High-accuracy machining for the Oil and Gas sector is a key process to ensure the reliability and efficiency of the components used in this industry. The demand for minimal tolerances, corrosion-resistant materials, and compliance with international regulations makes CNC machining essential in the manufacturing of parts for pumps, valves, and other critical equipment. Asimer Group, with over 30 years of experience in precision machining, offers engineering solutions to meet the needs of the Oil and Gas sector, ensuring quality and compliance with the most stringent standards. In this article, we will explore the importance of machining in this sector, the materials used, technological innovations, and how to optimize processes to reduce costs without compromising quality.
The importance of high-accuracy machining in oil and gas
Components used in the Oil and Gas industry must operate in high-demand environments, enduring pressures of up to 15,000 psi, extreme temperatures as low as -196 °C, and exposure to highly corrosive fluids such as hydrocarbons and chemical agents. These conditions require advanced machining processes that guarantee maximum precision and reliability for each part.
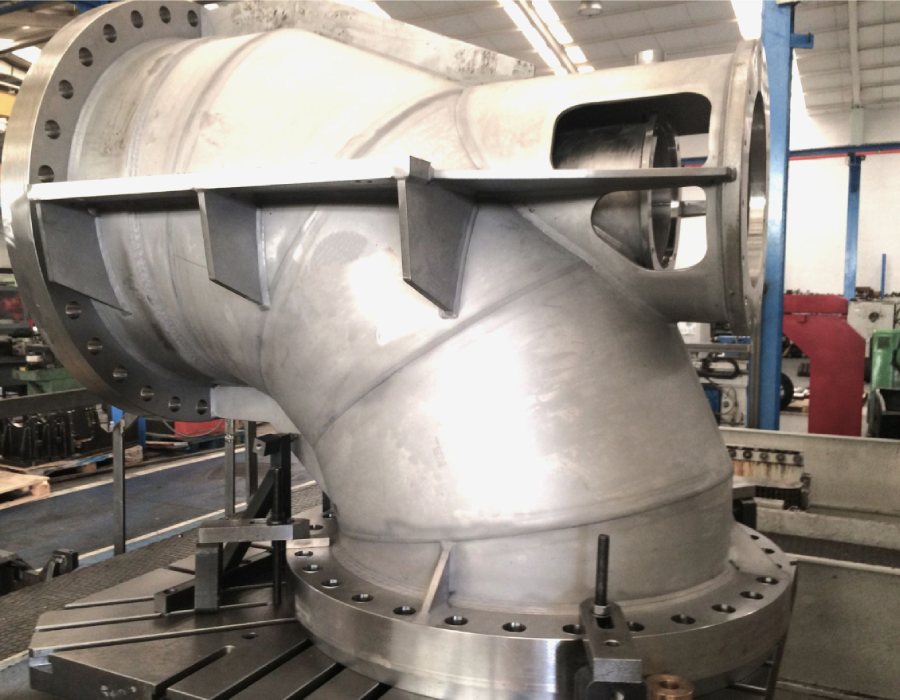
Some of the most critical elements that require high-precision machining include:
- Industrial pumps, where precision machining optimizes hydraulic efficiency, reduces impeller wear, and improves performance in fluid transport.
- Flow control valves, which require minimal tolerances and high-precision surface finishes to prevent leaks and ensure safe operation in high-pressure systems.
- Cryogenic valves, designed to handle liquefied gases at low temperatures, require precision machining to prevent losses and ensure tight sealing.
- Fittings in the Oil and Gas industry, which must meet exact geometric specifications to guarantee the structural integrity of pipelines.
- Diaphragm valves, used in applications where precise flow control is crucial for system safety and efficiency.
- Butterfly valves, widely employed in regulating the flow of liquids and gases, require precise machining to ensure proper operation in the petroleum industry.
To meet high safety and quality standards, CNC technology and CNC machining implementation are essential for manufacturing these components. Asimer Group, with its expertise in precision machining, collaborates with leading industry manufacturers, offering solutions tailored to the specific market needs. With its ability to produce parts with tight tolerances and high-quality finishes, Asimer Group ensures components that meet the strict demands of the Oil and Gas industry, optimizing production processes and reducing operational failures.
Material selection and treatments in high-accuracy machining for oil and gas
To ensure the quality of machined parts, the use of a metrology room equipped with advanced dimensional inspection tools is crucial. The combination of measuring arms and high-precision measuring instruments verifies that the parts meet the tolerances required by the Oil and Gas industry.
The materials used in precision machining must withstand highly aggressive environments with exposure to chemical agents, extreme temperatures, and high pressures without compromising their structural integrity. Some of the most commonly used materials include:
- High-alloy stainless steel (such as AISI 316L and Duplex), widely used in components requiring corrosion resistance in marine and chemical processing environments. These materials are essential in control valves and industrial fittings.
- Titanium, a high-strength, low-density material used in underwater and cryogenic applications. Its resistance to fatigue and corrosion in saline water environments makes it ideal for submersible pump components and high-pressure pipelines.
- Nickel-based superalloys (such as Inconel), designed to operate under extreme heat and mechanical loads. Their use is crucial in check valves and combustion systems in refineries and natural gas plants.
- Surface treatments, such as tungsten carbide and chromium nitride coatings, used to improve wear resistance in components subjected to extreme friction, such as high-pressure valves and centrifugal pump impellers.
- Heat treatments to enhance cryogenic resistance in industrial pumps and valves, such as thermal aging in superalloys and cryogenic treatment in stainless steels. These techniques increase material toughness, preventing cracks in valves used in cryogenic Oil and Gas systems.
- Anti-corrosion treatments for centrifugal pump components, including high-performance polymer coatings and anodizing to improve durability in aggressive environments.
In addition to material selection, these components require advanced manufacturing techniques, such as chip removal machining and specialized cutting tools with ceramic coatings to prevent premature wear in superalloys like Inconel. Asimer Group has state-of-the-art machinery and a highly specialized team to ensure maximum precision in machining critical components for the Oil and Gas industry, guaranteeing quality and reliability in every manufactured piece.
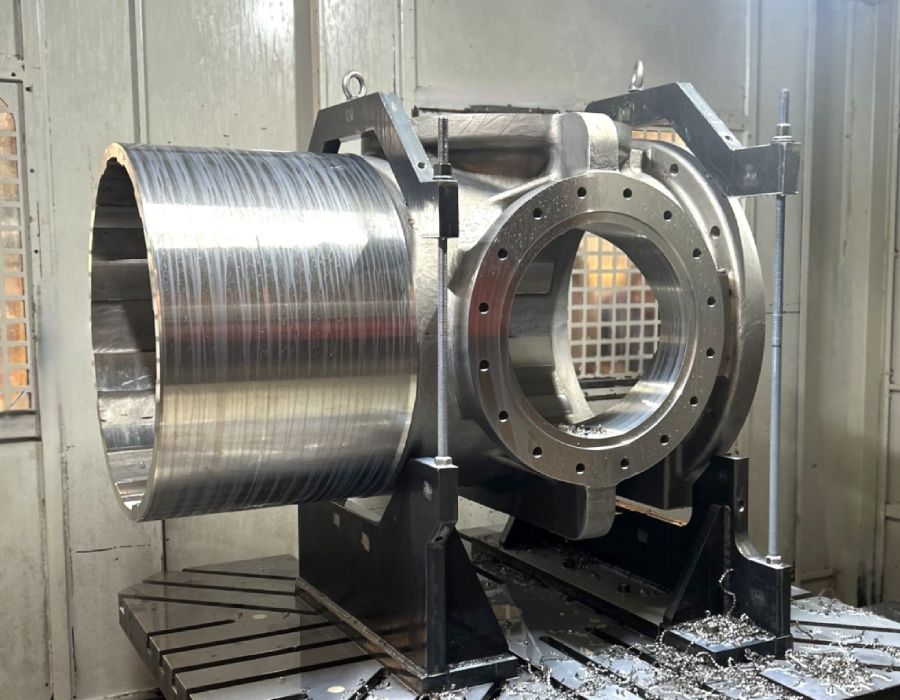
Technological innovations in machining for oil and gas
One of the key advancements in the industry is the manufacturing of axial flow check valves in the oil sector, widely used in water injection systems in oil wells, ensuring adequate pressure and preventing fluid backflow. Thanks to the latest developments in CNC technology, it is possible to produce these components with millimeter tolerances and ensure their performance in extreme conditions.
The use of advanced technologies has also improved accuracy in CNC machining, allowing for tolerances of up to ±0.002 mm, which is crucial for components subjected to high pressure and temperature in the Oil and Gas industry. This enables the manufacturing of extremely tight-tolerance parts, essential for ensuring optimal performance in demanding environments.
Advancements in machining technologies have revolutionized the manufacturing of components for the Oil and Gas sector. The implementation of Industry 4.0, the use of advanced CNC technology, and automation have enhanced precision and reduced production times. Some key innovations include:
- Trevisan machining centers: Advanced systems that allow machining large parts with high precision.
- Next-generation CNC machining tools, designed to work with high-strength materials.
- Applications of CNC machining in the Oil and Gas sector, optimizing manufacturing processes for industrial valves and pumps.
- Industry 4.0 in machining, with the use of sensors and real-time monitoring systems to improve efficiency.
- Machining automation, reducing human errors and increasing process repeatability.
The future of machining in this sector lies in digital optimization and smart manufacturing, technologies that enable real-time simulation of machining processes to predict failures and optimize production. Asimer Group positions itself as a leader in implementing these technologies to improve efficiency and quality in processes, ensuring more efficient, safe, and sustainable operations.
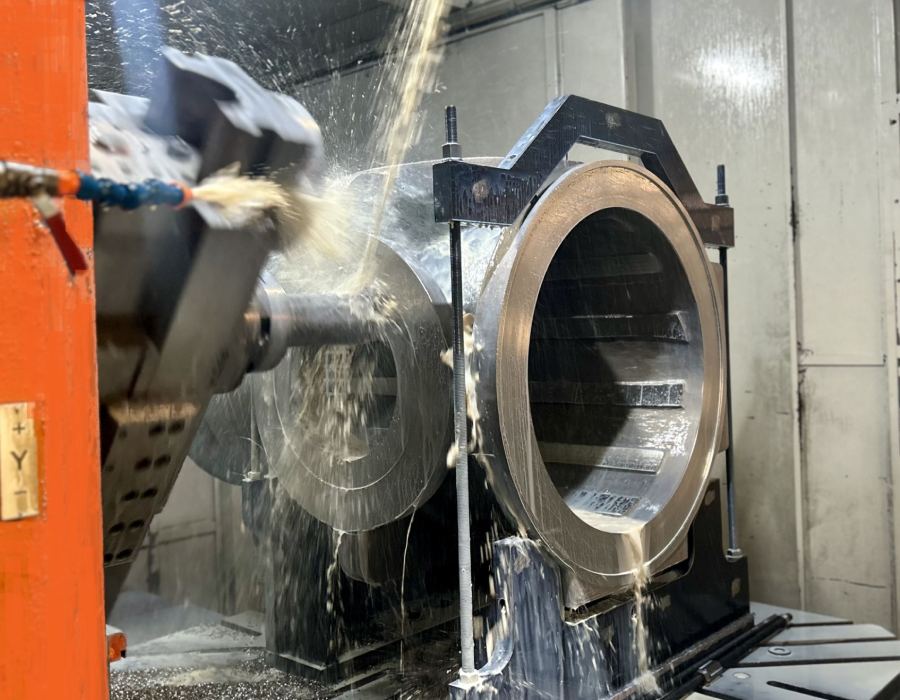
Evaluation and maintenance in machining for oil and gas
In addition to the manufacturing of valves and pumps, precision machining also plays a fundamental role in the maintenance of critical equipment. Cryogenic pump applications require rigorous inspection processes to ensure proper operation in low-temperature environments, such as in the transportation of liquefied natural gas (LNG) or air separation plants, where machining precision is key to operational efficiency. Energy efficiency in these devices is a determining factor for operational optimization and cost reduction in refineries and processing plants.
Advanced inspection techniques in machined components for the oil and gas sector
To ensure the reliability of manufactured components, it is essential to conduct rigorous inspections. Non-destructive testing enables defect detection without compromising material integrity, reducing operational costs by up to 30% by minimizing failures in critical components before their installation in high-pressure systems. Some types of non-destructive testing used in the inspection of machined parts include:
- Ultrasonic testing (UT): Detects internal cracks in valves, pumps, and high-pressure systems without requiring equipment disassembly.
- Magnetic particle inspection (MT): Ideal for identifying surface defects in ferromagnetic materials used in valves and fittings.
- Infrared thermography: Detects temperature variations in critical components, allowing early identification of wear points or thermal leaks in pumping systems.
The use of penetrant liquids is particularly useful in the inspection of welds in industrial valves and pumps, ensuring that there are no cracks or surface defects. Likewise, welding is used for corrosive environments, especially in pipelines exposed to aggressive fluids.
The use of these methods, along with a metrology room equipped with a measuring arm and other measuring instruments, ensures that components meet the tolerances required in the Oil and Gas industry and extends their service life.
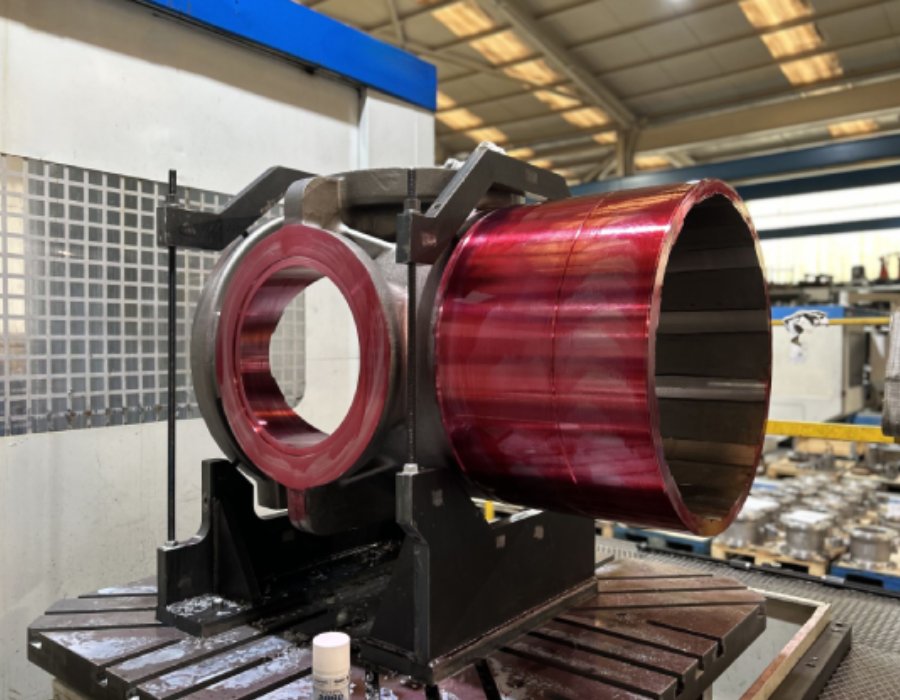
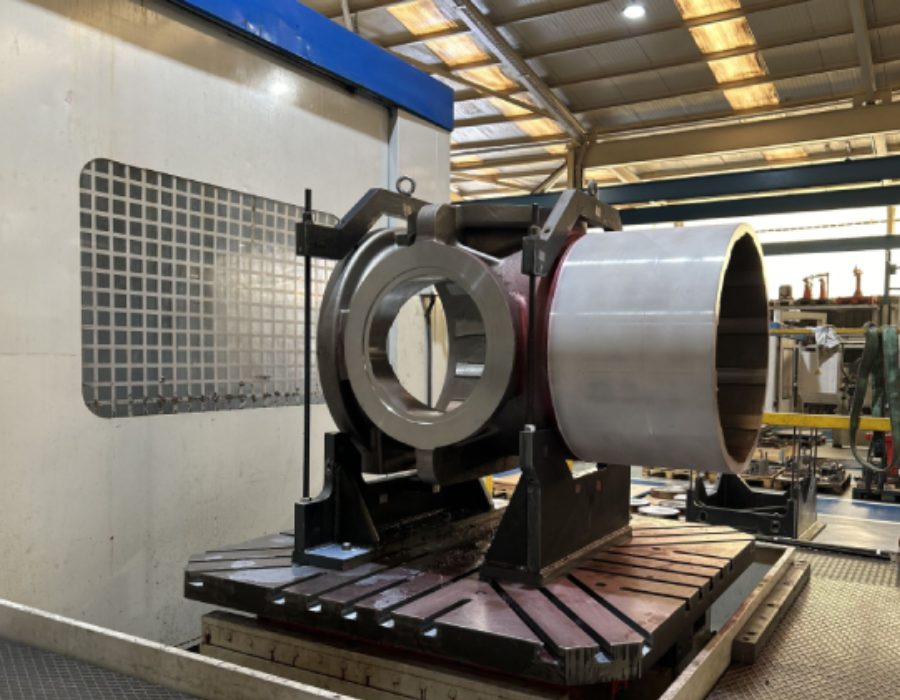
Predictive maintenance and real cases of detected failures
Predictive maintenance allows for the detection of potential failures before they occur, reducing downtime and operational costs.
One of the most common cases in the sector is the premature failure of cryogenic pumps used in the transportation of liquefied natural gas (LNG). Multiple inspections have identified that wear in mechanical seals can lead to efficiency losses in thermal transfer, increasing energy consumption and reducing pumping capacity.
Another example is the maintenance of butterfly valves, where ultrasonic inspections have detected microcracks in the closing discs, preventing catastrophic failures in high-pressure systems. Thanks to this type of predictive maintenance, replacements can be scheduled before equipment suffers irreparable damage.
Regulatory compliance and sustainability in machining for oil and gas
Compliance with API, ASME, and ISO regulations is essential in the manufacturing of components for the Oil and Gas sector. For example, in the production of flow control valves, API 6D certification ensures safety and operational efficiency in pipelines and gas pipelines.
Likewise, oil refining processes depend on the reliability of high-precision machined components. For instance, centrifugal pump impellers used in refining plants require strict tolerances to ensure efficient crude oil circulation at different stages of the process. The correct application of sealing principles in valves, pumps, and piping systems prevents hydrocarbon leaks and improves operational safety.
These certifications guarantee that each manufactured part meets the highest standards of safety, performance, and durability, ensuring its reliability in high-demand environments such as refineries and offshore platforms.
Asimer Group complies with API, ASME, and ISO regulations, ensuring that each machined component meets the highest quality and reliability standards in industrial applications.
Cost optimization and efficiency in machining for the oil and gas sector
In the Oil and Gas industry, optimizing machining processes is key to improving profitability without compromising the quality and precision of components. Through the implementation of advanced technologies and efficient strategies, it is possible to reduce costs in the machining of industrial pumps, valves, and fittings.
Some of the most effective strategies for cost optimization in pump and valve machining include:
- Use of high-performance tools:
- Selecting specialized cutting tools with ceramic coatings increases machining speed and reduces premature wear.
- Tools with tungsten carbide or PVD coatings extend insert lifespan and minimize tool changes, reducing downtime.
- Automation and process control:
- Integrating load and unload robots in CNC machining centers minimizes human errors and improves repeatability.
- Implementing real-time monitoring software optimizes cycle times, detecting process deviations before failures occur.
- Material usage optimization:
- Using optimized chip removal machining strategies reduces material waste in large-volume parts.
- More efficient CNC programming minimizes excess material, lowering raw material costs without compromising component quality.
- Energy consumption reduction:
- Incorporating high-efficiency motors in CNC machines decreases electricity consumption.
- Optimizing machining paths reduces machine operation time, positively impacting process sustainability.
With these strategies, Asimer Group continues to innovate and optimize its machining processes to offer high-performance solutions in manufacturing critical components for the Oil and Gas sector.
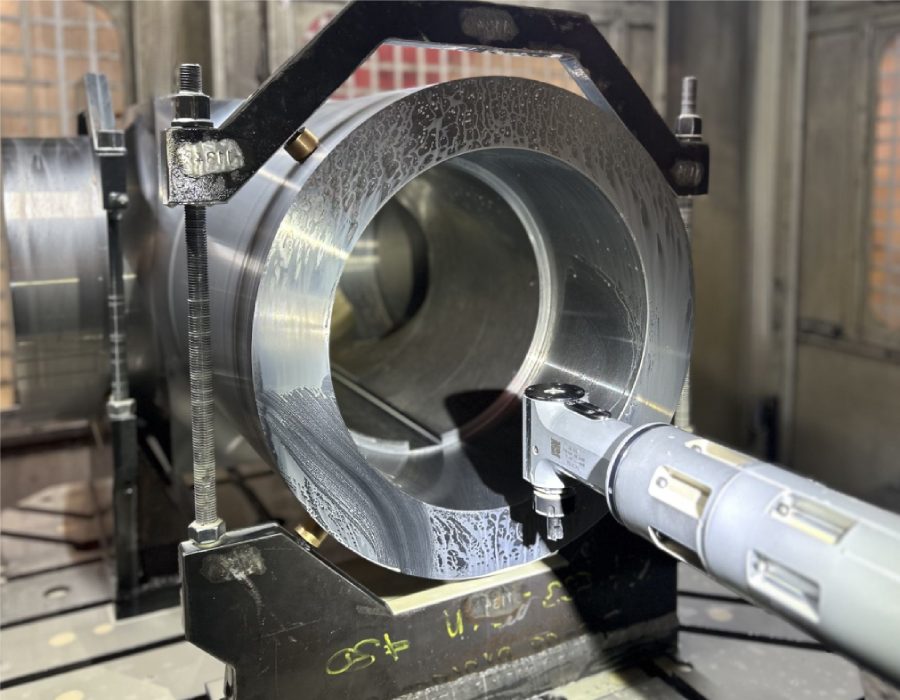
The importance of machining in the sustainability and efficiency of the oil and gas sector
High-precision machining not only improves the quality and durability of components in the Oil and Gas industry but also plays a crucial role in reducing failures and optimizing operational efficiency.
The use of advanced techniques in centrifugal pump manufacturing, as well as in the machining of large-diameter valves, helps reduce material waste and improve the efficiency of fluid transport systems. Additionally, applying methods such as automatic MIG welding and TIG welding in industrial environments enhances component durability.
Finally, implementing strategies to reduce the carbon footprint in industrial pumps and valves is a priority for companies in the sector. The combination of sustainable manufacturing techniques and the use of high-efficiency materials contributes to creating more environmentally friendly systems.
The future of machining in the Oil and Gas sector lies in digitization, automation, and efficient resource use. Optimizing machining processes not only improves business competitiveness but also allows Asimer Group to continue innovating and offering high-value-added solutions to the Oil and Gas industry, contributing to a more efficient and sustainable sector.
Frequently asked questions
What is the difference between CNC machining and conventional machining?
CNC machining uses software and numerical control to manufacture parts with high precision, while conventional machining relies more on the operator’s manual skills.
What are the most commonly used materials in Oil and Gas machining?
Materials such as stainless steel, titanium, and nickel-based superalloys are the most commonly used due to their resistance to corrosion and high temperatures.
How does automation reduce machining costs?
Automation enables more efficient production, reducing waste, cycle times, and errors, optimizing operational costs.
What regulations govern the machining of Oil and Gas components?
Regulations such as API 6A, API 610, and ASME ensure the quality and safety of components used in this critical industry.