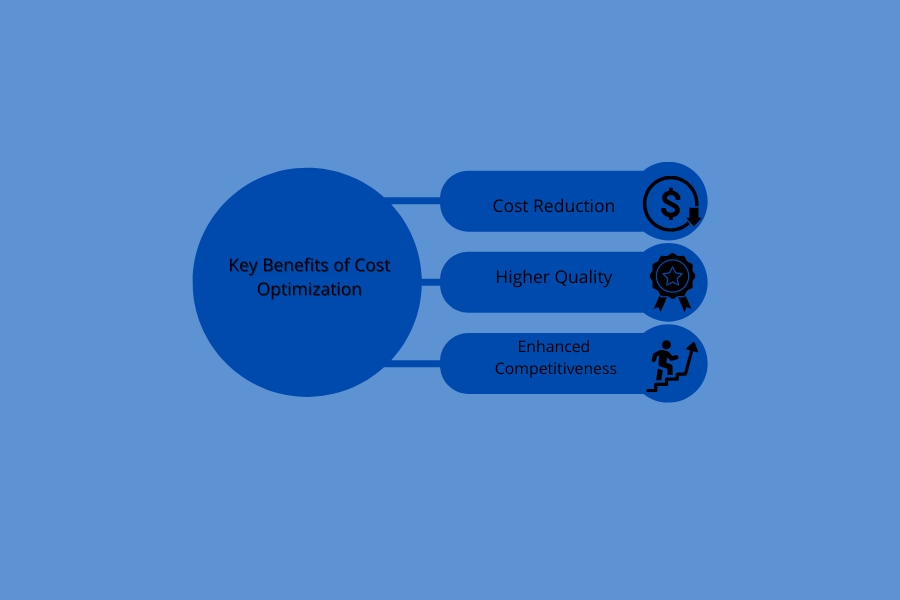
Case studies in optimization cost in machining of pumps and valves
At Asimer Group, we guarantee energy efficiency and sealing reliability in every machined component thanks to advanced CNC technology and optimized design processes. This allows us to provide durable, high-performance solutions for demanding sectors like petrochemicals and desalination.
In specialized applications such as cryogenic valves and pumps, precision and resistance to extreme conditions are essential. Thanks to our expertise in high-precision machining, we have successfully overcome the most demanding challenges, optimizing costs while ensuring the reliability of components.
Examples of Successful Cases
- Cost Reduction in Centrifugal Pumps: A client in the centrifugal pump sector reduced production costs by 20% after implementing our advanced CNC technology. Additionally, by redesigning key components, we optimized manufacturing and improved operational efficiency. Predictive maintenance further minimized interruptions, maximizing productivity.
- Efficient Production of Industrial Valves: For a client specializing in industrial valves with extremely precise tolerance requirements, we utilized 3D scanning technology and optimized the component design. This resulted in a 30% reduction in manufacturing time without compromising quality, showcasing our ability to meet the most stringent specifications.
Boost your competitiveness with cost optimization
At Asimer Group, we are experts in combining advanced technology, technical expertise, and sustainability to optimize every stage of your industrial processes. We work with demanding sectors such as petrochemicals, cryogenics, and desalination to deliver high-performance solutions that comply with the most rigorous standards.
Our services include:
- MIG, Automated MIG, TIG, and PTA Welding: Offering a wide range of welding processes, from the precision and versatility of TIG welding to the advanced automation of MIG welding, ideal for projects requiring high efficiency and uniformity. Additionally, PTA welding specializes in applications where wear resistance and durability are critical.
- CNC Machining by Chip Removal: Ideal for complex parts, using advanced tools that optimize resources and ensure minimal tolerances.
- Efficient Redesign and Production of Components, Tools, and Fixtures: Tailored solutions that maximize efficiency and minimize costs in sectors such as water treatment and petroleum refining.
Additionally, our team of technicians supports you from the initial design to the final delivery, ensuring that every component meets the highest quality and sustainability standards. By implementing advanced strategies, such as non-destructive testing and CNC technologies, we help our clients reduce production costs by 20-30%, as demonstrated by our success stories in centrifugal pumps and industrial valves.
Contact us today! Discover how our CNC machining and welding solutions can transform your projects, enhance the quality of your components, and significantly reduce your operational costs.
Frequently asked questions
What factors influence the machining costs of pumps and valves?
The main factors include:
- Design Complexity: More complex designs require additional time and specialized tools.
- Material Type: Hard-to-machine materials can increase costs.
- Technology Used: Advanced machinery like CNC reduces errors and production time.
- Volume and Deadlines: Large volumes or tight deadlines may require more intensive processes.
What advantages does CNC technology offer in cost reduction?
CNC technology provides multiple benefits:
- Extreme Precision: Minimizes errors and material waste.
- Process Automation: Speeds up production and improves consistency.
- Flexibility: Enables work on complex designs and specific customizations, optimizing resources.
Which sectors benefit from these strategies?
We work with clients in demanding industries requiring high-precision, durable components, such as:
- Petrochemicals: Optimizing valves and fittings for corrosive environments.
- Naval: Machining and welding components exposed to extreme conditions.
- Desalination: Designing and manufacturing parts resistant to saltwater corrosion.
- Cryogenics: Producing pumps and valves with strict tolerances for low-temperature applications.
What impact does sustainability have on machining?
Sustainability not only reduces environmental impact by conserving resources but also improves energy efficiency, resulting in lower operating costs. At Asimer Group, we promote sustainable practices such as efficient material usage, reducing the carbon footprint of industrial pumps and valves, and integrating advanced technologies to maximize process efficiency.