Needle control valves are critical components in a wide range of industrial applications, from the naval industry to paper pulp production. Their ability to precisely regulate fluid flow makes them an essential choice in industries ranging from chemical and pharmaceutical to power generation and the nuclear industry.
In the naval industry, precision and reliability are of paramount importance in every aspect of vessel design and operation.
Flow control valves play a critical role in managing fluids on board, ensuring precise control in various maritime applications. These valves, known for their exceptional features, are essential in the naval sector. However, to better understand their importance in this field and how they contribute to efficiency and safety at sea, we invite you to read our article Flow Control Valves: Features and Applications in the Naval Industry.
The accuracy of machining is crucial in the industry, especially when it comes to critical components like needle control valves. These valves require high-quality manufacturing to ensure their precise operation. This precision is reflected in their conical design and needle-shaped stem, allowing exceptionally fine control of flow, which is crucial in processes that require precise regulation. Additionally, in industrial environments where resistance to high pressures and temperatures is essential, these valves stand out for their ability to minimize leaks. This has led to their logical choice in many applications, including the petrochemical industry, where precision is essential.
In addition to their use in conventional applications, needle control valves have also found a prominent place in the nuclear industry, where precision and safety are of utmost importance. These valves are used in cooling systems and coolant flow control in nuclear power plants, contributing to the stability and reliable performance of these critical facilities. Furthermore, continuous innovation in the needle valve industry has led to advances such as automation, integration with process control systems, and research on advanced materials that increase their resistance to corrosion and their ability to operate in challenging environments, including cryogenic and desalination applications.
It is also worth mentioning that, for example, in the oil industry, efficiency and safety are of utmost importance, and in the oil industry, axial flow check valves are critical components for maintaining the continuous and controlled flow of oil products along oil pipelines and gas pipelines.
These valves play an essential role in directing fluid flow in a specific direction while effectively preventing unwanted backflow, which is crucial for maintaining the integrity of oil transportation systems.
What Are Needle Control Valves?
Advantages of Needle Control Valves
1. Precise Flow Control
The most outstanding feature of needle valves is their ability to provide exceptionally precise flow control. This is essential in applications that require fine flow regulation, such as in the chemical, pharmaceutical, and food processing industries.
2. High Pressure Resistance
Needle valves are known for their ability to withstand high pressures. Their robust design makes them ideal for applications where fluid pressure is a critical factor.
3. Minimal Leakage
Due to their tight and conical design, needle valves tend to minimize leaks, which is especially important in applications where system integrity is paramount.
4. Wide Temperature Range
These valves are suitable for a wide temperature range, making them versatile and suitable for applications that require operation in extreme conditions.
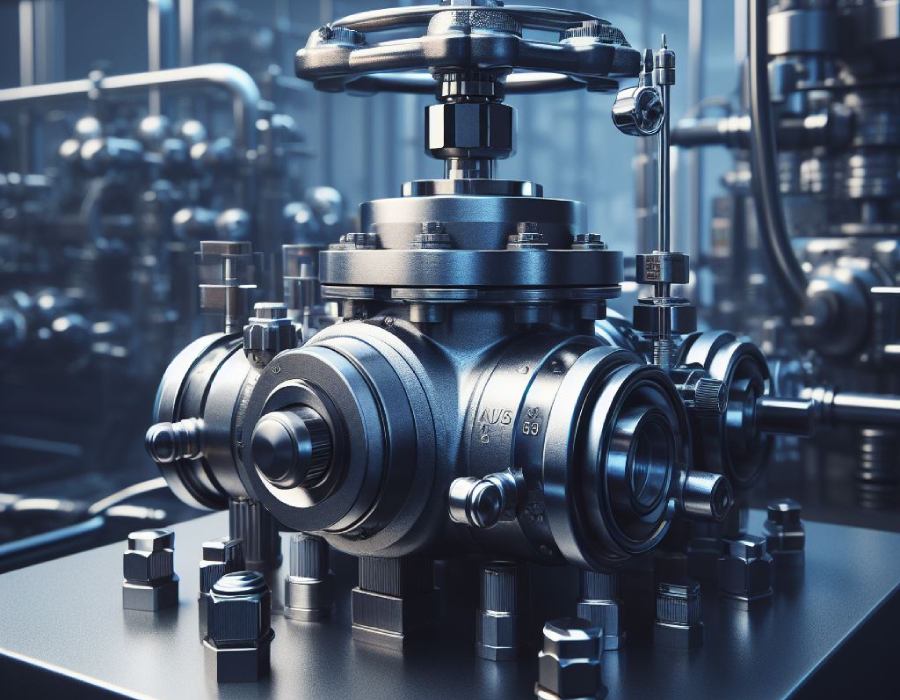
Applications of Needle Control Valves
1. Chemical Industry
In the chemical industry, needle control valves are essential for precise control of reagents and chemicals in manufacturing processes.
2. Pharmaceutical
In pharmaceutical product manufacturing, precision is critical. Needle valves ensure precise control of the flow of active pharmaceutical ingredients.
3. Food Processing
The food processing industry uses needle valves to control the flow of ingredients in the production of food and beverages.
4. Oil & Gas
In oil & gas applications, needle valves are crucial for controlling the flow of fuels, lubricants, and other industry-related products.
5. Energy
In power plants and energy plants, these valves are vital for regulating the flow of water and steam in power generation systems.
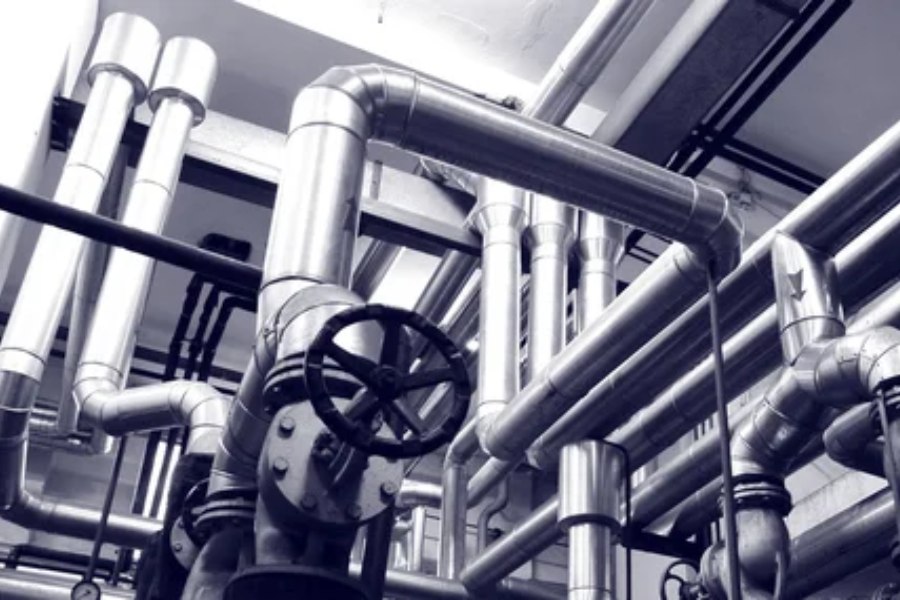
Energy Efficiency in Needle Control Valves
In a world where sustainability and efficiency are key priorities, needle control valves play a fundamental role in improving energy efficiency in a wide range of industrial applications. These precise and advanced valves not only ensure precise control of fluid flow but also contribute to the reduction of energy consumption and operating costs in various industries.
The Importance of Material Selection
A crucial aspect in the manufacture of needle control valves is the selection of materials. Because these valves are used in a variety of environments and conditions, material selection is critical to ensure long-term durability and performance. At Asimer Group we understand the importance of this selection and work closely with our customers to identify the most suitable materials for their specific applications.The materials used in the manufacture of needle control valves may vary depending on the intended use. Common materials include stainless steel, nickel alloys, titanium and corrosion-resistant materials.The choice of material can influence, among other things, corrosion resistance, operating temperature and chemical compatibility. Our engineering experts are trained to advise our customers on the most suitable material selection for their specific needs.
Needle valves are essential components in systems requiring precise flow regulation, such as the chemical and petrochemical industries. Their unique design allows for fine control of flow, making them ideal for applications demanding extreme precision. By ensuring the precise manufacturing of these valves, we can guarantee reliable and safe performance across a variety of industrial applications. By linking this article with “Chip Removal Machining in the CNC Era,” we can explore how high-precision machining contributes to the manufacture of these valves, ensuring accuracy and reliability in their operation.
Application in the Nuclear Industry
Another sector in which needle control valves play a crucial role is the nuclear industry. In nuclear environments, precision and safety are essential. These valves are used in cooling systems, coolant flow control, and other processes related to nuclear energy. The ability of needle valves to precisely and safely control flow makes them a logical choice to ensure the reliable operation of these critical facilities.
Innovations in Needle Control Valves
The needle control valve industry continues to evolve with technological advancements that further improve their performance and versatility. Some recent innovations include:
1. Automated Needle Control Valves
Automation is a key trend in the industry. Automated needle control valves can be remotely controlled and programmed to adjust flow as needed in real-time. This is particularly useful in applications where a rapid response to changes in process conditions is required.
2. Advanced Materials
Research and development of new materials continue, leading to needle valves that are even more resistant to corrosion, extreme temperatures, and aggressive chemical environments. This further expands the applications of these valves.
3. Integration with Control Technology
Needle control valves can be integrated into larger process control systems, allowing for greater automation and monitoring. This is especially beneficial in process optimization and production efficiency.
In an increasingly innovation-oriented industrial world, “Technological Innovations in Industrial Valve Manufacturing” are setting the pace of progress. Discover how these new technologies are transforming precision and efficiency in the production of needle control valves, driving excellence in the industry.
Axial Flow Check Valve: An Essential Complement
In the fluid flow regulation landscape, axial flow check valves emerge as an essential complement that works in harmony with needle control valves. These check valves play a fundamental role in allowing fluid flow to move in a predetermined direction and effectively blocking any attempt at backflow. This is especially critical in applications where system integrity is paramount, and backflows must be avoided, such as in piping systems in chemical plants, water treatment facilities, and power systems.
The strategic combination of needle control valves and axial flow check valves can be crucial for maintaining control, safety, and efficiency in complex piping systems and industrial processes. This results in more reliable operation and a reduction in the risks associated with flow back.
The Integration of Needle Control Valves at Asimer Group
At Asimer Group, leaders in engineering, machining, and welding of industrial valves and pumps, we recognize the significance of needle control valves in various sectors. Our expertise and commitment to quality and precision position us as the ideal partner for companies in various industrial fields.
At the core of our approach is an understanding that needle control valves are essential elements for the efficient and safe operation of multiple processes. Our commitment to excellence is reflected in the quality of the projects we undertake.
In close collaboration with our customers, we offer customized solutions tailored to their specific needs, ensuring that needle control valves integrate seamlessly into their operations and processes.
We hope this article has shed light on the importance of needle control valves in the industry and how they contribute to process efficiency.
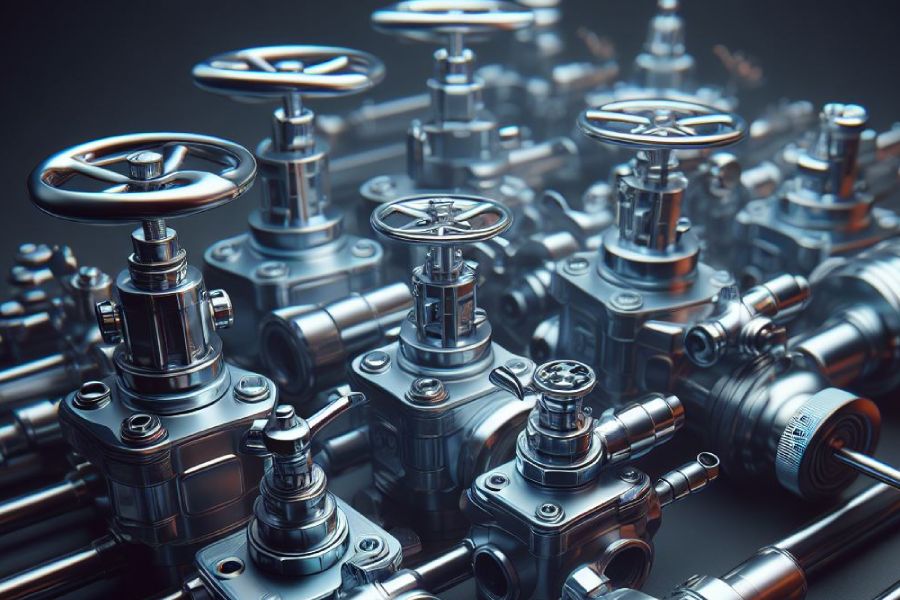