Maintenance of butterfly valves is essential for their optimal performance and to extend their durability. These valves play a crucial role in various industries from the oil & gas sector to the naval industry, petrochemicals, applications in nuclear plants, water treatment, cryogenic processes, desalination, paper mill production, and HVAC systems, due to their efficiency in controlling liquid flows. Proper care not only prevents unexpected failures but also reduces downtime, thereby increasing cost-effectiveness in repair expenses.
Consequences of Poor Maintenance
Inadequate maintenance of butterfly valves can lead to a series of significant problems for any industrial operation. Among the most frequent complications are leaks, which not only compromise the system’s integrity but also can result in significant resource losses and environmental risks. Furthermore, blockages are another common consequence of neglecting maintenance, causing obstructions that affect fluidity and the overall performance of the equipment.
Accelerated component wear is another direct consequence, which not only reduces the valve’s lifespan but also increases long-term operating costs by requiring more frequent repairs or even premature replacements. These unplanned interruptions not only incur additional costs but can also affect production and operational efficiency.
Neglect in maintenance not only has economic repercussions but also poses a safety risk, as poorly maintained valves can fail at critical moments, endangering both personnel and infrastructure. In terms of regulatory compliance, failure to adequately maintain valves can result in legal and regulatory sanctions, in addition to damaging the company’s reputation.
Tools and Equipment Necessary for Butterfly Valve Maintenance
To carry out effective maintenance of butterfly valves, it is essential to have a variety of specialized tools and equipment that ensure both accuracy in inspection and the safety of personnel involved in these critical tasks.
Inspection Equipment
For effective maintenance, specific inspection equipment such as inspection cameras, pressure gauges, and infrared thermometers are indispensable as they facilitate a detailed evaluation of the valve’s condition and help identify problems before they worsen.
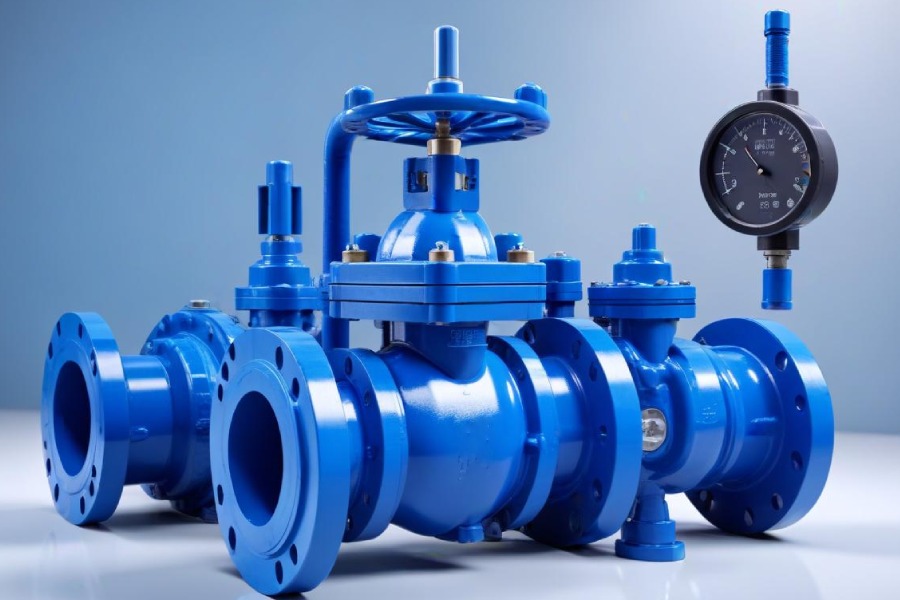
Cleaning Instruments
Regular cleaning is crucial to preserve the proper performance of valves. Tools such as brushes designed to access difficult internal areas and pressure washing equipment are useful for effectively removing residues and build-ups that could block fluid flow or affect tightness. Additionally, the use of specific chemicals may be required to dissolve more stubborn deposits without damaging the valve components.
Protection and Safety Equipment
The use of safety equipment is vital during valve maintenance to protect personnel. Elements such as gloves, goggles, and respiratory protection are essential to prevent injuries and ensure a safe working environment.
Preventive Maintenance Procedures for Butterfly Valves
At the heart of an efficient flow system in various industries, butterfly valves play a critical role in liquid and gas control and handling. Ensuring their optimal performance is crucial to prevent interruptions and extend the system’s lifespan.
Visual Inspection
Performing a thorough visual inspection is the crucial first step in any preventive maintenance program for butterfly valves. This procedure involves not only identifying obvious signs of wear and corrosion but also detecting leaks, deformities, or any anomalies in critical components such as gaskets, actuators, and seals. Early detection of these issues can prevent unexpected failures and costly operational shutdowns, allowing for timely interventions to optimize performance and extend the valves’ lifespan. Additionally, this inspection helps verify the correct alignment and lubrication of moving parts, vital aspects for efficient and safe system operation. Therefore, regular visual inspection is indispensable to maintain the integrity and reliability of butterfly valves within any facility.
Non-Destructive Testing and its Importance in the Industry
Non-destructive testing (NDT) procedures are vital for butterfly valve maintenance as they allow for evaluating the integrity and condition of these components without damaging them. Methods such as ultrasonic testing, radiography, magnetic particle testing, and liquid penetrant testing are used to detect cracks, corrosion, and other internal or surface defects. Implementing NDT in preventive and corrective maintenance programs helps identify issues before they become critical failures, ensuring operational reliability and safety. Furthermore, NDT helps extend the lifespan of valves, reducing costs associated with unexpected repairs and replacements.
Continuous Cleaning
Continuous cleaning of butterfly valves is not only a recommended practice but a necessity to ensure their optimal and efficient operation. This task should include the meticulous removal of sediments, residues, and contaminants that can accumulate on the surface and internal mechanisms of the valve. These contaminants may come from the fluid circulating through the valve or the external environment, especially in areas with high exposure to suspended particles.
Regular cleanings help prevent issues such as blockages, uneven wear, and general deterioration that could compromise the integrity and performance of the valve. Additionally, this cleaning ensures that components such as seals and bearings remain in good condition and operate effectively, preventing leaks and other operational issues.
The cleaning process should be carried out with appropriate products and techniques to avoid damaging the valve materials. Depending on the type of contaminant and frequency of use, this procedure can range from a simple wash to more complex techniques such as using specific solutions or specialized tools. The frequency of these cleanings should also be adapted to the operating conditions, ensuring that the valves always operate under ideal conditions for performance.
Component Lubrication
Lubricating components is essential to maintain the performance and durability of butterfly valves. This process significantly reduces wear and friction of moving parts, key to ensuring smooth and efficient operation. It is essential to always use lubricants recommended by the manufacturer to not compromise the integrity of materials and the effectiveness of the mechanism.
In addition to following the manufacturer’s specifications for the type of lubricant, it is equally important to pay attention to the lubrication frequency. This will depend on the valve’s usage and the specific environmental conditions in which it operates, such as temperature and exposure to contaminants. In more demanding environments, it may be necessary to increase the lubrication frequency to prevent the accumulation of residues and corrosion that could prematurely deteriorate the moving parts.
Moreover, regular checks should be carried out to verify that the lubrication remains adequate and that the lubricants have not degraded, which could affect the valve’s performance. A good maintenance practice not only extends the life of valves but also contributes to overall system efficiency and safety.
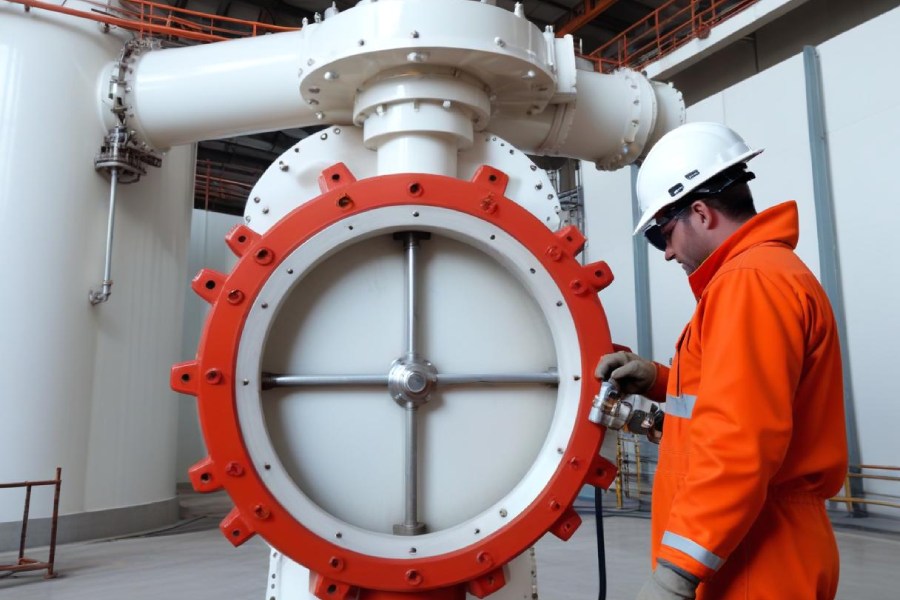
Corrective Maintenance Procedures
Leak Identification and Repair
Leaks in butterfly valves can indicate serious issues. Detecting leaks can be done using specialized leak detectors or visual inspection. In the case of damaged components, processes such as machining large-scale valves ensure that parts are accurately restored or replaced to maintain efficient operation.
Find out how to prevent leaks and improve sealing in industrial systems, especially in the oil and gas sector, using fittings designed to optimize operational safety and extend equipment lifespan.
Replacement of Gaskets and Seals
Renewing gaskets and seals in butterfly valves is an essential task to maintain the integrity and efficiency of the industrial system. These elements are crucial to ensure valve tightness and prevent leaks that could affect operational safety and efficiency.
When gaskets and seals show signs of wear, either from exposure to high temperatures, corrosive chemicals, or prolonged use, it is vital to proceed with their replacement. This process not only restores the valve’s original function but also prevents leaks that could lead to product losses, environmental contamination, or safety risks for personnel.
The replacement procedure typically involves several detailed phases. First, it must be ensured that the system is completely isolated and the valve is depressurized to prevent accidents during maintenance. Subsequently, the old gaskets and seals are carefully removed, paying attention not to damage the valve’s internal surfaces. It is essential to choose replacement gaskets and seals that meet the valve’s exact specifications and specific operating conditions, considering factors such as temperature, pressure, and fluid type.
The precise placement of the new gaskets and seals is crucial to ensure effective sealing. This may include the application of special lubricants or sealant compounds as needed to ensure tightness and resistance to adverse conditions. After installation, it is advisable to perform leak tests to confirm the effectiveness of the replacement and verify that the valve operates correctly before reintegrating it into the system.
Repair of Damaged Components
In case of significant damage to valve components, repairs are necessary. This may include the replacement of damaged parts, adjustments, and alignments. Carrying out these repairs in a timely manner ensures that the valve continues to operate efficiently and safely.
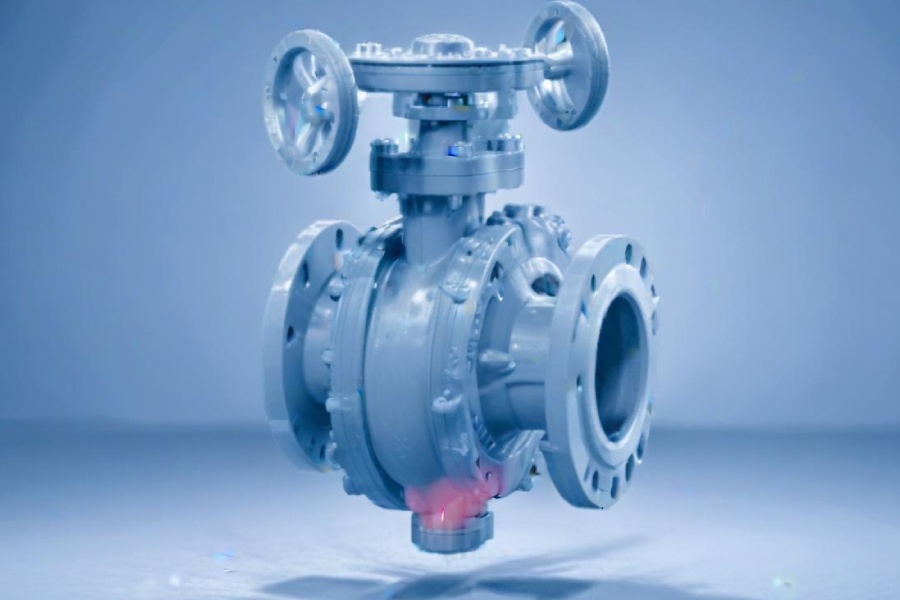
Frequency and Maintenance Scheduling
Preventive Maintenance Programs
Developing a preventive maintenance program is essential to ensure the longevity and efficient operation of butterfly valves. This program should include a detailed list of maintenance tasks and their frequencies based on the manufacturer’s recommendations and specific operating conditions.
Comparison with Axial Flow Check Valve
Axial flow check valves and butterfly valves have different applications and designs, leading to differences in their maintenance.
Axial flow check valves are designed to allow flow in one direction and prevent backflow, being essential in systems where preventing reverse flow is critical. Maintenance of these valves focuses on ensuring the check mechanism functions correctly, requiring regular inspections of discs, springs, and seats to prevent leaks and blockages.
In contrast, maintenance of butterfly valves focuses on the integrity of the rotating disc and the valve body, as well as proper lubrication and cleaning to ensure efficient flow control. Both valves require visual inspection procedures and non-destructive testing to identify issues before they become critical failures, but the specifics of each valve type dictate particular maintenance techniques and frequencies.
For efficient management of preventive maintenance for butterfly valves, it is crucial to understand the different types of industrial valves and their specific applications, ensuring optimal operation and prolonging their lifespan.
Furthermore, proper maintenance can improve energy efficiency in industrial valves, reducing operational costs and enhancing system sustainability.
Comparison with Diaphragm Valves
Compared to butterfly valves, diaphragm valves require special attention to the integrity of their diaphragm and precision in adjusting their actuator, ensuring optimal fluid handling in hygienic and high-purity environments. To learn more about their characteristics and applications, visit our article on Diaphragm Valve: Features and Applications in the Industry.
Inspection and Service Intervals
Establishing inspection and service intervals based on valve usage and environmental conditions is essential. Valves operating in extreme conditions may require more frequent inspections and maintenance. Adjusting these intervals based on operational experience and manufacturer recommendations ensures proper and timely maintenance.
Best Practices for Butterfly Valve Maintenance
Employee Training
It is essential that maintenance personnel receive appropriate training. Employees should be well-versed in proper maintenance techniques, as well as the correct use of tools and equipment and safety regulations. Ongoing training and knowledge refreshment contribute to efficient maintenance and ensure safety.
Recordkeeping and Maintenance Monitoring
Maintaining thorough documentation of all maintenance-related activities is an essential practice. This includes noting inspections, cleaning procedures, lubrications, repairs, and component changes. Rigorous monitoring and accurate records facilitate effective management and help detect trends or common issues.
Use of Original Components and Parts
It is essential to use original components and parts, as recommended by the manufacturer, to ensure both compatibility and the best performance of butterfly valves. Avoiding counterfeit or low-quality components is crucial to prevent operational failures and prolong the valve’s lifespan.
Alerts and Problem Diagnosis
Common Failure Indicators
Paying attention to common signs of malfunction in butterfly valves is of vital importance. These signs include unusual sounds, resistance when turning the valve, leaks, and variations in system pressure. Identifying these indicators early facilitates quick action and prevents major complications.
Detection of Potential Problems
To identify emerging issues, conducting visual inspections combined with operational tests and the use of diagnostic equipment is essential. Early recognition of problems such as corrosion, advanced wear, and defects in seals helps prevent serious breakdowns and keeps the system in optimal operating conditions.
Conclusion
Proper maintenance of butterfly valves provides multiple benefits, such as optimal system performance, reduced downtime, extended valve lifespan, and savings in repair and replacement costs. A well-planned and executed maintenance program ensures that valves operate effectively and reliably.
Consistency and proper maintenance planning are essential for the safe and efficient operation of butterfly valves. Following manufacturer recommendations, adjusting maintenance intervals based on operational conditions, and keeping detailed records of all maintenance activities are essential practices to ensure the longevity and optimal performance of these critical valves. A proactive maintenance approach not only prevents issues but also optimizes overall system operation and enhances safety in the workplace.