CNC technology has truly been a game-changer in demanding sectors like the petrochemical industry. At Asimer Group, we deeply understand the importance of optimizing our processes to remain competitive and efficient in this field.
The petrochemical industry, the backbone of modern society, is undergoing a fundamental transformation driven by advanced CNC machining applications. This extensive article thoroughly explores how Asimer Group, a leader in machining and welding of industrial valves and pumps, along with engineering solutions, is spearheading these innovations, outlining the promising future of the petrochemical industry.
The CNC Technology Revolution
At the heart of the modern industrial revolution in the petrochemical industry lies a fundamental technology: Computer Numerical Control (CNC). This innovation has unleashed a cascade of advancements that have radically transformed the way manufacturing processes are carried out. From high-precision machining to advanced automation, specific component manufacturing, and the integration of cutting-edge technologies, CNC has played a central role every step of the way.
CNC machining tools emerge as the vital heartbeat of excellence in metallurgy. These tools not only represent a revolution in the way we work with metals but are also the key to driving efficiency and quality at every step of the manufacturing process. From millimetric precision to customization capability, CNC machining tools are the pillar upon which a brighter and more sustainable future for the petrochemical industry is built. With their ability to optimize processes and ensure the integrity of crucial components, these tools are truly the pulsating heart of excellence in the metallurgical industry.
Within the fascinating world of the petrochemical industry, CNC machining emerges as a true architect of efficiency and quality. Exploring CNC machining in depth, we discover the authentic art of working metals with computerized control. This technology not only redefines the standards of millimetric precision and customization but also sculpts a more promising and sustainable future for this vital sector.
Efficiency and quality in the petrochemical industry largely depend on precise processes and advanced technology. One key aspect is oil refining, an intricate process that requires a combination of welding and machining of industrial pumps and valves. These pieces are fundamental to ensure the smooth and safe flow of different components in petrochemical facilities. From extraction to distribution, each stage of petroleum refining demands meticulous care, where welding and machining of these pieces play an essential role in ensuring the integrity and efficiency of the entire process. It’s a delicate balance between cutting-edge CNC technology and craftsmanship in material handling, allowing the petrochemical industry to operate with maximum efficiency and quality.
The transformation of pump and valve manufacturing through CNC machining represents a crucial milestone in the evolution of the petrochemical industry. This process has allowed for the creation of components with an unprecedented level of precision and quality, redefining efficiency standards at every stage of petroleum refining. The detailed applications of CNC machining in this field open up a range of possibilities, from optimizing fluid flows to reducing operational costs. In a world where efficiency and quality are imperative, this innovation stands as a fundamental pillar in driving towards a more promising and sustainable future in the petrochemical industry.
Efficiency and quality in the petrochemical industry largely depend on precise processes and advanced technology.
With the ability to program machines with millimetric precision, high-precision machining has become a reality, allowing for the creation of critical components with an unprecedented level of detail and reliability. This extreme precision not only ensures safety and efficiency in the petrochemical industry but also opens doors to new design and functionality possibilities.
Advanced automation driven by CNC has taken operational efficiency to new levels, enabling the execution of complex operations in an automated manner. This capability not only accelerates production times but also reduces human errors and associated costs, significantly improving profitability and competitiveness.
The flexibility and adaptability of CNC are evident in the manufacturing of specific components, where each piece is created to meet the exact demands of a particular application. This customization capability is reinforced by the integration of advanced technologies such as artificial intelligence and machine learning, which optimize processes and enhance the anticipation of potential issues.
CNC-based monitoring and remote control offer constant supervision and effective management of machining processes, providing greater peace of mind and security in petrochemical environments where continuous surveillance is crucial.
In addition to the benefits in terms of precision and efficiency, CNC also contributes to environmental sustainability by reducing waste and optimizing material usage, minimizing both environmental impact and associated costs.
These CNC machining innovations are transforming the petrochemical industry, providing more efficient, precise, and adaptive solutions to the manufacturing challenges presented by this crucial sector. Asimer Group, at the forefront of these innovations, positions itself as a key player in driving excellence and efficiency in the petrochemical industry through advanced CNC machining.
The Transformation of the Petrochemical Industry with CNC Machining
In the context of Industry 4.0, the evolution of CNC machining has redefined processes in the petrochemical industry. Asimer Group, aware of its potential, has integrated these technologies comprehensively, elevating efficiency and quality in the manufacturing of crucial equipment.
Advantages of Advanced CNC Machining Applications in Petrochemicals
CNC technology, led by Asimer Group in the petrochemical industry, ensures accuracy in machining, redefining standards and ensuring the safety and reliability of crucial equipment in this innovative transformation.
- Operational Efficiency and Production Time Reduction
Process automation with CNC not only improves precision but also accelerates production times. At Asimer Group, this efficiency translates into faster deliveries, meeting the demands of a petrochemical industry that requires agile responses.
- Continuous Innovation: Development of Specific Components
The versatility of CNC machining allows for the creation of highly specialized and customized components. Collaboration between Asimer Group and its clients results in tailor-made solutions, addressing the unique challenges of their operations.
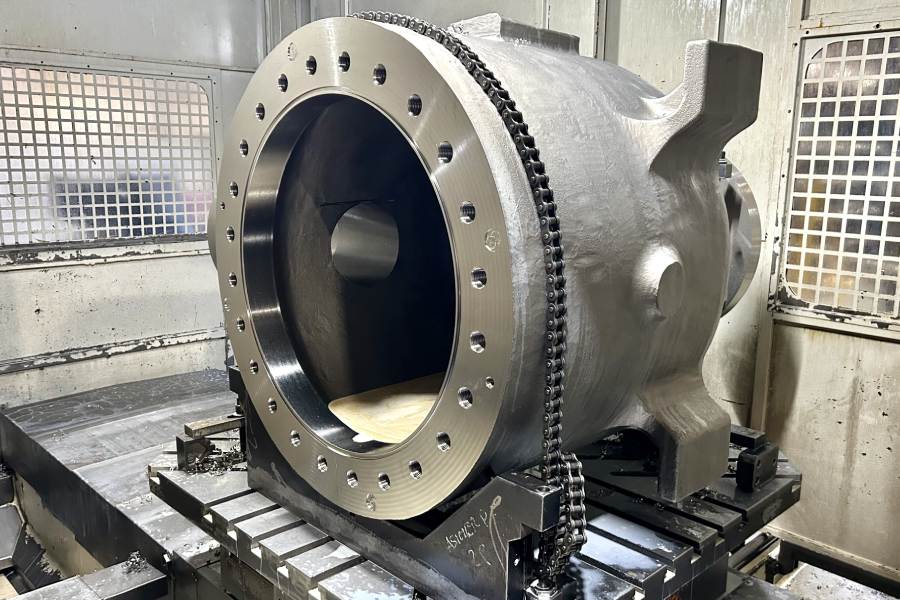
Asimer Group’s Commitment to Quality and Sustainability
Quality and sustainability are pillars on which Asimer Group bases its operation. The integration of CNC technologies enhances product quality, contributing to waste reduction and material optimization, strengthening a sustainable approach.
- Guaranteed Quality: Rigorous Certifications and Standards
Asimer Group adheres to rigorous quality certifications and standards. The implementation of high-precision CNC machining practices ensures that each product complies with the industry’s strictest regulations.
- Environmental Sustainability: Waste Reduction and Material Optimization
CNC technology contributes to sustainability by minimizing waste and optimizing material usage. Asimer Group integrates sustainable practices, setting a higher standard for the industry.
On the other hand, this technology has significantly contributed to improving efficiency and quality in the manufacturing of crucial components for the petrochemical industry, such as industrial pumps and valves. These latter play a crucial role as control gates to regulate the flow of fluids in various operations, from petroleum extraction to refining. This is where energy efficiency becomes a determining factor.
Energy efficiency in industrial valves plays a crucial role in optimizing processes within the petrochemical industry. These valves act as control gates to regulate the flow of fluids in various operations, from petroleum extraction to refining. The incorporation of CNC technology in the manufacturing of these valves has allowed for more efficient and precise designs, reducing energy consumption and minimizing losses during operation. This focus on energy efficiency not only improves the profitability of petrochemical facilities but also contributes to reducing the environmental footprint by decreasing the use of energy resources.
The combination of advanced CNC technology and a firm commitment to energy efficiency reinforces its position as a leader in the sector, driving both profitability and environmental responsibility at every step of the manufacturing process.
The Future of the Petrochemical Industry with CNC Machining
As CNC technology evolves, Asimer Group leads the latest innovations, paving the way for the future of the petrochemical industry.
- Constant Research and Development: The Key to Success
Continuous investment in research and development is the cornerstone of Asimer Group’s prominent position in the market. The company explores new technological frontiers, anticipating future needs and developing innovative solutions.
- Adaptability to Changes: Asimer Group’s Strength
Adaptability is essential in an ever-changing business environment. Asimer Group stands out for its ability to anticipate and adapt to emerging trends, ensuring that its clients benefit from the latest technologies and approaches in petrochemical equipment manufacturing.
Specific Applications of CNC Machining in Petrochemicals
- Process Optimization: Redefining Efficiency
CNC machining is not only about precision but also process optimization. Asimer Group uses this technology to redefine efficiency in the manufacturing of pumps and valves, improving workflows and reducing operating costs.
Asimer Group excels in using CNC machining to manufacture highly specialized components, including the innovative cryogenic valve. This specific application demonstrates the versatility of CNC machining in adapting to the unique demands of the petrochemical industry, providing tailored solutions that ensure efficiency and safety in critical environments.
As Asimer Group leads innovations in CNC machining for the petrochemical industry, it particularly excels in the application of advanced technologies in industrial valve manufacturing. This pioneering approach not only redefines efficiency and precision in production but also positions Asimer Group as a benchmark in implementing technological innovations to enhance quality and safety in the petrochemical industry.
- Product Customization: Meeting Specific Demands
In a market where customization is key, CNC machining allows Asimer Group to meet the specific demands of its clients. The ability to quickly adjust production to changing requirements ensures customer satisfaction and competitiveness in the market.
The Innovative World of the Petrochemical Industry: Integration of Asimer Group’s Metrology and Quality Inspection Room
In this innovative world of the petrochemical industry, where precision plays a crucial role, Asimer Group stands out for excellence in integrating the Metrology and Quality Inspection Room. From meticulous measurement and quality assessment to the implementation of non-destructive tests, this facility becomes the epicenter of impeccable standards that underpin the excellence of Asimer Group. The synergy between technology and precision is evident, as the room not only uses advanced measuring instrument technologies, such as the innovative measuring arm, but also seamlessly integrates with the Trevisan Machining Center.
This cutting-edge approach by Asimer Group extends beyond the petrochemical industry, encompassing critical sectors such as oil and gas, naval, pulp and paper, cryogenics, desalination, and water and wastewater management. The synergy between technology and precision, evident in the Metrology Room, reinforces Asimer Group’s position as a leader not only in CNC machining but also in delivering adaptive solutions for various industrial applications. Here, technology is not just a tool but an essential driver of operational success and sustainability in the manufacturing of petrochemical equipment.
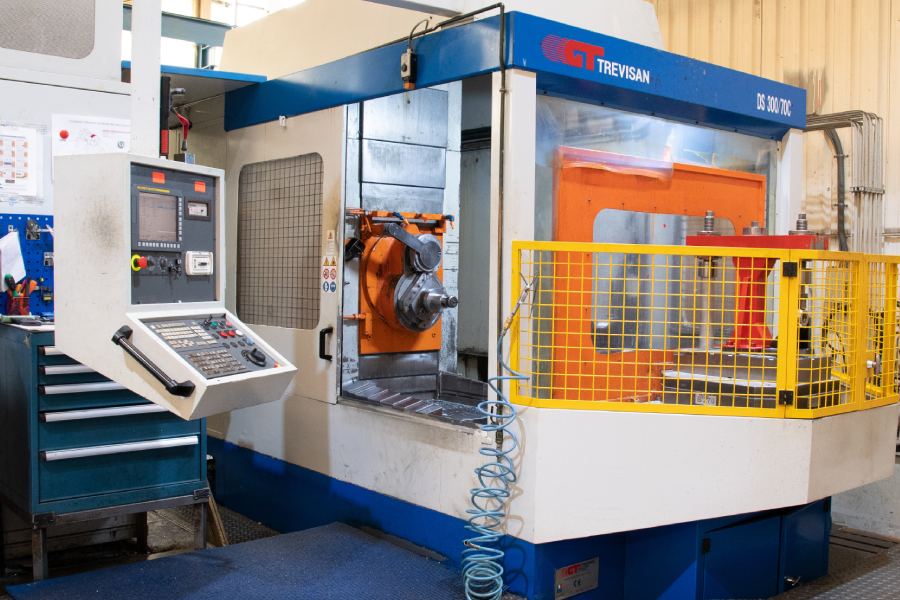
Driving Success in the Petrochemical Industry
In the petrochemical industry, CNC technology has emerged as an indispensable tool for enhancing efficiency and quality in the manufacturing of key components. The precision and reliability offered by this technology are crucial to ensuring success in such a demanding environment as petrochemicals. By linking this article with “Chip Removal Machining in the CNC Era,” we can explore how this technology is transforming the petrochemical industry and improving its efficiency and quality.
CNC technology has proven to be an invaluable asset for the petrochemical industry, driving efficiency and quality to unprecedented levels. However, its true value lies in its ability to foster innovation and environmental consciousness.
By embracing CNC technology, we are building a future where excellence and sustainability go hand in hand. Every advancement in this technology brings us closer to that goal, but it also presents us with challenges that we must overcome with creativity and determination.
Ultimately, CNC technology represents more than just improvements in manufacturing; it is a symbol of our commitment to a better and more responsible future. By continuing to progress cautiously and responsibly, we can harness its full potential for the benefit of both industry and the environment.