Certification in non-destructive testing (NDT) is a key component for guaranteeing quality, safety, and efficiency in modern industry. In an environment where the integrity and functionality of critical components are essential, having certified personnel ensures that procedures are carried out to the highest standards. At Asimer Group, we understand that certification not only raises quality levels but also strengthens trust in the solutions offered to our clients.
In this article, we will explore the importance of NDT certification, the most recognized applicable standards, and the benefits it provides to both professionals and companies. We will also share success stories that demonstrate the positive impact of integrating certified NDT into industrial projects.
The Importance of certification in Non-Destructive Testing
In industry, non-destructive testing enables materials and components to be inspected without compromising their integrity. This approach is essential for guaranteeing accuracy in CNC machining, particularly in sectors where accuracy is a fundamental requirement. However, the effectiveness of these methods largely depends on them being carried out by highly trained and certified technicians according to international standards. NDT certification ensures that operators have the theoretical knowledge and practical skills to perform tests accurately and reliably.
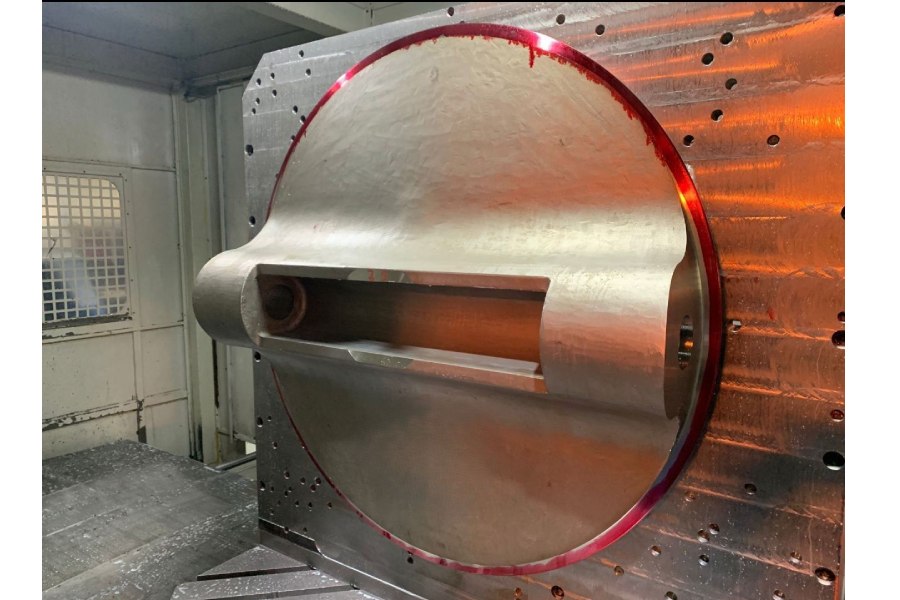
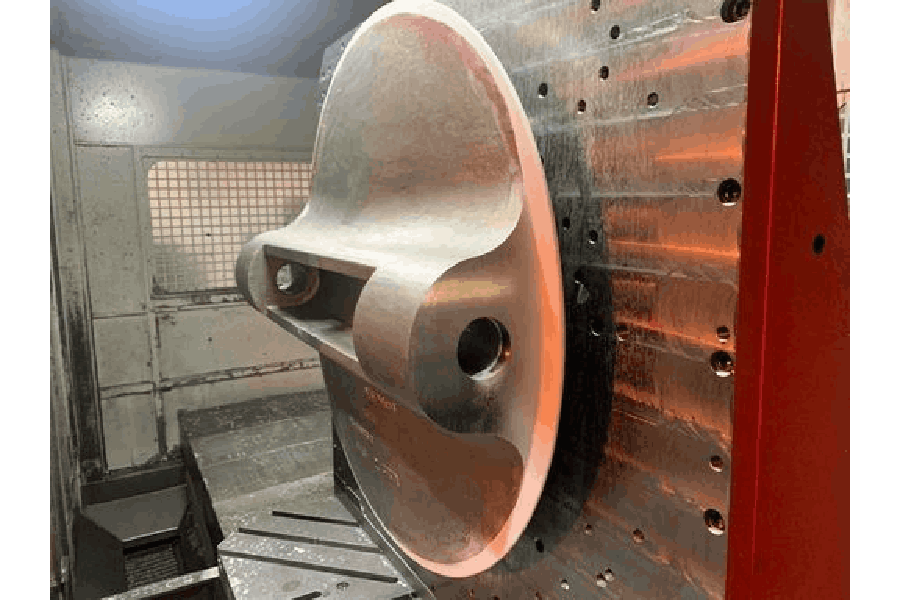
Why is certification essential?
- Guarantees Process Quality
NDT is used in sectors where safety and precision are critical, such as petrochemical, cryogenic, and naval industries. Only certified technicians can ensure consistent and reliable results. - Minimizes Operational Risks
Early detection of defects is vital to prevent failures that could lead to material, human, or environmental damage. Certification ensures operators are prepared to identify and evaluate these risks effectively. - Compliance with International Standards
Many industries are subject to strict regulations requiring specific certifications. Meeting these standards not only avoids penalties but also enhances competitiveness in international markets. - Builds Customer Trust
Companies with certified personnel project an image of professionalism and a commitment to excellence.
Additionally, certification ensures that processes such as TIG welding, automatic MIG welding, and PTA welding meet the technical requirements demanded in sectors like water treatment, oil refining, and cryogenic applications.
Certification is also essential for industries operating under the principles of Industry 4.0, where the integration of advanced technologies ensures more efficient and precise control of industrial processes.
Applicable standards in NDT certification
NDT certification is regulated by a series of international standards that define competence and procedural requirements. These standards not only ensure the quality of tests but also standardize practices globally, facilitating collaboration between companies in different countries.
ISO 9712: Certification of personnel in NDT
The ISO 9712 standard is a key reference for certifying personnel conducting non-destructive testing. It is designed to assess technical competencies and establish a common framework across various industrial sectors.
Certification Levels
- Level I: Operators trained to perform tests following written instructions under supervision.
- Level II: Professionals capable of selecting testing techniques, interpreting results, and supervising NDT activities.
- Level III: Experts responsible for developing procedures, leading NDT programs, and training other levels.
ISO 9712 is applied in sectors such as petrochemical, automotive, and water treatment, ensuring standardization in critical processes.
ASNT: Flexibility and global recognition
The certification scheme of the American Society for Nondestructive Testing (ASNT) is one of the most widely accepted worldwide. It offers a flexible approach that adapts to various industries, from aerospace to heavy construction.
Advantages of ASNT Certification
- Theoretical and Practical Evaluation: Candidates must demonstrate comprehensive knowledge and practical skills.
- International Recognition: This certification facilitates job mobility and ensures compliance with global standards.
- Sectoral Adaptability: It adjusts to the specific needs of each industry, enabling effective implementation.
EN 4179: Specialization in the aerospace industry
This standard is particularly relevant to the aerospace industry, where safety is of vital importance. It establishes requirements for the qualification and certification of NDT personnel working with aeronautical components.
Applications
- Inspection of fuselages and engines to detect microcracks or wear.
- Monitoring of structures subjected to extreme operating conditions.
At Asimer Group, we have participated in projects where the application of EN 4179 was crucial to ensuring the integrity of critical components.
The use of technologies such as CNC technology, chip removal machining, and Trevisan machining centers has complemented the implementation of these standards.
Other relevant standards
- ISO 9001: While not directly related to NDT, this standard ensures that quality management systems support consistent and effective testing implementation.
- API 1169: Used in the oil and gas pipeline industry, this standard ensures the inspection of critical infrastructure using certified NDT.
These standards are also key when selecting and applying the most suitable types of non-destructive testing for each industry, including analyzing types of industrial valves and inspecting industrial pumps.
Success stories in NDT implementation
At Asimer Group, we have implemented NDT in key projects with excellent results. Here are two examples among many:
1. Double isolation & bleed split ball valve bodies
We completed 7 sets of valve bodies and covers for Double Isolation & Bleed Split Ball Valves (8”x6” 2500#) for a French client specializing in highly specialized valves for the oil and gas markets. This project included:
- Raw material acquisition (7 pieces in A105 Ø420x640mm + 7 pieces Ø420x380mm, with 3.2 certificates).
- Pre-machining steps.
- Coating with ALLOY 625 in sealing areas (according to ASME standards) and WPS/PQR/WPQ, following the inspection plan (ITP).
- Post-weld heat treatment (PWHT) and intermediate inspections using NDT.
- Final machining steps.
- Non-destructive testing (PT, UT, VT, and PMI) performed by Level II certified operators.
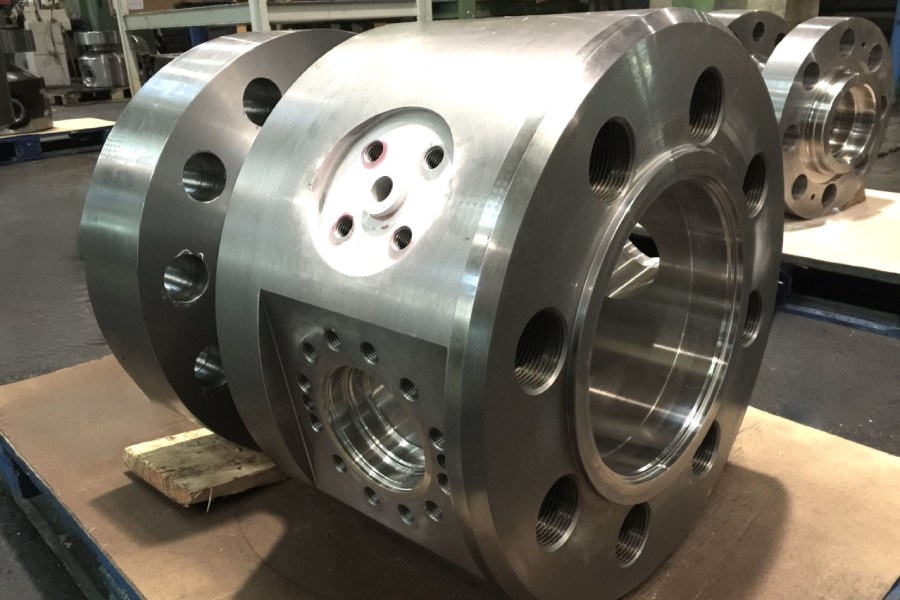
2. Centrifugal pump casings
We worked on 5 centrifugal pump casings made from CA6NM cast material for a French client in the thermal oils sector.
- Initial pre-machining.
- Liquid Penetrant testing (PT) on sealing surfaces before final machining.
- Final precision machining.
- Final non-destructive tests (PT and VT) performed by Level II certified operators.
In addition to NDT, our engineering solutions include services such as specialized welding and advanced inspection technologies, offering complete integration into industrial projects.
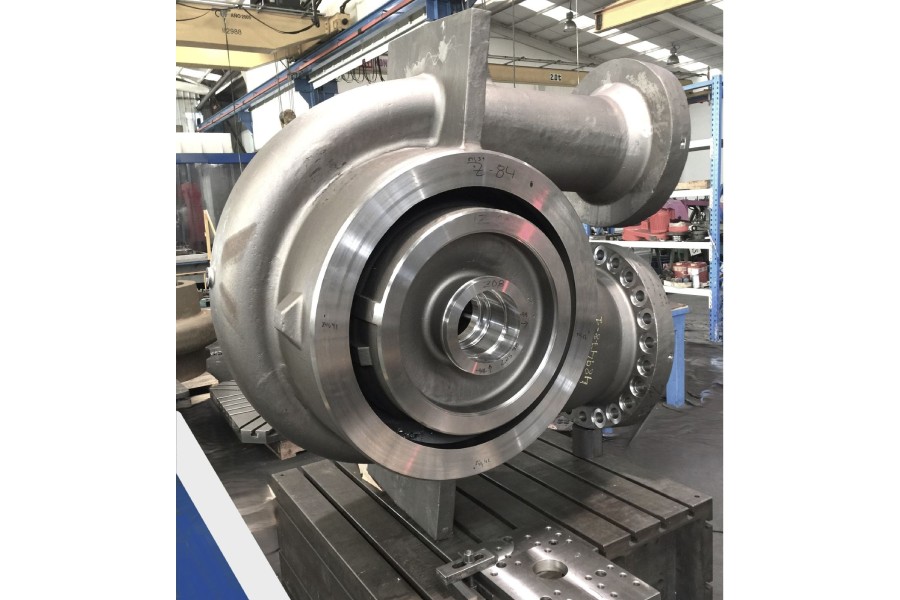
Benefits of NDT standards for companies
Adopting international NDT standards not only guarantees quality but also provides significant competitive advantages:
- Access to International Markets: Globally recognized certifications allow companies to operate in multiple countries without regulatory barriers.
- Optimization of Internal Processes: Following standards helps standardize procedures, reducing errors and improving efficiency.
- Regulatory and Legal Compliance: Ensures products and processes meet legal requirements, avoiding penalties or litigation.
- Enhanced Reputation: Companies that comply with recognized standards are perceived as leaders in quality and safety.
Tools like measurement instruments, the measuring arm, and inspections conducted in a metrology room are fundamental for validating the results obtained through NDT.
Conclusion
NDT certification is more than just a technical requirement; it is a strategic pillar for ensuring quality, safety, and competitiveness in modern industry. Standards such as ISO 9712, ASNT, and EN 4179 provide a solid framework that ensures the competence of technicians and the reliability of results.
At Asimer Group, we understand the importance of these certifications and work continuously to integrate the most demanding standards into all our projects. From petrochemical to cryogenic sectors, our certified processes guarantee reliable and high-quality solutions.
If you are looking for a partner committed to excellence in NDT, contact us. We are here to transform the quality of your industrial processes and take your operation to the next level.