Automatic Mig Welding: Benefits, applications and innovations
Automatic Mig Welding: Benefits, applications and innovations
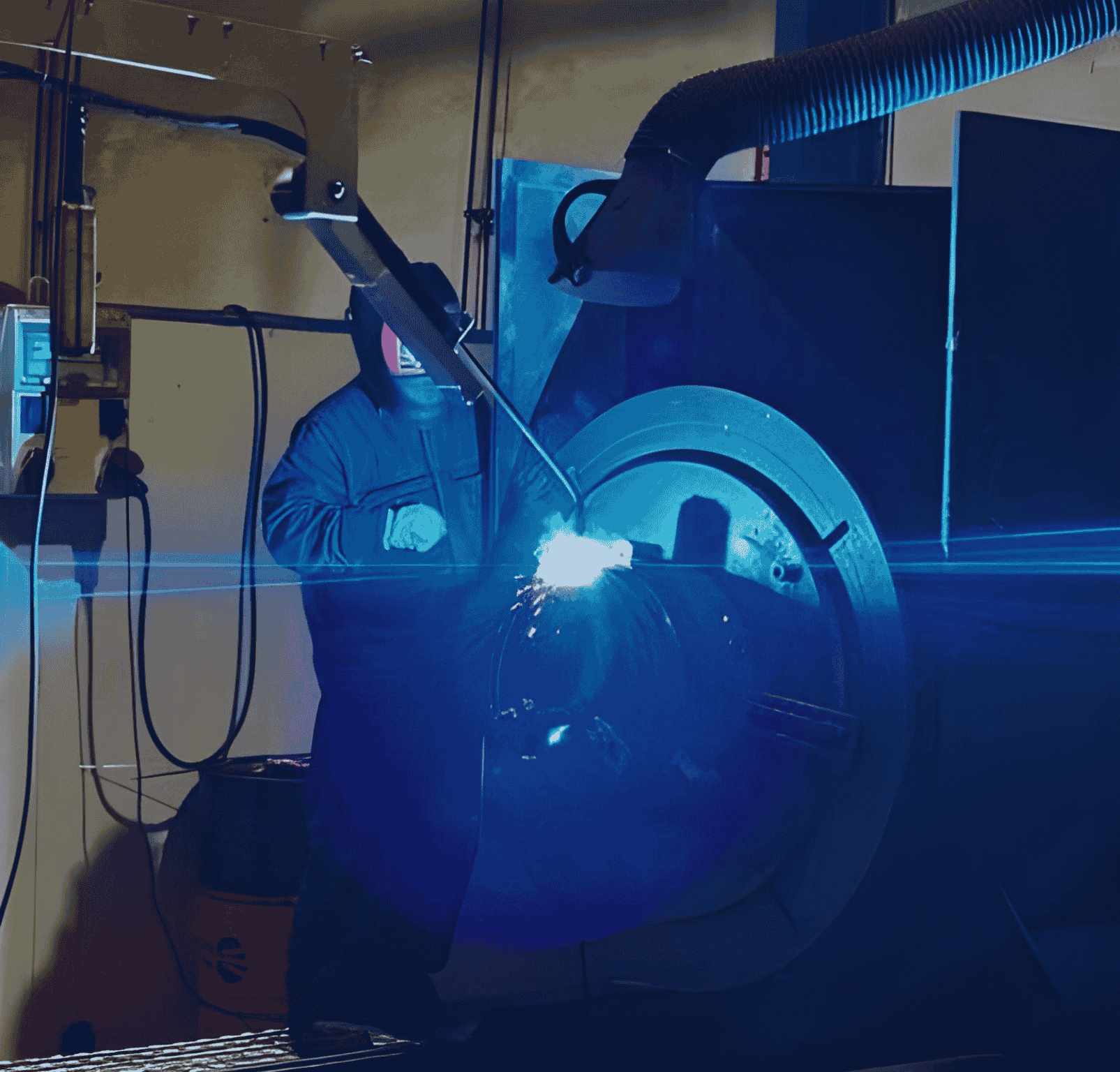
What is MIG automatic welding?
Automatic MIG welding is driving a significant transformation in the manufacturing and repair of key industrial components, such as pumps, valves, and compressors. As the demand for more durable, precise, and efficient products continues to grow, automation has become an essential tool for optimizing processes in highly demanding industrial sectors. At Asimer Group, we have embraced automatic MIG welding technology to provide solutions that maximize productivity and quality, exceeding industry standards.
MIG welding (Metal Inert Gas), known for its versatility and efficiency, has evolved with the integration of automated systems, such as welding machines and digital control equipment. Instead of relying on the operator to manage the electric arc, wire feeding, and shielding gas application, automatic MIG welding utilizes automated welding machines and advanced monitoring systems that execute the process with precision and consistency.
Automation in MIG welding enables more precise control over key parameters such as wire speed, voltage, and current, resulting in high-quality welded joints. This is particularly critical in the manufacturing of compressors, pumps, and valves, where components must withstand extreme pressure and temperature conditions without failure.
Benefits of automatic MIG welding in the pump and valve industry
Increased productivity and greater efficiency
In industrial sectors such as compressor design and manufacturing, as well as the production of pumps and valves, where large-scale production and precision are essential, automatic MIG welding provides a significant advantage. Automated systems can operate continuously for extended periods without the need for interruptions, enabling faster production cycles and a higher volume of welded components in less time.
Furthermore, automation reduces the need for rework, as the process is highly controlled and repeatable. This means that manufacturers can meet tighter deadlines without compromising product quality, a key advantage for companies that rely on efficiency to stay competitive.
To ensure the integrity of welds in critical components such as compressors, pumps, and industrial valves, it is essential to complement automatic MIG welding with advanced inspection techniques. In this regard, penetrant testing is an essential tool for detecting potential defects that could compromise weld performance in demanding environments.
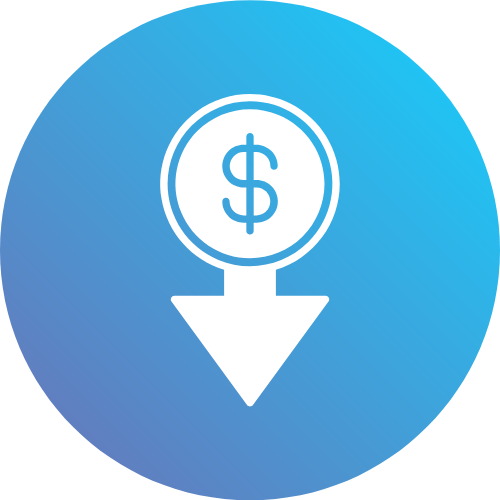
Reduced operating costs
While the initial investment in automated welding systems can be considerable, the long-term benefits far outweigh this expense. Operating costs decrease significantly due to several key factors:
- Reduced material waste, as the process is more precise and controlled.
- Optimization of consumable usage, such as welding wire and shielding gases, by automatically adjusting parameters according to the specific requirements of each job.
- Decreased downtime.
To ensure that all manufactured components meet the strict quality and precision standards demanded by the pump and valve industry, we conduct rigorous inspections of each part in our metrology room. We use high-precision equipment to validate every welding process. This comprehensive approach allows us not only to reduce costs but also to ensure maximum reliability in every project.
For manufacturers of compressors, pumps, and valves, cost reduction not only translates into higher profit margins but also into greater competitiveness in the market, especially for large-scale projects or complex production series. If your company is looking for advanced technologies to optimize the manufacturing of critical industrial components, our engineering solutions offer a comprehensive approach that maximizes both quality and efficiency in every production process.
Constant accuracy in each weld
Precision is a critical factor in the manufacturing of compressors, valves, and industrial pumps, where even the slightest error can compromise the structural integrity of the components. Automatic MIG welding machines eliminate the typical variations found in manual processes, ensuring consistently high-quality welds in every joint.
This level of precision is especially important in the welding of valves and pumps that operate under high pressure and extreme temperatures. Automation minimizes defects such as cracks, porosities, and spatter, ensuring superior performance of the components throughout their lifecycle.
To ensure that each component meets the most stringent industry standards, at Asimer Group we use high-precision measuring and testing instruments, allowing us to verify weld accuracy and guarantee maximum reliability under demanding operating conditions.
For this purpose, we utilize advanced tools such as the measuring arm, which enables us to verify the accuracy of welded joints and ensure they meet the rigorous quality requirements of the industrial sector.
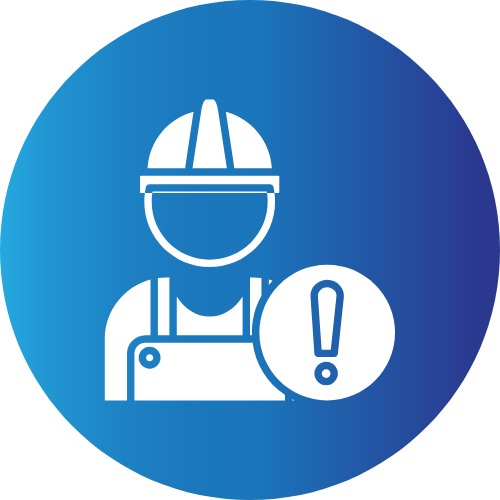
Greater safety
  for operators
Automation in welding not only enhances efficiency and precision but also improves safety. Automatic welding machines carry out welding tasks in hazardous environments, while operators supervise the process from a safe distance. This significantly reduces risks associated with exposure to high temperatures, hazardous gases, and ultraviolet radiation.
Moreover, in the pump and valve manufacturing sector, it is essential to perform non-destructive testing to ensure that welds meet the highest standards of quality and safety. These tests allow for the detection of potential defects without compromising the structural integrity of the components, ensuring optimal performance under extreme conditions.
At Asimer Group, we ensure that our automated processes comply with the strictest safety regulations, protecting both our personnel and the equipment involved. We hold the UNE-EN ISO 3834-2 Certification, which guarantees meticulous quality control in all aspects of welding manufacturing. This standard establishes comprehensive quality requirements for the fusion welding process of metallic materials.
Benefits of automatic MIG welding in the pump and valve industry
Increased productivity and greater efficiency
In industrial sectors such as compressor design and manufacturing, as well as the production of pumps and valves, where large-scale production and precision are essential, automatic MIG welding provides a significant advantage. Automated systems can operate continuously for extended periods without interruptions, enabling faster production cycles and a higher volume of welded components in less time.
Furthermore, automation reduces the need for rework, as the process is highly controlled and repeatable. This means that manufacturers can meet tighter deadlines without compromising product quality, a key advantage for companies that rely on efficiency to remain competitive.
To ensure the integrity of welds in critical components such as compressors, pumps, and industrial valves, it is essential to complement automatic MIG welding with advanced inspection techniques. In this regard, penetrant testing is an essential tool for detecting potential defects that could compromise the performance of welds in demanding environments.
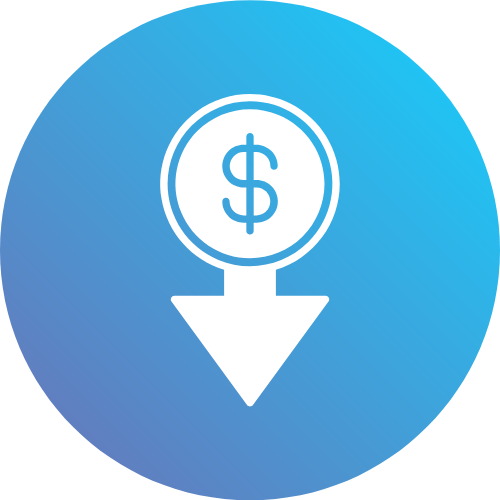
Reduced operating costs
Although the initial investment in automated welding systems can be considerable, the long-term benefits far outweigh this expense. Operating costs decrease significantly thanks to several key factors:
- Reduced material waste, as the process is more precise and controlled.
- Optimization of consumable usage, such as welding wire and shielding gases, by automatically adjusting parameters according to the specific needs of each job.
- Minimized downtime.
To ensure that all manufactured components meet the strict quality and precision standards demanded by the pump and valve industry, we conduct rigorous inspections of each part in our metrology room. Using high-precision equipment, we validate every welding process. This comprehensive approach not only helps reduce costs but also ensures maximum reliability in every project.
For manufacturers of compressors, pumps, and valves, cost reduction not only translates into higher profit margins but also into greater competitiveness in the market, especially for large-scale projects or complex production runs. If your company is looking for advanced technologies to optimize the manufacturing of critical industrial components, our engineering solutions provide a comprehensive approach that maximizes both quality and efficiency in every production process.
Constant precision in each weld
Precision is a critical factor in the manufacturing of compressors, valves, and industrial pumps, where even the slightest error can compromise the structural integrity of the components. Automatic MIG welding machines eliminate the typical variations found in manual processes, ensuring consistently high-quality welds in every joint.
This level of precision is especially important in the welding of valves and pumps that operate under high pressure and extreme temperatures. Automation minimizes defects such as cracks, porosity, and spatter, ensuring superior component performance throughout their lifecycle.
To ensure that each component meets the strictest industry standards, at Asimer Group, we use high-precision measuring and testing instruments, allowing us to verify weld accuracy and guarantee maximum reliability under demanding operating conditions.
For this purpose, we rely on advanced tools such as the measuring arm, which allows us to verify the accuracy of welded joints and ensure they meet the stringent quality requirements of the industrial sector.
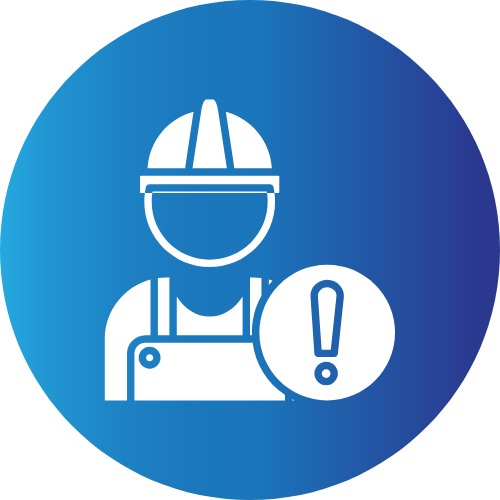
Greater safety
  for operators
Automation in welding not only enhances efficiency and precision but also increases safety. Automatic welding machines perform welding tasks in hazardous environments, while operators supervise the process from a safe distance. This significantly reduces risks associated with exposure to high temperatures, hazardous gases, and ultraviolet radiation.
Additionally, in the pump and valve manufacturing sector, non-destructive testing (NDT) is essential to ensure that welds meet the highest standards of quality and safety. These tests help detect potential failures without compromising the structural integrity of the components, ensuring optimal performance under extreme conditions.
At Asimer Group, we ensure that our automated processes comply with the strictest safety regulations, protecting both our personnel and the equipment involved. We hold the UNE-EN ISO 3834-2 Certification, which guarantees meticulous quality control in all aspects of welding manufacturing. This standard establishes comprehensive quality requirements for the fusion welding process of metallic materials.
Applications of automatic MIG welding in pumps and valves
Automatic MIG welding has been adopted in various key areas within the manufacturing and repair of industrial valves and pumps. Automatic MIG welding has critical applications in multiple industries, such as oil and gas, naval, pulp and paper, petrochemical, cryogenics, desalination, water, and wastewater treatment. In these sectors, the precision and durability of compressors, pumps, and valves are essential to ensure reliable operation in demanding environments.
For example, cryogenic valves and cryogenic pumps, which require precise manufacturing to withstand extremely low temperatures, greatly benefit from automatic MIG welding. This technology ensures the integrity and reliability of welds in cryogenic applications, guaranteeing that valves and pumps function properly even under the most severe conditions.
Below, we highlight some of the most common applications.
Manufacture of pump housings
Pump casings must be robust enough to withstand high levels of pressure and corrosion, requiring extremely strong and defect-free welded joints. The centrifugal pump is a key component in many industrial processes, and its manufacturing demands maximum precision and durability to endure extreme operating conditions. Automatic MIG welding enables the precise joining of these casing components, ensuring their durability and performance even in the most challenging environments.
Furthermore, to ensure that each part fits perfectly and meets the highest quality standards, we combine automated welding with advanced machining processes. In this regard, accuracy in CNC machining is crucial to achieving components that comply with the stringent requirements of pump and valve manufacturers, ensuring optimal and long-lasting performance under extreme operating conditions.
Repair of industrial valves
Industrial valves, especially those operating in chemical or oil processing plants, such as butterfly valves and diaphragm valves, experience significant wear due to continuous exposure to corrosive fluids and extreme temperatures. Automatic MIG welding is used to repair these damaged valves, extending their service life and preventing the need for costly replacements.
Automatic MIG welding not only allows for the repair of surface damage but also restores the full functionality of critical components within each valve. Thanks to its precision and consistency, this process effectively rebuilds worn or corroded areas while maintaining the structural integrity of the valve and ensuring a tight seal. In applications where extreme conditions are constant, such as in the petrochemical industry and chemical plants, the ability to perform repairs using automatic MIG welding reduces the risk of failures and prevents costly operational downtime.
Manufacture of custom valves
Automatic MIG welding is particularly useful in the manufacturing of customized valves, where exact specifications are required to ensure optimal performance. Welding machines allow for precise adjustments during the process, ensuring that each valve meets the strict requirements of our clients.
Automatic MIG welding enables levels of precision and consistency that are difficult to achieve with manual techniques, making it especially beneficial in the production of customized valves. This technique ensures that welded joints are uniform and strong, minimizing the risk of failures during operation in demanding environments.
Additionally, as an automated process, MIG welding allows for detailed control of welding parameters, such as travel speed and temperature, adapting to the specific requirements of each valve design.
Manufacture of pump housings
Pump casings must be robust enough to withstand high levels of pressure and corrosion, requiring extremely strong and defect-free welded joints. The centrifugal pump is a key component in many industrial processes, and its manufacturing demands maximum precision and durability to endure extreme operating conditions. Automatic MIG welding enables the precise joining of these casing components, ensuring their durability and performance even in the most aggressive environments.
Furthermore, to ensure that each piece fits perfectly and meets the highest quality standards, we combine automated welding with advanced machining processes. In this regard, accuracy in CNC machining is crucial to achieving components that meet the stringent requirements of industrial pump and valve manufacturers, thus guaranteeing optimal and long-lasting performance under extreme operating conditions.
Repair of industrial
valves
Industrial valves, especially those operating in chemical or oil processing plants, such as butterfly valves and diaphragm valves, experience significant wear due to continuous exposure to corrosive fluids and extreme temperatures. Automatic MIG welding is used to repair these damaged valves, extending their service life and avoiding the need for costly replacements.
Automatic MIG welding not only allows for the repair of surface damage but also restores the full functionality of critical components within each valve. Thanks to its precision and consistency, this process effectively rebuilds worn or corroded areas while maintaining the structural integrity of the valve and ensuring a tight seal. In applications where extreme conditions are constant, such as in the petrochemical industry and chemical plants, the ability to perform repairs using automatic MIG welding reduces the risk of failures, preventing costly operational downtime.
Manufacture of custom valves
Automatic MIG welding is particularly useful in the manufacturing of customized valves, where exact specifications are required to ensure optimal performance. Welding machines allow for precise adjustments in the process, ensuring that each valve meets the strict requirements of customers.
Automatic MIG welding enables levels of precision and consistency that are difficult to achieve with manual techniques, making it especially beneficial in the production of customized valves. This technique ensures that welded joints are uniform and strong, minimizing the risk of failures during operation in demanding environments. Additionally, as an automated process, MIG welding allows for detailed control of welding parameters, such as travel speed and temperature, adapting to the specific needs of each valve design.
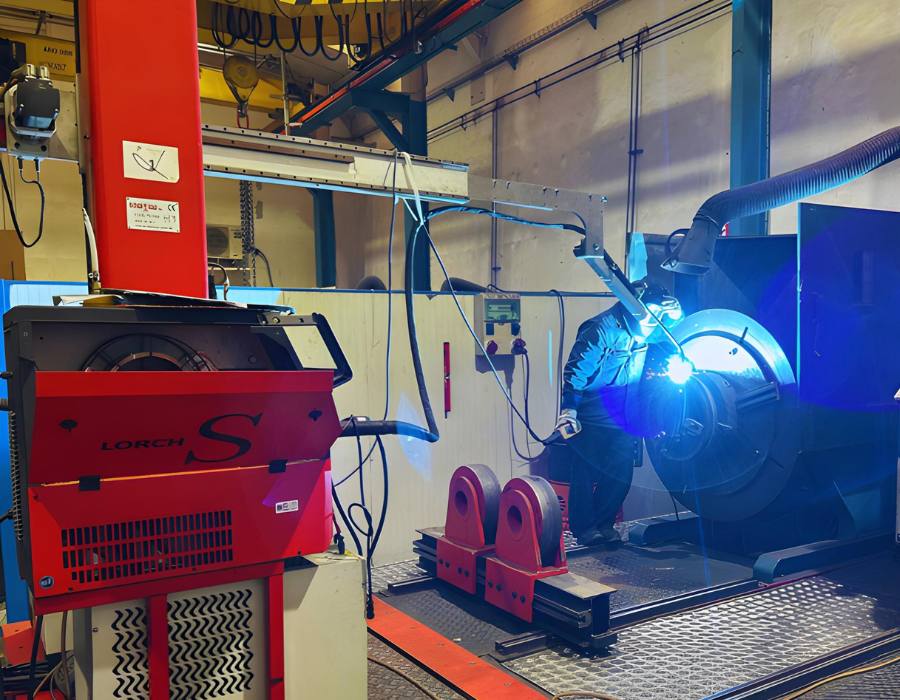
Innovations in automatic MIG welding
At Asimer Group, we strive to stay at the forefront of automatic welding technology by implementing innovations that enhance both the efficiency and quality of our processes. Some of the latest technologies include:
Automatic welding machine
The integration of state-of-the-art automatic welding machines has improved the repeatability and precision of complex welds. These machines are equipped with advanced vision systems and sensors, allowing them to adapt to the most intricate geometries of pumps and valves.
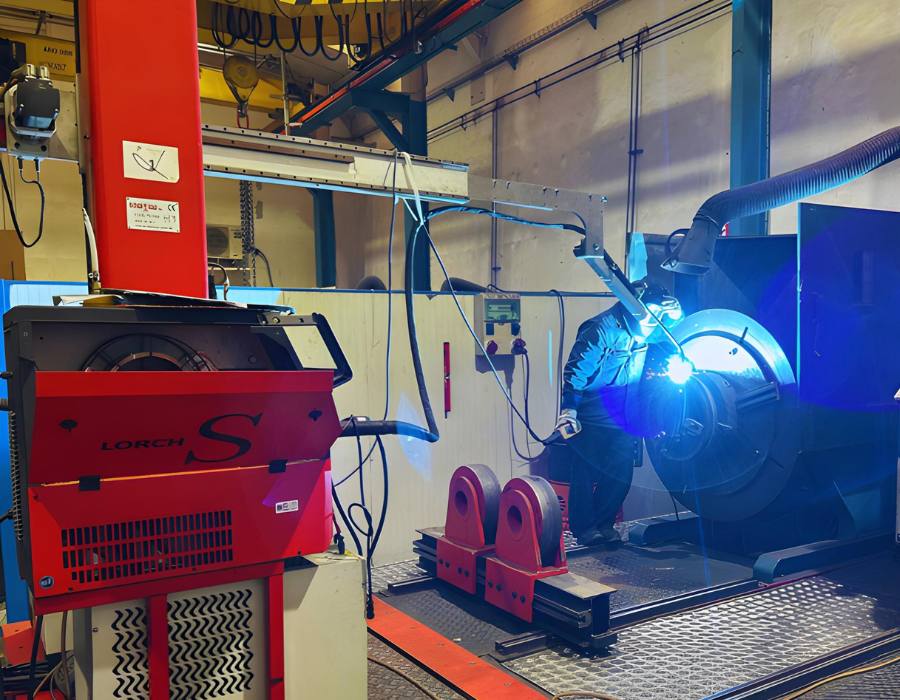
Real-time monitoring
At Asimer Group, we have incorporated real-time monitoring systems that automatically adjust welding parameters during the process. This ensures that any variations in the material or environmental conditions are corrected instantly, minimizing defects and guaranteeing superior quality in every component.
The shift towards Industry 4.0 is transforming all aspects of manufacturing, including automatic MIG welding. By integrating advanced technologies and intelligent systems, companies can enhance the precision and efficiency of their processes, aligning with the most innovative trends in CNC machining and beyond.
As we advance in the field of automatic welding, it is essential to explore and compare the differences between TIG and MIG welding to determine which best suits the specific manufacturing needs of pumps and valves. While automatic MIG welding offers numerous advantages, TIG welding also represents a cutting-edge solution in the manufacturing of industrial valves. This complementary technique can be ideal for applications that require greater precision in the final finish of components.
Sustainability and energy efficiency
In addition to improving productivity, automatic welding also offers environmental benefits. We have optimized our power sources and carefully selected shielding gases that reduce environmental impact, helping to lower the carbon footprint of our operations.
In the context of automatic MIG welding, energy efficiency in industrial valves is a crucial aspect that should not be overlooked. For pump and valve manufacturers, optimizing energy consumption in the manufacturing and operation of industrial components can lead to significant cost savings and a reduced environmental impact.
Overcoming the challenges of automatic Mig welding
- Complex parameter setting: Thanks to our advanced technology, we can precisely adjust the welding parameters according to the exact specifications of each project.
- Handling of intricate geometries: We use machines with advanced vision systems to weld in hard-to-reach areas.
- Integration into production processes: Our automatic welding systems are perfectly integrated with other stages of the manufacturing process, ensuring a smooth and efficient transition.
Automation as the key to the future
Automatic MIG welding is revolutionizing the industrial sector, marking a turning point in the manufacturing and repair of essential components such as pumps and valves. At Asimer Group, we not only adopt this technology but also optimize it to meet the demanding quality and performance standards our clients expect. The unmatched precision and continuous production capability offered by automated welding allow us to tackle complex industrial challenges, ensuring reliable and consistent results.
Furthermore, by integrating real-time monitoring systems and cutting-edge technology, we have minimized defects and maximized efficiency, resulting in more durable components and a significant reduction in operational costs. These advancements not only enhance productivity but also enable us to offer more sustainable and environmentally friendly solutions, reducing our carbon footprint.
In a highly competitive industrial market, welding automation is not just an advantage but a necessity to stay ahead. If your company is looking for solutions that combine precision, speed, and cost-effectiveness, Asimer Group is ready to be your strategic partner. Our commitment is to provide you with the best technical support and the highest quality results in every project. Contact us today and discover how we can take your manufacturing processes to the next level.