Industrial pumps and butterfly valves are two vital components within the fascinating world of industrial engineering that work together to ensure efficient operation in numerous industrial processes.
In the vast and dynamic world of industrial pumps, it is crucial to understand how Industry 4.0 and the CNC Machining Revolution are radically transforming the design, manufacturing, and operation of these essential devices. The integration of advanced manufacturing technologies, such as CNC machining, is redefining standards of quality, precision, and efficiency in industrial pump production. In this context of innovation and technological progress, Asimer Group is at the forefront, leveraging the advantages of Industry 4.0 and positioning itself as a reference in the application of the latest innovations in the field of CNC machining, thus driving the advancement and evolution of industrial pumps towards a more efficient and sustainable future.
Industrial pumps are mechanical devices designed to transfer liquid or gas fluids from one location to another within an industrial process. Their main function is to generate flow and pressure to move the fluid from a low-pressure location to a high-pressure one, enabling the transportation, supply, or recirculation of various substances.
Industrial pumps find applications in a wide variety of industries, including chemical, petrochemical, food, pharmaceutical, water treatment, pulp and paper, naval, cryogenics, desalination, and oil & gas, among others. They are used for pumping liquids as well as handling viscous and corrosive fluids.
These devices play a fundamental role in the machining and welding of industrial pumps, providing engineering solutions for various applications. In this article, we will explore the types, operation, and key applications of industrial pumps.
The Importance of Industrial Pumps in the Machining and Welding of Industrial Pumps
What Are Industrial Pumps, and Why Are They Essential in the Machining and Welding of Industrial Pumps?
Industrial pumps are mechanical devices designed to transfer fluids from one place to another, generating a constant and controlled flow. In the context of machining and welding of industrial pumps, these machines play a crucial role by supplying the required fluid for cutting, cooling, and lubrication processes. Additionally, in engineering solutions, industrial pumps are used to manage and control the flow of liquids in different applications.
Key Benefits of Industrial Pumps in the Machining and Welding of Industrial Pumps
The use of industrial pumps in the machining and welding of industrial pumps offers several significant benefits. Firstly, these pumps provide a constant and precise flow, ensuring uniform distribution of the fluid and higher quality in the final products. If you are looking to improve the efficiency of your processes, industrial pumps are your solution Additionally, industrial pumps allow for optimal flow and pressure control, contributing to reduced production times and improved overall efficiency. Lastly, industrial pumps also offer greater reliability and durability, reducing maintenance and replacement costs.
The Importance of Oil Refining and Its Relationship with the Welding and Machining of Industrial Pumps and Valves
Oil refining is a critical process in the oil industry that directly impacts the production and performance of industrial pumps and valves used in this sector. Through refining, crude oil undergoes various physical and chemical processes to separate and transform its components into useful products such as gasoline, diesel, aviation fuel, lubricants, and other derivatives.
The need to withstand and handle a wide range of petroleum-derived products, from the lightest to the heaviest and most viscous, poses significant challenges for industrial pumps and valves, exposing them to considerable wear on their components.
In this context, TIG welding emerges as a cutting-edge technique for the manufacturing of industrial pumps and valves, offering exceptional precision and control in joining materials resistant to corrosion and high temperatures. This technique ensures the structural integrity and durability of these essential equipment, thereby contributing to their optimal performance under demanding conditions.
The relationship between oil refining and the machining of industrial valves and pumps is essential because the refined products are used to lubricate and operate these essential equipment. Industrial pumps and valves must withstand and handle a wide range of petroleum derivatives, from lighter to heavier and more viscous ones, resulting in considerable wear on their components.
In this regard, the welding and machining of industrial pumps and valves become crucial to ensuring their optimal operation under rigorous conditions. The welding techniques used must be capable of joining materials resistant to high temperatures and corrosion, while machining must enable precision and durability of these machines’ components.
Oil refining also influences the selection of materials used in the manufacturing of industrial pumps and valves. Due to the presence of chemical substances and corrosive compounds in refined oil, it is essential to use materials resistant to corrosion and abrasion to ensure the equipment’s lifespan and integrity.
Main Types of Industrial Pumps and Their Characteristics for Specific Applications
Centrifugal Pumps: Operation and Applications in the Machining and Welding of Industrial Pumps
Centrifugal pumps are widely used in the machining and welding of industrial pumps due to their ability to handle large volumes of liquid. These pumps use centrifugal force to generate pressure and move the fluid through a rotating impeller. They are ideal for applications that require high flow capacity, such as tool cooling and fluid transfer in piping systems.
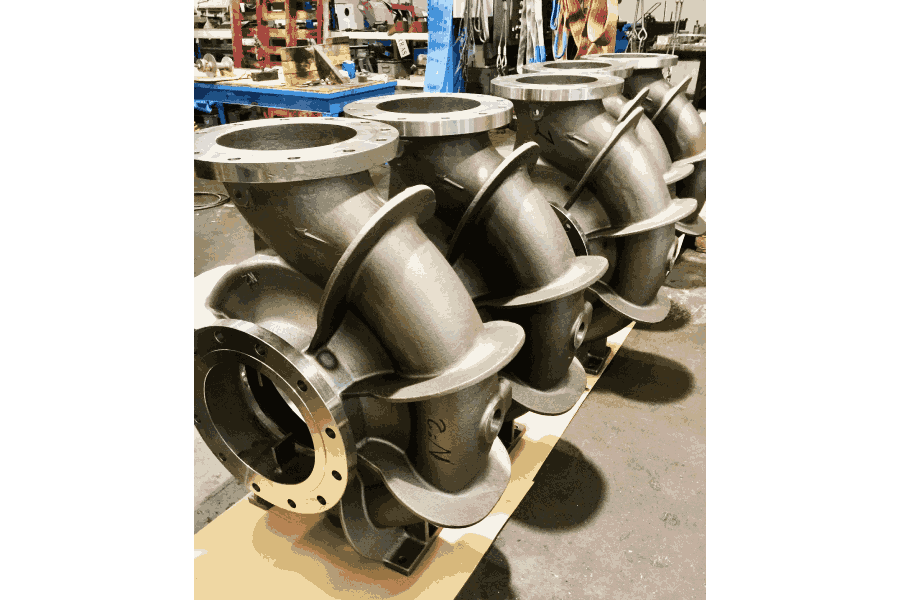
Gear Pumps: Features and Uses in the Industrial Pump Industry
Gear pumps are known for their compact design and efficiency in transferring viscous liquids. These pumps use a pair of gears to displace the fluid and generate pressure. They are ideal for applications involving high-viscosity fluids, such as lubricating oils and sticky materials. In the machining and welding of industrial pumps, gear pumps are used to ensure proper lubrication of tools and transport of specialized liquids.
Piston Pumps: Applications and Advantages in the Machining and Welding of Industrial Pumps
Piston pumps are recognized for their ability to generate high pressures and a constant flow. These pumps use a piston to displace the fluid and generate pressure through alternating movements. They are ideal for applications that require precise pressure and rigorous flow control, such as injecting liquids in high-precision machining processes and welding industrial pumps. Additionally, piston pumps offer long service life and increased resistance to corrosive liquids.
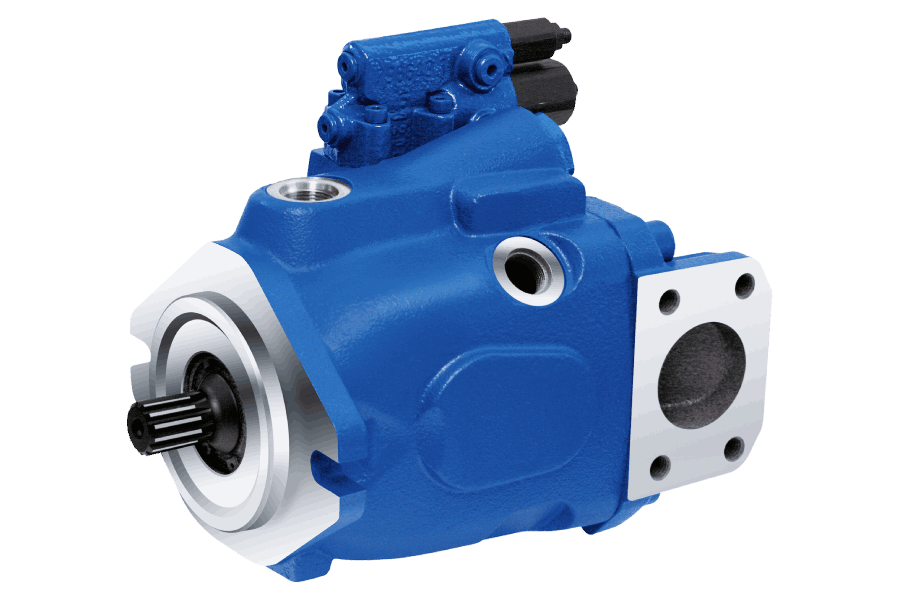
Cryogenic Pumps: Advances in Industrial Applications
Cryogenic pumps have experienced notable advances in industrial applications, especially in sectors that require handling fluids at extremely low temperatures. These pumps are used in aerospace and medical industries, as well as scientific research and cryogenic storage and transportation applications. Their ability to handle fluids at temperatures close to absolute zero makes them crucial tools in the industrial field. These advances have allowed for greater efficiency and reliability in the transportation and handling of cryogenic gases and liquids, significantly contributing to the development of the industry and research in this field.
Operation and Main Components of Industrial Pumps
Operating Principle of Industrial Pumps: How They Transform Energy to Drive Flow
The operation of industrial pumps is based on the transfer of energy to drive the flow of the liquid. In general, these pumps use a motor or a power source to drive a rotating component, such as an impeller or a piston. As the component moves, the fluid is drawn in and then propelled through the piping system. This continuous process of suction and discharge ensures a constant and controlled flow of the liquid.
Essential Components of Industrial Pumps and Their Role in the Machining and Welding of Industrial Pumps
Industrial pumps are composed of several essential components that work together to ensure efficient operation. Some of the most common components include:
- Impeller or Piston: These are the components that generate the necessary motion to transfer the fluid from the inlet to the outlet of the pump. Impellers are typical in centrifugal pumps, while pistons are found in positive displacement pumps.
- Mechanical Seal: This is a critical component that prevents fluid leaks around the pump’s shaft. It ensures proper sealing between rotating and stationary parts, helping to prevent leaks and ensure safe operation.
- Inlet and Outlet Valves: These valves regulate the flow of fluid into and out of the pump. The inlet valve controls the amount of fluid entering the pump, while the outlet valve regulates the flow to the system or process the pump is connected to.
- Motor or Power Source: The motor is responsible for providing the power necessary for the impeller or piston to perform their function and move the fluid through the system.
These components play a crucial role in the machining and welding of industrial pumps, ensuring stable flow, adequate pressure, and smooth operation.
Common Applications of Industrial Pumps in Different Sectors
Use of Industrial Pumps in the Chemical and Petrochemical Sector: Cases and Considerations
In the chemical and petrochemical sector, industrial pumps are used for the safe and efficient handling of chemical and petrochemical products. These pumps ensure controlled flow of corrosive, viscous, and hazardous liquids used in chemical production, oil processing, and other related operations. Proper selection of industrial pumps is crucial to ensure safety, efficiency, and compliance with environmental standards.
Applications of Industrial Pumps in the Food and Beverage Sector: Safety and Hygiene
In the food and beverage sector, industrial pumps play a fundamental role in the safe and efficient handling of liquids and food products. These pumps are used in applications such as ingredient transportation, food packaging, liquid transfer during processing, and equipment cleaning. Industrial pumps guarantee food safety by complying with hygiene and quality standards, preventing cross-contamination, and ensuring controlled product flow.
Industrial Pumps in the Energy and Oil Sector: Challenges and Solutions
In the energy and oil sector, industrial pumps play a vital role in the transportation and extraction of crude oil and other related fluids. These pumps are used in applications such as well drilling, oil pumping, and long-distance fluid transportation. Industrial pumps must withstand extreme conditions, such as high temperatures and pressures, and must comply with safety regulations and standards in the industry.
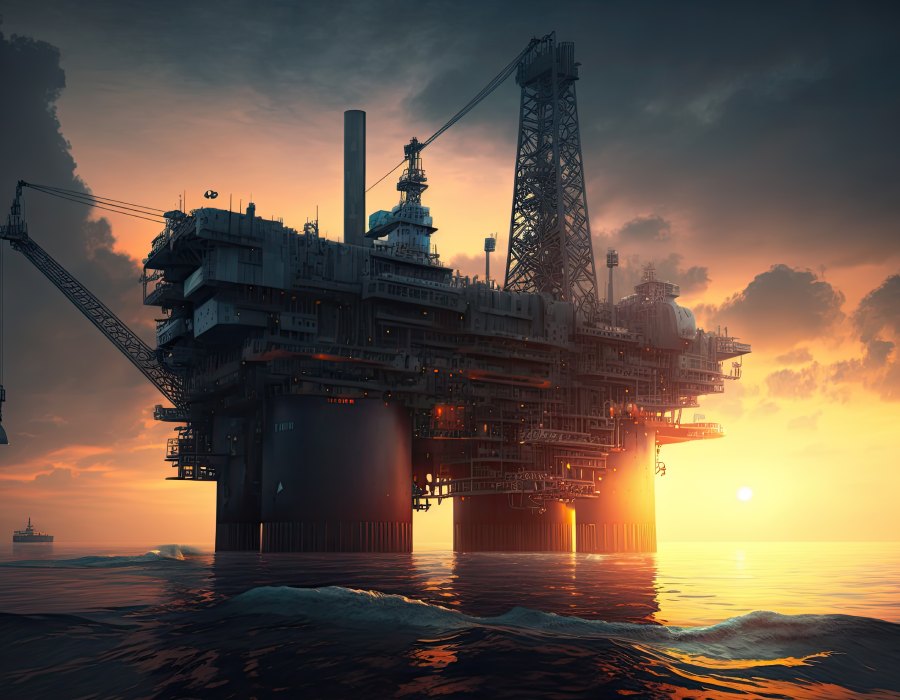
Considerations for Selecting and Maintaining the Right Industrial Pumps
Key Factors to Consider When Choosing Industrial Pumps for the Machining and Welding of Industrial Pumps
When selecting the right industrial pumps for machining and welding of industrial pumps, several factors must be considered. These include the type of fluid to be pumped, viscosity, required pressure, flow rate, temperature, and chemical compatibility. Additionally, it is essential to evaluate the working environment, safety requirements, pump size, and capacity. Considering these factors allows for the choice of the most suitable industrial pump to optimize performance and efficiency.
Preventive and Corrective Maintenance of Industrial Pumps: Ensuring Optimal Performance
Proper maintenance of industrial pumps is essential to ensure optimal performance and extend their lifespan. Preventive maintenance includes regular cleaning, filter replacement, lubrication of moving components, and inspection for potential leaks. Additionally, it is important to conduct periodic checks of mechanical seals and bearings and monitor pressure and flow rates. In case of failures or breakdowns, corrective maintenance should be carried out immediately to minimize downtime and repair costs.
Future of Industrial Pumps: Trends and Technological Advances
Innovations and Recent Developments in the Field of Industrial Pumps
The field of industrial pumps is constantly witnessing innovations and technological advances. One emerging trend is the use of more durable and robust materials such as ceramics and high-performance polymers. Additionally, smart technologies, such as sensors and real-time monitoring systems, are being implemented to optimize performance and predict potential failures. Furthermore, more energy-efficient and environmentally-friendly pumps, such as variable speed pumps and high-efficiency pumps, are being developed.
Impact of Digitalization and Industry 4.0 on Industrial Pumps
Digitalization and Industry 4.0 are transforming the industrial pump industry. Integration of automated control systems and data analytics allows for more precise monitoring and control of industrial pumps. Additionally, network connectivity facilitates communication between different equipment and systems, improving efficiency and responsiveness. Digitalization also drives the implementation of predictive maintenance, enabling early detection of potential issues and avoiding costly downtime.
Industrial pumps at Asimer Group
Industrial pumps are fundamental elements in the machining, welding, and engineering solutions of industrial pumps. With their ability to generate constant and controlled flow, these machines drive productivity and turn flow into gains. Understanding the different types of industrial pumps, their operation, and their applications in various sectors, as well as considering selection and maintenance considerations, allows for harnessing their full potential.
By linking this article with “Chip Removal Machining in the CNC Era,” we can examine how the precise manufacturing of the internal parts of these pumps through CNC machining contributes to their optimal performance and extended lifespan.
Moreover, trends and technological advances in the field of industrial pumps present new opportunities to enhance efficiency and sustainability. As the industry evolves, industrial pumps will continue to play a crucial role in optimizing machining processes, welding operations, and engineering solutions.
Asimer Group, a company specialized in machining, welding, and engineering solutions of industrial pumps, has addressed the essential fundamentals of these vital equipment in this article. It is crucial to rely on experts in the field, such as Asimer Group, who offer personalized solutions for machining, welding, and engineering services to adapt industrial pumps to the specific needs of each industry.
At Asimer Group, we are committed to excellence and quality in every project, ensuring optimal operation of industrial pumps, and backed by a highly trained team to provide comprehensive solutions.
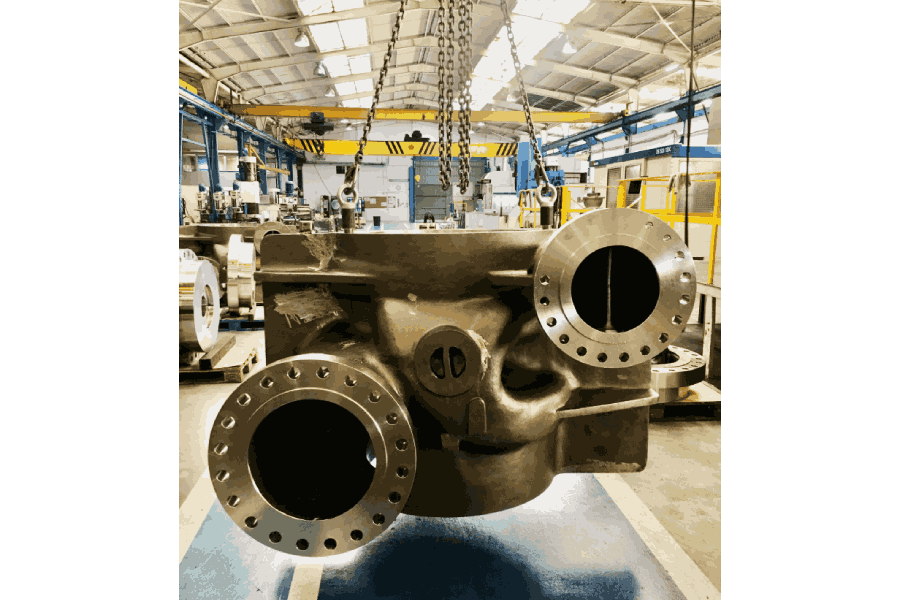