The machining of large-dimension valves is a critical specialty in various industries that require the handling of fluids and gases under extreme pressure and temperature conditions. At Asimer Group, we offer customized solutions for sectors such as petrochemical, marine, energy, and water treatment, ensuring the precision, durability, and safety of the valve projects we undertake. Our approach includes the use of advanced technologies such as CNC machining, vertical lathes, and specialized welding, supported by a highly trained team and a strong commitment to quality.
How do we optimize large-size valve machining for demanding industrial sectors?
At Asimer Group, we approach the machining of large-size valves with a comprehensive strategy that combines precision, adaptability, and technical expertise. We understand that each sector—from naval and petrochemical to water treatment and cryogenics—demands strict standards in terms of tolerances, materials, and surface finishes. That’s why we tailor each project to technical drawings or samples, applying state-of-the-art technologies and certified processes.
Our ability to machine large-format valves is supported by a specialized fleet of machinery, advanced CAD/CAM solutions, and a skilled technical team experienced in complex, high-value components. This approach allows us to reduce cycle times, minimize margin of error, and ensure maximum operational reliability of each valve in its intended environment.
Whether it’s a small batch or a unique part, we deliver results that meet the most demanding technical requirements, always adhering to the specific regulations of each industry.
What is the machining of large-dimension valves?
Machining is the process of manufacturing or modifying parts by controlled material removal. When it comes to large-dimension valves, this process involves working with components that can weigh up to 10 tons and have complex structures. At Asimer Group, we use specialized machines like vertical lathes and CNC milling machines that allow us to machine industrial-sized valves with minimal tolerances, ensuring a high degree of precision and finish.
Large-dimension valves are critical for controlling the flow of liquids or gases in large-scale industrial infrastructures. This includes applications in pipelines, petrochemical plants, ships, and power plants. For these valves to function properly in hostile environments, it is essential that their components are perfectly aligned and made from highly resistant materials.
The technology we use, including advanced machining centers, is key to achieving a high level of precision in the machining of these valves. Discover more about how CNC machining is at the epicenter of Asimer Group.
Types of large-dimension valves
There are different types of industrial valves that may require large-dimension machining, each with a specific function:
- Gate valves:
Used to stop or allow the passage of a fluid. They are common in applications where complete shutoff is required.
- Ball valves:
Ideal for controlling the flow of fluids in systems that require quick and airtight sealing.
Used to regulate the flow of a fluid, especially in applications where quick installation and lower cost are required. Learn more about the operation and maintenance of butterfly valves to understand how they are applied in large industries.
- Check valves:
Allow flow in only one direction, preventing backflow of the fluid.
Used in applications where a tight seal is important without contact with the fluids.
- Needle control valves:
Designed to provide precise flow regulation in high-pressure systems.
Each of these valve types can be manufactured in large-dimension versions, which requires a specialized machining process to ensure their proper functionality.
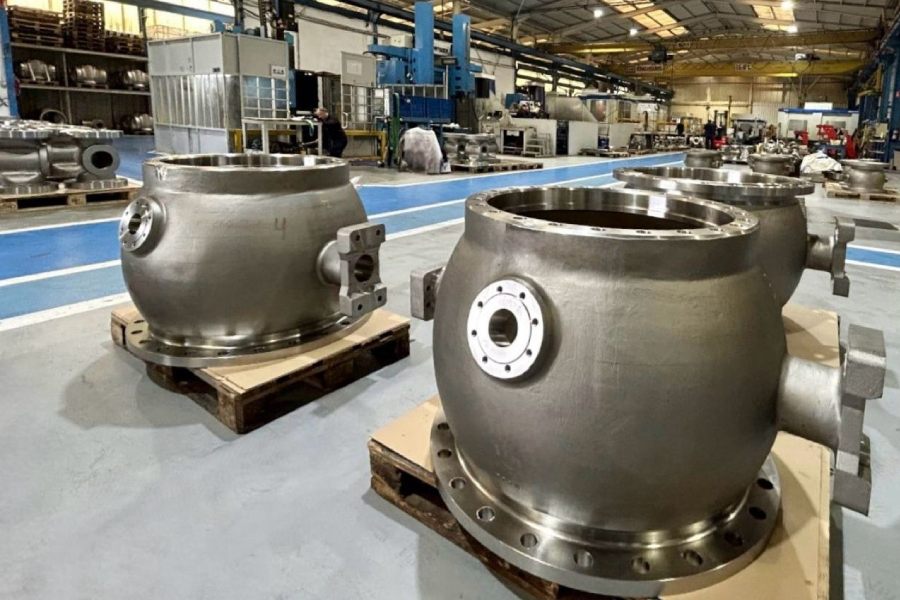
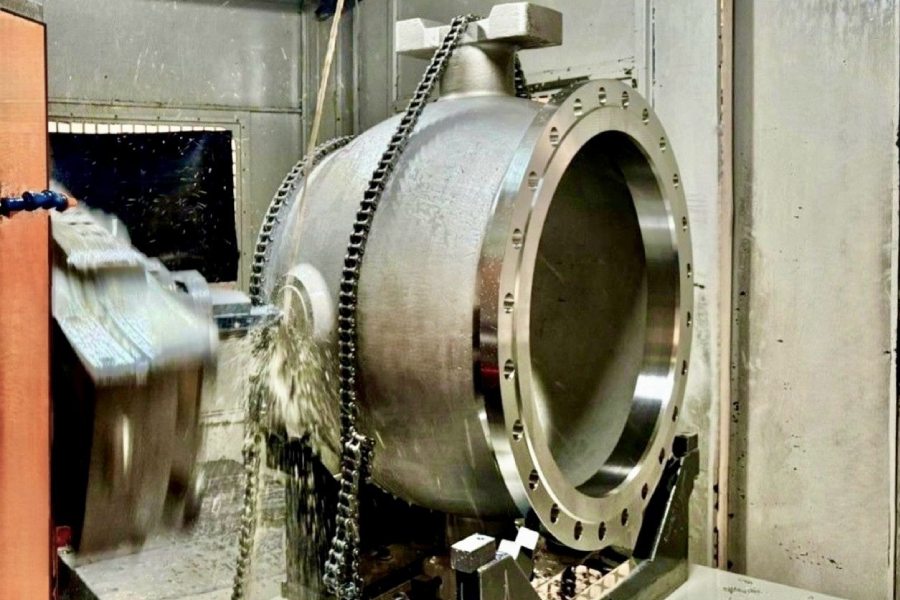
The importance of machining large-dimension valves
The machining of large-dimension valves is essential to ensure that these critical parts meet strict safety and performance requirements in industrial environments. Errors in machining can cause leaks, system failures, and, in the worst cases, serious industrial accidents. Therefore, it is vital that these valves are machined with precision to withstand the extreme conditions they will encounter.
At Asimer Group, our engineering solutions are designed to address these challenges, ensuring the precision and reliability of valves even in the most demanding environments.
If you are interested in learning more about how we achieve accuracy in CNC machining, check out our case studies.
Furthermore, these valves are often exposed to factors such as corrosion, abrasion, and temperature fluctuations, which require high-quality machining to increase their service life. Technological innovations in the manufacturing of industrial valves allow us to adapt to these challenges and continue offering effective solutions.
Industrial applications of large-dimension valves
At Asimer Group, we are committed to providing specific solutions tailored to the needs of each sector.
The main markets requiring large valves include:
- Petrochemical industry:
Large-dimension valves regulate the flow of gases and liquids under high-pressure and temperature conditions, handling potentially hazardous substances. Airtight sealing and corrosion resistance are essential.
- Naval industry:
On ships, valves control propulsion and cooling systems. These valves require constant maintenance due to their exposure to corrosive marine environments.
- Cryogenic and oil and gas applications:
In the context of large-dimension valve machining, it is crucial to mention the importance of cryogenics in certain industrial applications, where cryogenic valves must operate at extremely low temperatures while maintaining functionality without compromising safety.
In sectors like oil and gas, both valves and cryogenic pumps are exposed to extreme pressure and temperature conditions, where airtight sealing and corrosion resistance play a vital role. This is where the advanced technology and customized processes we offer at Asimer Group ensure that our solutions are not only precise but also adaptable to the most demanding industry requirements.
In water treatment plants, valves regulate the flow of water and other liquids through complex systems. Large valves ensure that distribution and filtration processes run smoothly.
- Energy sector:
Valves control the flow of steam, gases, and other critical fluids in power plants, where systems operate at extremely high temperatures and pressures. The reliability of these valves is crucial to avoid operational failures, which you can learn more about in our article on energy efficiency in industrial valves.
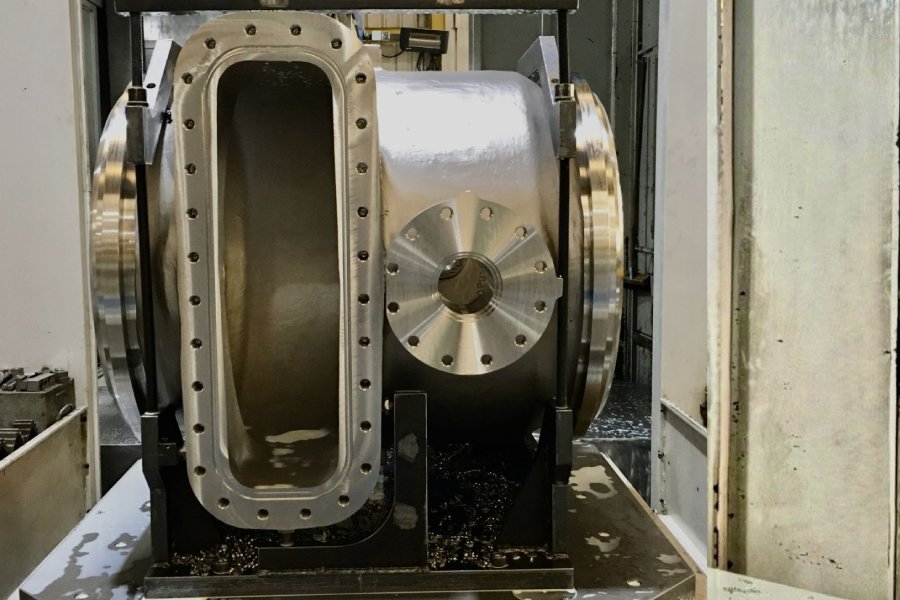
Challenges in machining large-dimension valves
Machining large-dimension valves presents several technical challenges, especially when it comes to achieving high levels of precision and quality. Some of the main challenges are:
- Handling large parts:
At Asimer Group, we have cranes, lathes, and other specialized equipment to handle valves weighing up to 10 tons. Proper maneuverability of these components is key to avoiding deformation or damage during the machining process.
- Tight tolerances:
Although the valves are large, they require very narrow tolerances to ensure a perfect fit in their connection points and internal seals. Even a minor error can lead to leaks or functional failures.
- Difficult-to-machine materials:
Valves are often made from materials such as stainless steel, nickel alloys, or titanium, which are highly resistant to corrosion and wear but difficult to machine due to their hardness. Our team is experienced in handling these materials using advanced cutting tools and precise techniques.
Equipment and advanced technology at Asimer Group
At Asimer Group, we have state-of-the-art machinery to face the challenges of machining large valves. Our facilities are equipped with CNC lathes, CNC milling machines, Trevisan machining centers, vertical lathes, and boring machines, allowing us to work with large pieces while maintaining strict quality control at every stage.
CNC technology allows us to not only automate processes but also achieve millimeter precision in every component, which is essential to ensuring the performance and durability of valves in critical industrial applications.
One of the key processes we employ is chip removal machining, a technique that allows us to shape valves by controlled material removal, ensuring precise finishes and minimal tolerances in highly complex components.
Success in large-dimension machining depends not only on the machinery but also on the CNC machining tools we use, which are specifically designed to work with high-resistance materials and achieve precision finishes in complex components.
Turning of valves
Turning is a key technique in valve machining, allowing us to shape the outer and inner surfaces of valves, especially those of the spherical or gate type. With our CNC vertical lathes, we achieve the precision needed to create sealing surfaces that ensure airtight closure.
CNC milling
Milling allows us to make precise cuts on the flanges of valves and other critical areas where they connect to piping systems. Thanks to our CNC milling machines, we can machine components with complex geometries and achieve the finishes that meet the technical specifications of each client.
Boring and drilling
Boring is essential for machining the internal surfaces of large-dimension valves. This process ensures that the internal ducts of the valves are perfectly smooth, which is vital for frictionless operation and greater durability.
Quality control: A constant commitment
Asimer Group’s commitment to quality is unwavering. Every project we work on undergoes rigorous quality controls, ensuring they meet the highest standards. In our metrology and quality room, we use advanced technology to ensure that each component meets the exact technical specifications. Tools such as the measuring arm allow us to perform precise dimensional inspections on large parts, while other measuring instruments ensure the accuracy of every process, from machining to final assembly.
In addition to dimensional inspection, we also perform non-destructive testing to ensure the structural integrity of the valves without compromising their functionality, which ensures their strength and durability in extreme conditions.
To reinforce this control, we conduct additional tests using liquid penetrants, allowing us to detect possible cracks or imperfections on the surface of the valves, ensuring they meet the highest standards of safety and reliability.
Additional services: Specialized welding
In addition to machining, at Asimer Group we offer specialized welding, such as automatic MIG welding, TIG welding, plasma transferred arc welding, among others for large valve projects.
The applications of TIG welding are essential in industrial environments where precision and resistance are required, especially in components exposed to extreme conditions, such as high pressures or corrosive environments.
We employ advanced welding and overlay techniques to strengthen the surfaces of valves exposed to corrosive or abrasive fluids. This extends the service life of the valves and ensures their performance in extreme conditions. These same techniques are also applied to other key components, such as industrial pumps, ensuring that both valves and pumps operate safely and efficiently in demanding environments.
If you’re interested in learning more about the differences between TIG and MIG welding, we explore both techniques and their applications in critical industrial processes.
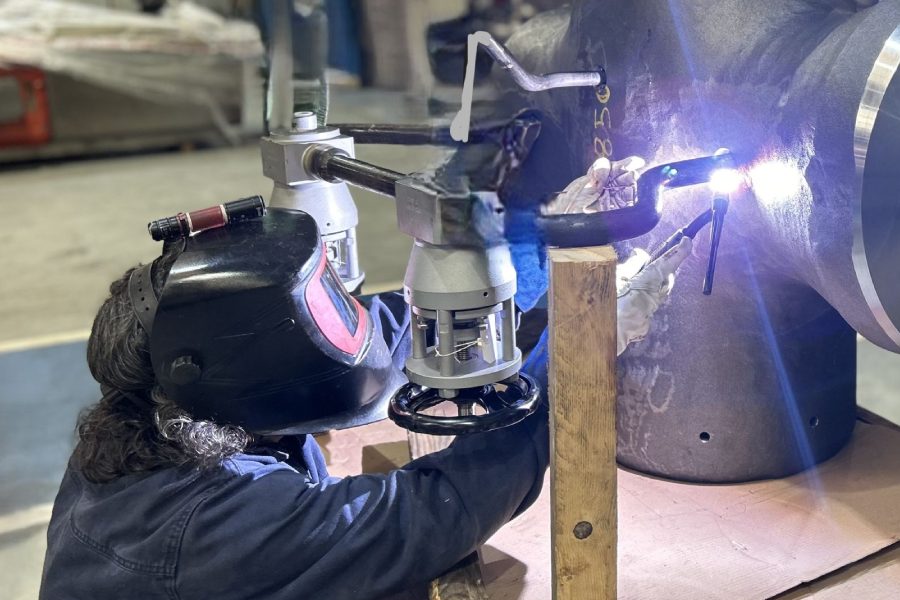
Technological innovation in machining large-dimension valves
Innovation is one of the pillars of Asimer Group, and to stay at the forefront of the industry, we use enterprise resource planning (ERP) systems that allow us to ensure the traceability and efficient management of each project.
Additionally, the use of technologies such as automated machining reflects how we integrate into Industry 4.0 and the CNC machining revolution, optimizing our processes to offer more precise and efficient solutions to our clients.
These technological advancements allow us to be flexible and adapt to the changing demands of our clients, always ensuring the delivery of the highest-quality products. Moreover, we are committed to the continuous improvement of our processes, which has allowed us to increase energy efficiency in industrial valves and reduce environmental impact.
Conclusion
The machining of large-dimension valves is a complex task that requires advanced technology, technical expertise, and an unwavering commitment to quality. At Asimer Group, we are prepared to face the challenges of this industry, providing customized solutions and comprehensive services.
Our ability to work with resistant materials and under strict tolerances positions us as a reliable partner for demanding industries such as petrochemical, marine, energy, and water treatment. If you are looking for a supplier that combines experience, innovation, and cutting-edge technology, Asimer Group is your best choice.
FAQs
What industrial sectors use large-dimension valves machined by Asimer Group? Sectors such as petrochemical, marine, water treatment, energy, and other industries where large volumes of fluids are handled.
What machining capabilities does Asimer Group offer? We can machine valves weighing up to 10 tons, using CNC lathes, milling machines, and advanced machining centers.
How do you ensure the quality of machined valves? Every valve undergoes rigorous quality controls, with full traceability through ERP systems.
What materials are most common in large-dimension valves? Stainless steel, nickel alloys, and other corrosion and wear-resistant materials.
What technologies does Asimer Group use for machining? We use CNC lathes, milling machines, and advanced machining centers.