High-accuracy machining for cryogenic applications plays a crucial role in the manufacturing of components that operate under extreme conditions. Cryogenic applications, where temperatures can drop below -150°C, demand advanced engineering solutions to ensure the durability and performance of industrial pumps and valves. In this article, we explore the benefits and key technologies that enable manufacturers to meet the stringent requirements of this challenging sector.
Importance of high-accuracy machining for cryogenic applications
Ensuring performance under extreme conditions
The performance of industrial pumps and valves in cryogenic applications depends directly on machining quality. Components must be manufactured with accuracy machining that ensures a perfect fit, preventing leaks or operational failures. For instance, a centrifugal pump used in liquefied natural gas (LNG) plants must maintain stability even under extreme stresses.
The use of fittings in the Oil and Gas industry is essential to ensure airtightness in systems where temperature and pressure conditions are critical. These components, such as threaded or welded connections, enable a hermetic seal even in demanding conditions. When combined with precise machining and advanced techniques, they ensure maximum durability and system performance. Additionally, certification in non-destructive testing guarantees that each component meets the highest standards of quality and reliability.
Wear and corrosion resistance
CNC machining plays a key role in enhancing the wear and corrosion resistance of materials, which are essential factors in cryogenic applications. This process is crucial in the manufacturing of critical components such as valves, where machining precision and material selection determine long-term performance.
Axial flow check valves designed for cryogenic applications require high-precision machining to ensure a hermetic seal. Advanced manufacturing processes help minimize pressure drop and optimize performance in systems where flow control is critical.
Similarly, butterfly valves used in handling aggressive or cryogenic fluids rely on uniform machining to guarantee the mechanical resistance of their materials and precise flow control. Manufacturing through chip removal machining processes ensures exact tolerances and greater durability in demanding industrial environments.
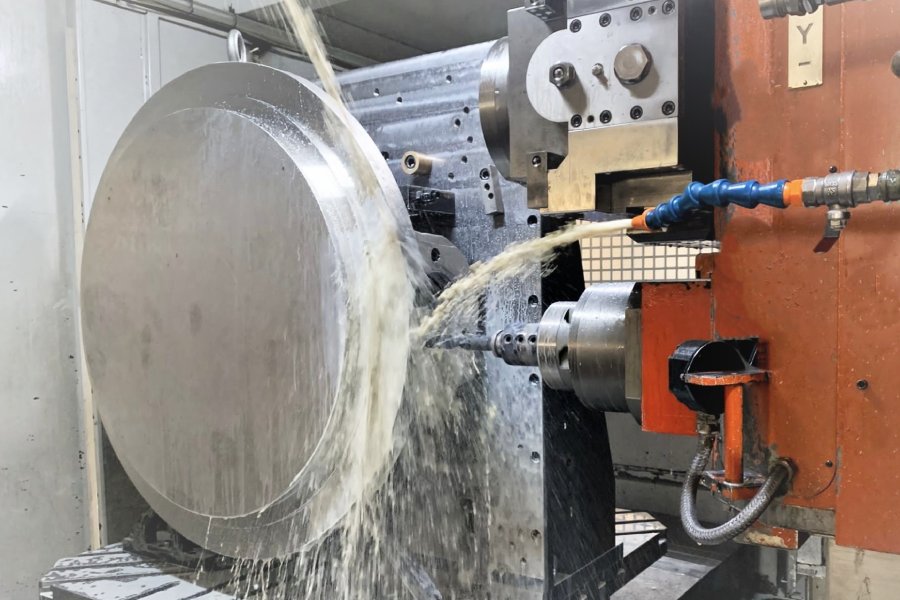
Advanced technologies for accuracy machining in cryogenics
Detailed applications of CNC machining
CNC technology is essential for the manufacturing of cryogenic components. This technology enables:
- Working with tolerances below 0.01 mm.
- Producing complex geometries for industrial pumps and valves.
- Ensuring repeatability in large-scale manufacturing.
A notable example is the machining of impellers for cryogenic pumps, where every detail affects flow and system energy efficiency. These components require a combination of machining precision and suitable material selection, such as Inconel® and Hastelloy®, to ensure long-term performance in extreme temperatures. Furthermore, the implementation of non-destructive testing, such as liquid penetrant and magnetic particle inspections, allows for the detection of microdefects that could compromise the component’s sealing and durability.
To ensure precision in machined parts, the use of control tools such as the measuring arm is essential. This technology enables real-time dimensional inspections, ensuring that each component meets the required specifications for cryogenic applications.
CNC machining tools and specialized materials
Using CNC machining tools coated with wear-resistant materials, such as tungsten carbide, is fundamental in CNC machining of parts for cryogenic applications. These coatings enhance the lifespan of cutting tools and maintain tight tolerances even under extreme working conditions. Additionally, working with advanced alloys like Hastelloy® or Inconel®, highly resistant to corrosion and low temperatures, is essential for manufacturing cryogenic pumps and valves used in the Oil and Gas and petrochemical industries.
The implementation of advanced equipment like the Trevisan machining center allows for machining complex components, such as large-dimension valves, optimizing both precision and dimensional stability. Thanks to its capability to machine in multiple axes and perform turning and milling operations in a single setup, this system reduces production times and improves surface finish quality. This is crucial in manufacturing components for cryogenic applications. This type of machinery, integrated within Industry 4.0, optimizes processes through real-time monitoring systems, smart sensors, and advanced automation, allowing dynamic adjustment of cutting parameters and minimizing material waste. These technologies ensure efficient and repeatable machining, guaranteeing quality in every batch of critical components for industrial pumps and valves in cryogenic environments while optimizing costs without compromising precision or product quality.
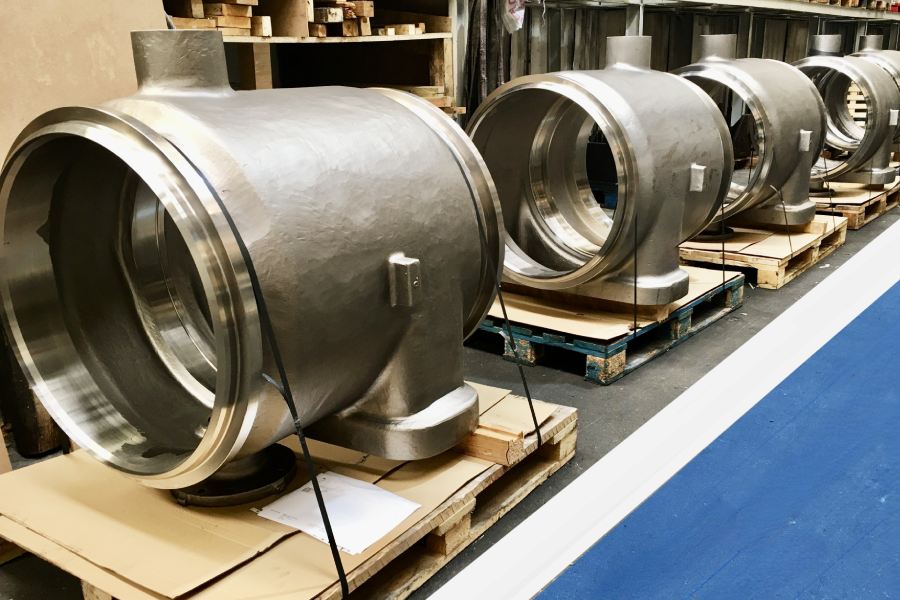
Practical cases: Success in cryogenic projects
High-precision machining plays a key role in the manufacturing of components for cryogenic applications, where extreme temperatures and sealing requirements demand advanced solutions. Below, we present two cases in which Asimer Group has applied its expertise in high-precision machining to ensure the performance and durability of industrial equipment in cryogenic environments.
Case 1: Components for cryogenic pumps in LNG
Asimer Group collaborated with a client in the liquefied natural gas sector on a high-precision impeller project. Thanks to our CNC technology, we achieved optimal tolerances that ensured system efficiency under -160°C conditions. This project also stood out for implementing liquid penetrant testing to detect minimal defects and guarantee final quality.
Case 2: Cryogenic valves for the chemical industry
An international client required needle control valves capable of operating in chemical plants. Asimer Group machined the components using corrosion-resistant materials, ensuring reliable performance at temperatures of -200°C.
In both cases, the use of advanced measuring instruments and rigorous control in our metrology lab ensured that each component met the most demanding specifications.
Advantages of accuracy machining in cryogenic pumps and valves
- Enhanced operational efficiency: Precision machining optimizes the geometry of components, improving aerodynamics and hydrodynamics in cryogenic pumps and reducing friction in valves for liquefied gases. This translates into lower energy losses and higher performance in industrial systems exposed to extreme temperatures.
- Reduced maintenance costs: In cryogenic applications, selecting low-temperature-resistant alloys and specific heat treatments minimizes material embrittlement and reduces friction and wear. This extends component lifespan and decreases the need for corrective maintenance in LNG and liquid nitrogen systems.
- Compliance with international standards: Precision machining and the application of non-destructive testing ensure that components meet specialized regulations for cryogenic equipment, such as those established by the LNG Technical Standards Commission and ASME for cryogenic applications. These regulations are essential in sectors like Oil and Gas, petrochemicals, and liquefied gas storage.
Integration of welding in accuracy machining for cryogenic projects
To ensure strong joints in cryogenic components, advanced welding techniques are used. TIG welding and MIG welding allow for high-quality weld beads with great resistance to low temperatures. In particular, automatic MIG welding offers excellent productivity in cryogenic valve manufacturing, ensuring homogeneous and fracture-resistant joints.
Additionally, PTA welding is employed for components requiring higher wear and corrosion resistance. The differences between TIG and MIG welding are key to determining the best option for each application, thus optimizing system efficiency and durability.
Why choose Asimer Group for cryogenic projects
At Asimer Group, we have the experience and technology required to undertake high-precision machining projects in the cryogenic field, as well as in other sectors such as naval, pulp and paper, desalination, and water and wastewater treatment.
We have collaborated on multiple projects where machining precision has reduced leaks in cryogenic valves by 30%, optimizing operational efficiency and extending component lifespan.
Our services include:
- Custom manufacturing of components based on blueprints or samples, including parts specifically designed to withstand extreme cryogenic temperatures.
- Use of advanced CNC technology for extreme tolerances.
- Experience in national and international projects.
If you are looking for a partner with proven expertise, Asimer Group has the solution you need. Contact our team today and discover how our specialization in precision machining for low-temperature environments can optimize the performance and durability of your industrial equipment. Get in touch and find out how we can enhance the manufacturing of your industrial pumps and valves while also contributing to reducing the carbon footprint.
Frequently asked questions about accuracy machining in cryogenics
Why is CNC machining crucial in cryogenic pumps?
CNC machining ensures extreme tolerances and allows for the manufacturing of components with precise fits, which are essential for preventing leaks and ensuring efficiency in cryogenic systems. Additionally:
✔ Enables working with advanced alloys such as Inconel® and Hastelloy®, which resist corrosion and temperatures as low as -200°C.
✔ Compensates for the thermal contraction of materials in cold environments, ensuring a precise fit.
✔ Optimizes energy efficiency by improving fluid flow in liquefied natural gas (LNG) cryogenic pumps.
What materials are used in cryogenic valves and pumps?
In cryogenic applications, materials must maintain their mechanical strength at extremely low temperatures. The most commonly used materials include:
✔ Inconel® and Hastelloy®: Nickel-based alloys with high resistance to corrosion and thermal fluctuations.
✔ Cryogenic stainless steel (304, 316, 316L): Commonly used in valves and pipelines for liquefied gases.
✔ Cryogenic carbon steels (ASTM A352 Grades LC1, LC2, LC3): Used in cryogenic valves within the Oil & Gas industry.
✔ Cryogenic bronze: Applied in bearings and specific components, with low zinc content to prevent embrittlement.
What advanced technologies are used in cryogenic machining?
To ensure precision and efficiency in machining parts for cryogenic applications, the following technologies are used:
✔ Trevisan machining centers: Ideal for manufacturing valves and pump casings with high dimensional stability.
✔ Tungsten carbide tools with advanced coatings (TiAlN, AlCrN): Enhance durability and reduce wear on difficult-to-machine materials.
✔ Real-time automation and Industry 4.0: Smart sensors optimize cutting parameters and minimize material waste.
✔ Cryogenic cooling with CO₂ or liquid N₂: Extends tool life and prevents overheating during machining.
✔ Latest-generation CAD/CAM software: Enables machining of complex geometries with tolerances below 0.01 mm.
How is the quality of machined components for cryogenic applications ensured?
To guarantee the reliability of components in cryogenic environments, rigorous quality controls are applied:
✔ Non-destructive testing (NDT):
- Liquid Penetrant Testing (PT): Detects surface cracks in welds and machined parts.
- Magnetic Particle Testing (MT): Useful for detecting internal defects in ferromagnetic materials.
- Ultrasonic Testing (UT): Ideal for inspecting thick materials without compromising integrity.
✔ Dimensional control using measurement arms:
Ensures that critical tolerances are met with micrometric precision.
✔ Leak testing:
- Helium Leak Test: Detects microleaks in valves and liquefied gas systems.
- Hydrostatic Test: Verifies mechanical strength and airtightness under high-pressure environments.
✔ Charpy Impact Testing:
Determines material resistance to embrittlement at sub-zero temperatures.
By leveraging these technologies, Asimer Group ensures the highest precision and durability in cryogenic applications.
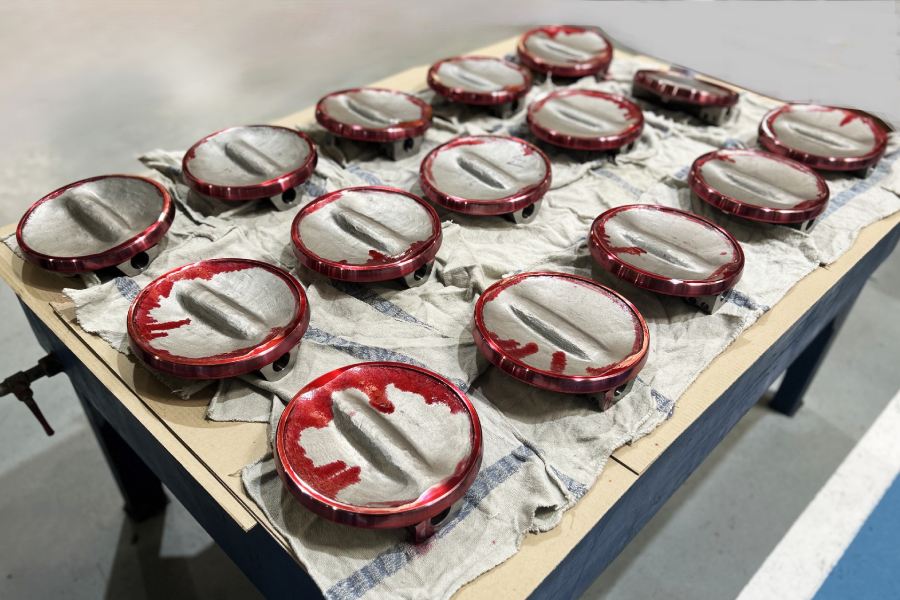
What are the benefits of CNC machining in the cryogenic industry?
Manufacturing components through CNC machining for cryogenic applications offers multiple advantages:
✔ High precision and exact tolerances: Essential for cryogenic pumps and valves, where minimal deviations can lead to operational failures.
✔ Extended component lifespan: Achieved through optimized materials and state-of-the-art machining processes.
✔ Reduced risk of leaks and operational failures: Ensuring a hermetic seal and optimal mechanical resistance.
✔ Compliance with international standards:
- ISO 21013-2: Applies to safety valves in cryogenic storage systems.
- ASME B31.3: Regulates cryogenic piping and its manufacturing.
- API 600 and API 602: Establish design and testing standards for cryogenic industrial valves.