Failure diagnosis in centrifugal pumps is a fundamental step to ensure the performance and efficiency of these essential industrial devices. From water treatment applications to sectors such as cryogenics, oil and gas, petrochemicals, desalination, pulp and paper, and naval industries, these pumps face demanding operational conditions that may lead to issues such as cavitation, abnormal vibrations, or failures in centrifugal pump components. A combination of advanced technologies, such as CNC machining, and repair techniques using TIG welding or MIG welding is key to maintaining the optimal functionality of these pumps.
This article delves into the most common problems affecting centrifugal pumps, how to diagnose their causes, and specialized solutions that can be implemented to ensure their functionality in critical industrial environments.
Common problems in centrifugal pump operation
Failures in industrial pumps can result in costly downtime and jeopardize key processes. The most frequent issues include:
Cavitation
Cavitation, a phenomenon that occurs when the fluid pressure drops below its vapor point, causes bubble formation that implodes, leading to severe damage to impellers and casings. This issue can compromise energy efficiency and reduce hydraulic performance, especially in sectors like desalination and pulp and paper.
Solution:
- Repair damage using CNC machining to ensure exact tolerances.
- Apply protective coatings through automatic MIG welding to enhance wear resistance.
Wear and corrosion
Abrasive and corrosive fluids in sectors like petroleum refining and cryogenic applications erode internal components, reducing pump sealing and increasing the risk of failure.
Solution:
- Use corrosion-resistant materials applied with CNC machining tools.
- Apply specialized coatings using TIG welding to restore damaged surfaces.
Vibrations and imbalances
Abnormal vibrations are often caused by impeller imbalances, worn bearings, or misalignments in shafts. These conditions negatively affect operational stability and may damage other critical components.
Solution:
- Use measuring instruments, such as a measurement arm, to identify misalignments.
- Perform dynamic balancing and shaft repairs using chip-removal machining.
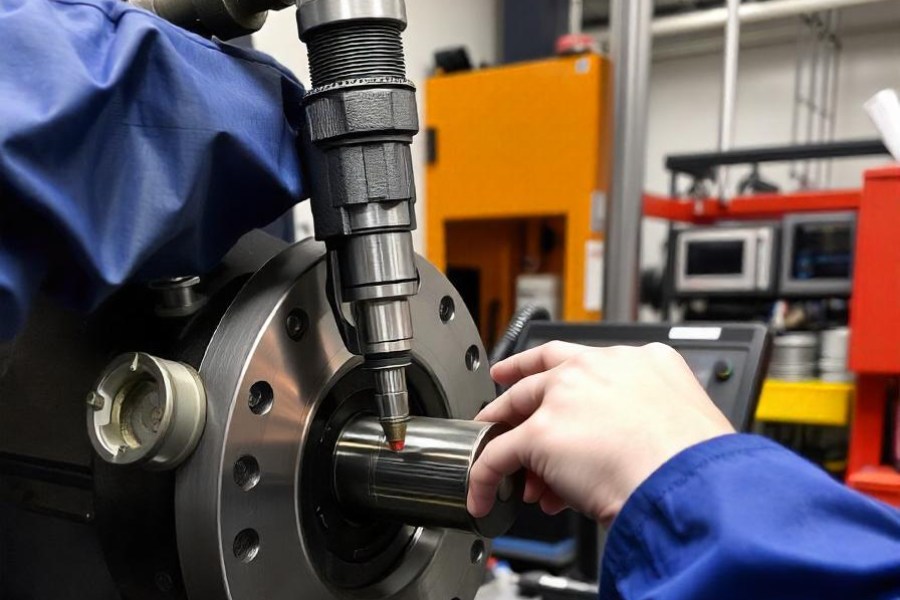
Precise diagnosis: The first step toward centrifugal pump repair
Effectively addressing problems requires detailed diagnostics using advanced tools and precise methodologies:
Visual inspection and non-destructive testing
Diagnostics begin with a visual inspection to identify visible cracks, wear, or residue buildup. Techniques like liquid penetrants and non-destructive testing are crucial to detect structural damage without compromising component integrity.
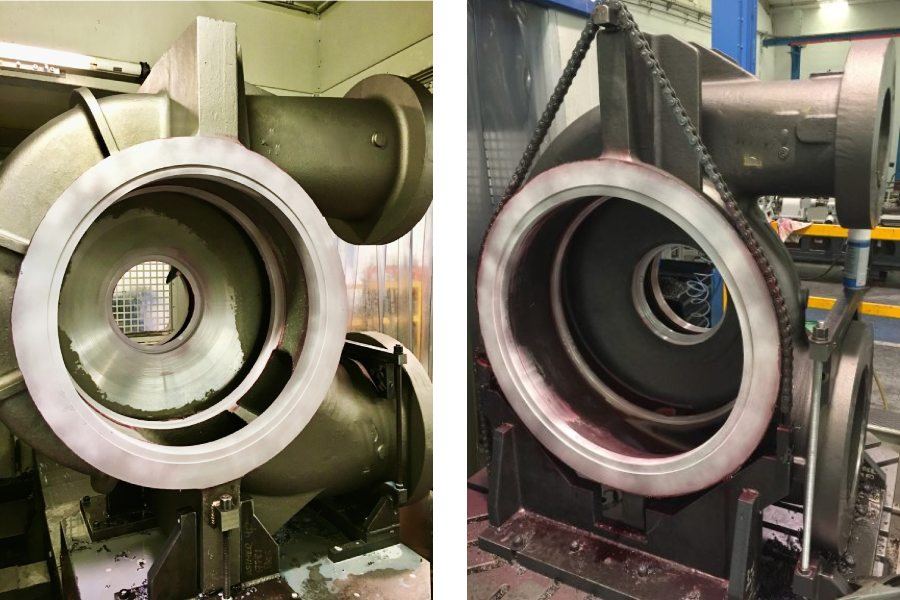
Vibration analysis and measuring instruments
Using sensors and measuring instruments helps identify issues such as impeller imbalances or damaged bearings. This analysis prevents major failures before they become critical problems.
Metrology room and CNC technology
Accurate measurement of components in a metrology room, combined with CNC technology, ensures repairs and replacements are precise and reliable, minimizing the risk of recurring failures.
Advanced repair solutions for centrifugal pumps using machining and welding
Once the problem is identified, the most effective solutions involve a combination of CNC machining techniques and specialized welding:
Repairing impellers and casings
CNC machining is ideal for restoring or manufacturing critical components such as impellers and casings, ensuring exact tolerances and perfect fits. In sectors like oil and gas, where fittings demand extreme precision, these solutions are indispensable.
TIG vs. MIG welding
Choosing between TIG and MIG welding depends on the specific project requirements. While TIG welding offers precision for thin materials and complex applications, MIG welding enables quick repairs on larger parts, such as those used in machining large-dimension valves.
Trevisan machining center: innovation in manufacturing
The Trevisan machining center excels in producing large components with high precision. This equipment is essential for demanding sectors like petrochemicals and desalination, where parts must withstand high pressures and extreme conditions.
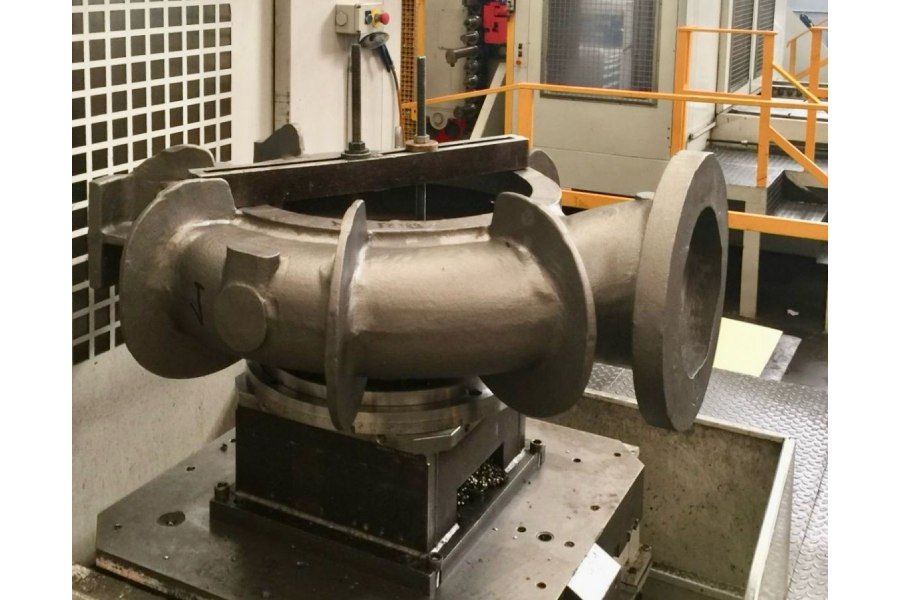
Engineering solutions for centrifugal pump maintenance in industry 4.0
The adoption of advanced technologies, such as CNC technology and process digitization in Industry 4.0, is transforming centrifugal pump repair and maintenance. Engineering solutions allow for:
- Optimizing the design and manufacture of critical components.
- Implementing simulations and digital modeling to predict potential failures.
- Improving energy efficiency by reducing consumption and enhancing performance.
Key sectors: Industrial applications of centrifugal pumps
The industrial applications of centrifugal pumps are essential in various sectors:
- Water Treatment and Desalination: Efficient handling of corrosive fluids.
- Cryogenics and Petrochemicals: Safe transport of extreme fluids.
- Oil and Gas: Critical processes requiring precision in fittings and components.
- Naval and Pulp and Paper: High-demand operations in variable environments.
Preventing centrifugal pump failures through predictive maintenance
Predictive maintenance anticipates issues and extends pump service life. Best practices include:
- Periodic inspections using methods like liquid penetrants.
- Advanced tools in a metrology room to evaluate tolerances.
- Preventive replacement of components via CNC machining.
Conclusion
Failure diagnosis in centrifugal pumps and implementing specialized solutions are crucial to ensuring their performance and durability. From advanced technologies such as CNC machining to precise TIG and MIG welding techniques, each solution is designed to meet the demands of critical sectors like petroleum refining, cryogenics, and naval industries.
At Asimer Group, we provide customized repair and maintenance services backed by state-of-the-art tools and a team of engineering experts. If you want to maximize efficiency and extend the service life of your pumps, contact us today. We’re ready to help!