Welding for corrosive environments is a key aspect of the durability and performance of industrial equipment. At Asimer Group, specialists in machining and welding of industrial pumps and valves, we understand the importance of selecting the right welding method to ensure the durability and performance of equipment in demanding industries. Factors such as exposure to aggressive chemicals, extreme pressure, and temperature require a technical and precise approach in choosing the welding technique.
In this article, we will explore the most suitable types of welding for corrosive environments, their applications, and technological innovations in the manufacturing of industrial valves and pumps that optimize production and maintenance processes.
Key factors in selecting welding for corrosive environments
Selecting the right type of welding depends on several fundamental factors:
- Component Material: Stainless steel, nickel alloys, and titanium are commonly used in these environments due to their corrosion resistance.
- Operating Conditions: Temperature, pressure, and exposure to aggressive substances affect the choice of welding method.
- Durability and Sealing: Welded joints with high sealing capabilities are essential to prevent leaks in flow control valves and industrial pumps.
- Energy Efficiency: Processes that optimize energy consumption can reduce the carbon footprint in industrial pumps and valves.
Main types of welding for corrosive environments
TIG welding (Tungsten Inert Gas)
TIG welding stands out in corrosive environments for its precision and compatibility with highly corrosion-resistant materials. Its application is key in industries requiring clean, impurity-free welds, such as:
- High-precision machining processes for cryogenic components in industrial pumps and valves.
In cryogenic environments (extremely low temperatures), materials tend to become brittle. TIG welding allows for clean, defect-free joints, reducing the risk of fractures due to brittleness.
- Manufacturing of centrifugal pumps essential in the chemical and petroleum industries, where corrosion resistance is a priority.
These pumps transport corrosive fluids. TIG welding creates homogeneous, porosity-free joints, minimizing the possibility of chemical attacks on welded joints.
- Welding of axial flow check valves in the oil industry, where an effective barrier against highly aggressive fluids is needed.
In the petroleum industry, valves must withstand highly corrosive fluids and extreme pressures. TIG welding is used to manufacture and repair these valves, ensuring that the joints are airtight and corrosion-resistant.
- Integration of machining and welding in centrifugal pump manufacturing, ensuring joints are resistant to pressure and corrosion.
The combination of CNC machining and TIG welding ensures that parts fit precisely and that welded joints have optimal resistance to mechanical stress and corrosion.
- Repair and manufacturing of cryogenic valves in the oil and gas sector, ensuring maximum durability in systems subjected to extreme temperatures.
In cryogenic valves, poor welding can generate microcracks that allow leaks of liquefied gases at extremely low temperatures. TIG welding enables a dense, resistant, and defect-free joint, minimizing risks.
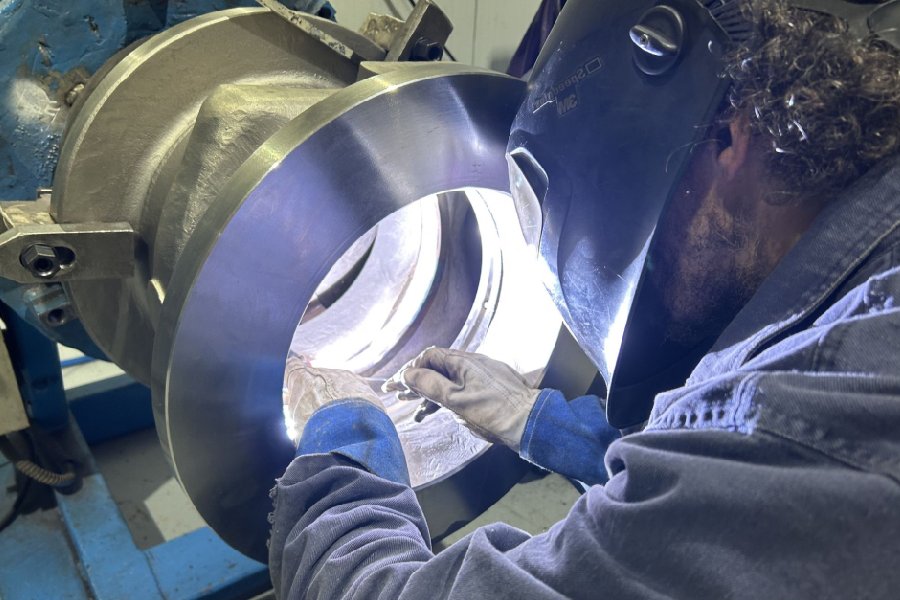
MIG welding (Metal inert gas) and automated MIG welding
MIG welding and its automated version (automated MIG welding) are widely used in industrial applications where speed and efficiency are required. Their advantages include:
- Higher deposition speed of material.
- Cost reduction in the machining of large-diameter valves.
- Use in Industry 4.0, where automation optimizes production times.
- Application in oil refining, where corrosion resistance is critical.
- Differences between TIG and MIG welding, key to selecting the best option based on material type and operating environment.
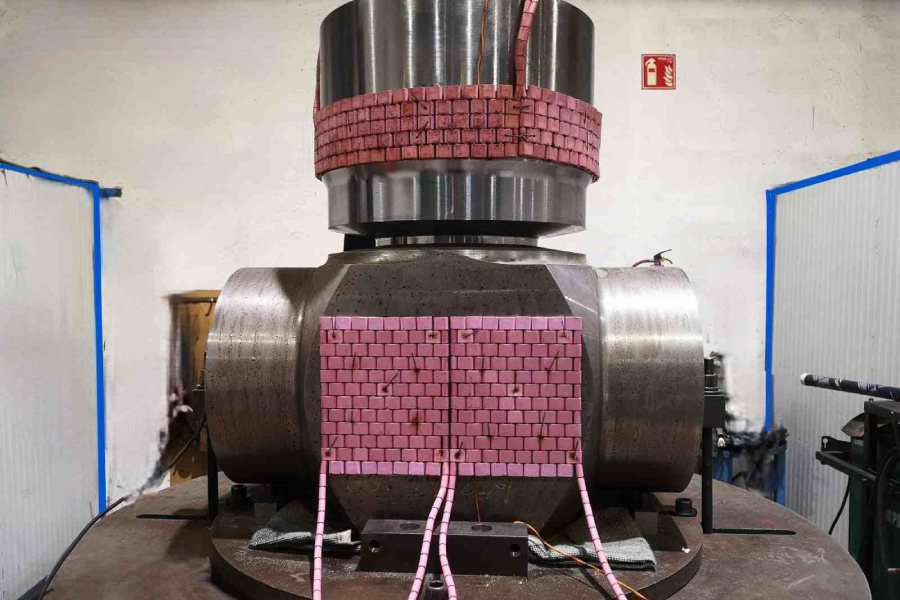
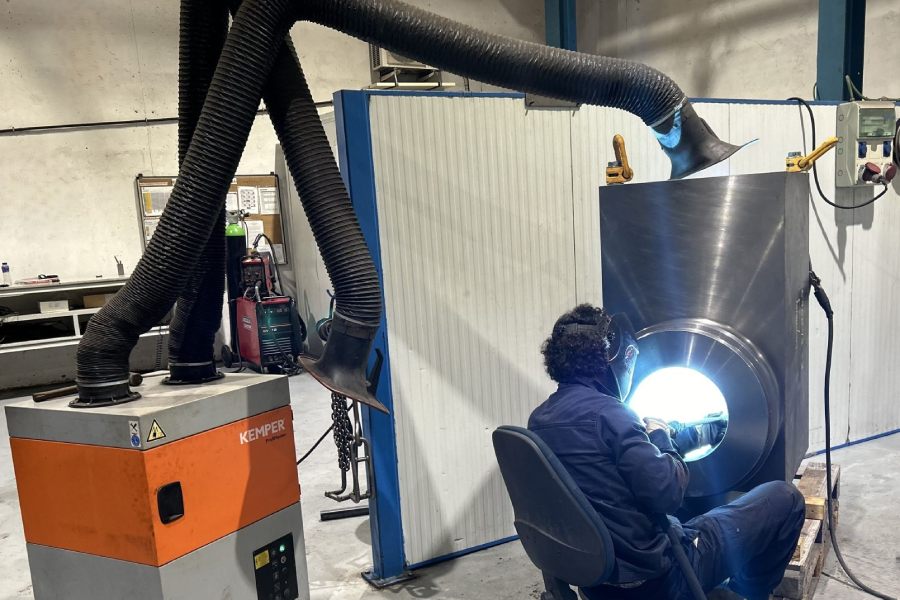
PTA welding (Plasma transferred arc)
PTA welding is an advanced process used in coatings and reinforcement of metal surfaces exposed to extreme wear and corrosive environments. Its ability to apply wear-resistant alloys with high precision makes it ideal for applications in industries requiring long-lasting components with superior mechanical resistance. It is commonly used in:
- Coating of large-diameter valves, protecting contact surfaces against wear and corrosion under high pressure and temperature conditions.
- Fittings in the oil and gas industry, where it is used for internal and external coatings that extend the lifespan of components exposed to aggressive fluids.
- Cryogenics applications, where PTA welding creates highly resistant surfaces against low temperatures and thermal impact.
- Manufacturing and maintenance of industrial valves, including butterfly valves and needle control valves, applying wear-resistant coatings on seats and components subject to constant friction.
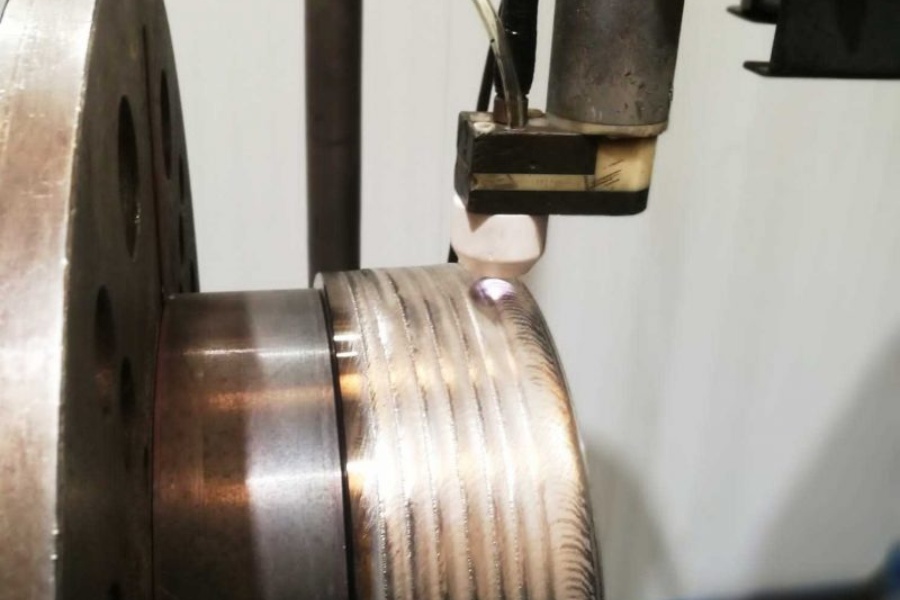
Common mistakes in welding for corrosive environments and how to avoid them
Welding in corrosive environments presents various challenges that can affect the quality and durability of joints. To ensure optimal results, it is essential to identify and prevent errors that reduce the structural resistance of welds. The most common problems and how to avoid them include:
- Incorrect material selection: Using inadequate alloys can accelerate corrosion and reduce component lifespan.
- Poor surface preparation: The presence of oxides or contaminants on the base material can affect welding adhesion.
- Inadequate welding technique: Each corrosive environment requires a specific method to prevent premature failures.
- Insufficient quality control: Without proper testing, defects that compromise mechanical resistance and sealing may go unnoticed.
At Asimer Group, we apply strict controls to ensure the highest quality in our welding for corrosive environments. We use advanced technologies such as non-destructive testing and metrology room inspections to guarantee that each joint meets the highest precision and durability standards.
Regulatory standards in welding for corrosive environments
To ensure quality and durability in welding for corrosive environments, it is essential to comply with international standards and certifications, including:
- ISO 3834: Defines quality requirements for fusion welding of metallic materials.
- ASME Section IX: Establishes welder qualification codes and welding procedures for industrial applications.
- API 1104: Used in the oil and gas industry for pipeline welding inspection and certification.
Factors affecting the lifespan of welding in corrosive environments
In addition to selecting the appropriate welding process, various factors can influence the longevity of the welded joint in aggressive environments:
- Extreme Temperature: Heat can alter the composition of the base metal and affect the strength of the weld.
- Pressure and Mechanical Load: High-pressure conditions can generate stress in the weld, causing cracks over time.
- Exposure to Aggressive Chemicals: Acids, salts, and corrosive agents can accelerate metal deterioration if the weld is not properly executed.
- Welding Defects: Porosity, cracks, or inclusions can compromise the integrity of the welded joint.
To minimize these risks, at Asimer Group, we apply high-precision machining processes and quality control at every stage of the project.
Practical cases and industrial applications
Welding for corrosive environments is widely used in multiple industrial sectors, where resistance to degradation is key:
- Oil & Gas Industry: Welding in hydrocarbon transport pipelines that withstand extreme pressure conditions and aggressive chemicals.
- Cryogenics: Applications in cryogenic valves that operate at extremely low temperatures without compromising their sealing.
- Petrochemical: Welding of storage tanks and processing equipment exposed to highly corrosive agents.
- Desalination: Pump and valve components that work with seawater, minimizing corrosion in saline environments.
- Water Treatment: Filtration and pumping systems where the chemical and mechanical resistance of welds is essential.
In each of these cases, Asimer Group provides tailored solutions using the most advanced welding and machining technologies.
Costs and efficiency in welding selection
Selecting the right type of welding not only impacts the durability of components but also operational efficiency and production costs. Below are some key comparisons:
- TIG Welding: Higher precision and corrosion resistance but requires more time and skilled labor.
- MIG Welding: Fast and efficient for mass production but less precise for delicate materials.
- PTA Welding: High wear resistance and excellent adhesion, ideal for highly corrosive environments.
At Asimer Group, we analyze each project and advise our clients to select the best option based on cost, application, and process efficiency.
Technological innovations applied to welding in corrosive environments
To ensure welding quality in corrosive environments, it is essential to employ advanced technologies that improve surface preparation, machining accuracy, and the quality control of welded joints. Some key innovations include:
- Trevisan Machining Center: Its high precision in CNC machining allows for surface preparation with minimal tolerances, ensuring welded joints are homogeneous and free of imperfections, thereby improving corrosion resistance.
- Advanced Measurement Instruments in the Metrology Room: Dimensional inspection of parts before and after welding ensures that there are no deviations in geometry that could affect the strength of the joint under extreme conditions.
- Chip Removal Machining: Used for manufacturing components of centrifugal pumps and industrial valves, ensuring that welding surfaces have the proper roughness for better adherence of the filler material.
- Applications in Industrial Valves: In certain valves, such as diaphragm valves and butterfly valves, specialized welding is used to reinforce areas subject to wear and corrosion, ensuring their performance in aggressive environments. Additionally, proper maintenance, including inspections with non-destructive testing, such as liquid penetrants for detecting surface defects, helps identify failures before compromising functionality. For ferromagnetic materials, this method can be complemented with magnetic particle testing or ultrasound to assess internal defects.
Competitive advantages of asimer group in welding for corrosive environments
At Asimer Group, we stand out for our ability to offer welding solutions tailored to the most demanding industrial environments. Our competitive advantages include:
- Experience and Specialization: We have a highly qualified team in TIG, MIG, and PTA welding, with a specific focus on high-demand applications.
- Advanced Technology: We use state-of-the-art equipment in CNC machining and automated welding, ensuring high-quality and precise joints.
- Rigorous Quality Control: We apply various types of non-destructive testing and metrological verifications in our metrology room to ensure that each weld meets the highest standards.
- Adaptability to Multiple Sectors: We serve industries such as oil and gas, cryogenics, petrochemicals, and water treatment, providing tailored solutions for each application.
- Commitment to Energy Efficiency: We implement optimized processes that contribute to reducing the carbon footprint in industrial pumps and valves.
Specialized solutions from Asimer Group in welding for corrosive environments
At Asimer Group, we understand that choosing the right welding method is key to ensuring the longevity and performance of industrial pumps and valves in highly corrosive environments. That is why we apply advanced technologies and a comprehensive approach to each project, ensuring welded joints with maximum resistance.
Our expertise in TIG, MIG, and PTA welding, combined with non-destructive testing and precision CNC machining, allows us to offer solutions tailored to sectors such as oil and gas, cryogenics, petrochemicals, and water treatment. We implement optimized processes to minimize defects, improve mechanical resistance, and extend the lifespan of each component.
Why choose Asimer Group?
- Rigorous Quality Control: We conduct advanced inspections using high-precision measurement instruments, such as the measuring arm in our metrology room.
- High-Performance Welding: Ensuring joints with maximum sealing and corrosion resistance.
- Cost Optimization Strategies: Designing solutions that balance durability and economic efficiency, reducing maintenance and repair costs.
If you are looking for a strategic partner to optimize your welding processes in corrosive environments, contact us and discover how our solutions can improve the quality and reliability of your industrial projects.
Frequently asked questions (FAQs) about welding for corrosive environments
What is the best welding for corrosive environments?
The choice depends on the type of material, exposure to corrosive agents, and operating conditions. Generally, TIG welding and PTA welding offer the highest corrosion resistance.
How can corrosion in welding be prevented?
The use of appropriate alloys, proper surface preparation, and the application of advanced techniques such as CNC machining help minimize corrosion.
Which industries require corrosion-resistant welding?
Industries such as oil and gas, petrochemicals, cryogenics, water treatment, and desalination require welding solutions that withstand aggressive conditions.
How does Asimer Group ensure quality in welding for corrosive environments?
We apply non-destructive testing, metrological control, and high-precision CNC machining processes, ensuring durable and efficient welded joints.
How can I request a specialized welding solution from Asimer Group?
You can contact us directly, and our technical team will assist you in finding the best solution for your needs.