In the aerospace industry, cryogenics is a branch of engineering that focuses on the study of low temperatures and their applications in various fields, from medicine to welding and machining of industrial valves and pumps. This article will focus specifically on cryogenic applications in the aerospace industry.
Cryogenic pumps in the Aerospace industry – Advantages and challenges.
The aerospace industry is one of the most stringent industries in terms of precision and safety. Cryogenic pumps are an important tool in aerospace engineering because of their ability to process gases at very low temperatures. In this article, we will look more closely at the benefits and challenges associated with the use of cryogenic pumps in the aerospace industry.
Advantages of using cryogenic pumps in the aerospace industry.
- An important advantage is that cryogenic bombs can manipulate gases at very low temperatures, which is essential for the production of rocket fuel. These fuels require extremely low temperatures to stay in a liquid state, allowing them to be stored and transported safely. Cryogenic bombs can be used to cool the fuel and pump it through rocket propulsion systems.
- Another advantage of cryogenic pumps is their ability to produce extremely high voids. This is essential to maintain the purity of materials and to prevent pollution in the manufacture of aerospace components. In addition, cryogenic pumps can also be used to cool and cool aerospace components, helping to reduce friction and increase part life.
In addition, cryogenic pumps can also be used to cool and cool aerospace components, helping to reduce friction and increase part life.
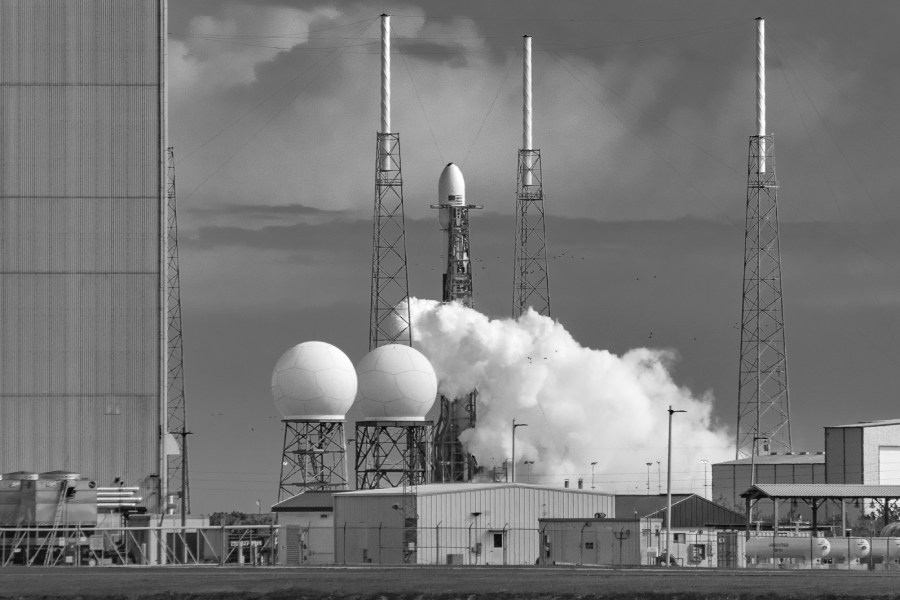
Challenges associated with the use of cryogenic pumps in the aerospace industry.
- Cryogenic pumps can be expensive and require serious maintenance. That is why it is important to choose a reliable industrial supplier and a machining and welding supplier who has experience in handling cryogenic pumps and other high precision equipment. A supplier with experience in the aerospace industry can provide customized solutions tailored to the needs of each customer.
- Treating gases at very low temperatures requires a high degree of precision and care. Lack of attention to detail can lead to machine failure, which can be dangerous and costly.
In the aerospace industry, quality and safety are paramount. That is why it is important to find a machining and welding supplier for industrial valves and pumps that has experience in the aerospace industry as it will be able to provide customized solutions adapted to the needs of each customer.
Cryogenic valves in the aerospace industry: Design and functionality.
In the aerospace industry, cryogenic valves are a fundamental component of rocket and satellite propulsion systems. These valves are used to control the flow of cryogenic fluids, such as liquid hydrogen and liquid oxygen, which are essential for rocket propulsion.
Cryogenic valves must also be designed to operate efficiently and safely. In rockets and satellites, the amount of liquefied gas must be precisely adjusted to ensure the proper functioning of the system. Therefore, the valves must be able to accurately and reliably regulate the flow of cryogenic liquid.
The design of cryogenic valves is essential to ensure their effectiveness in extremely cold environments. The materials used for its construction must be resistant to extremely low temperatures and resistant to thermal contraction. In addition, they must withstand the pressure of the cryogenic liquid without deforming or breaking.
Another crucial factor in the functionality of cryogenic valves is their sealability. Because the cryogenic fluid is extremely cold, valves must be hermetically sealed to prevent leaks. If a leak occurs, the cryogenic liquid can evaporate quickly, which can have serious consequences for the safety of the system and the entire mission.
In addition, engineers are working to develop more accurate and reliable cryogenic valves. Precision is critical in the aerospace industry and cryogenic designs are being enhanced to ensure accurate and reliable flow control of cryogenic fluids.
Technological advances in cryogenic valves are constantly evolving and increasingly advanced solutions are being developed. For example, some cryogenic designs use stronger composite materials that can withstand the extreme temperatures and pressures of cryogenic fluids without cracking or breaking.
How aerospace engineering uses cryogenics in the machining and welding of industrial pumps and valves.
Aerospace engineering is a field that constantly strives to be at the forefront of technology and manufacturing processes. One of the techniques introduced in this field is cryogenics, which is used in the machining and welding of industrial pumps and valves.
Cryogenics is a process that cools materials to extremely low temperatures, improving their strength and durability. In aerospace engineering, cryogenics is used to improve the quality of parts used in the production of pumps and valves, which are key components of any aeronautical system.
Cryogenics is applied in two stages of the manufacturing process: in welding and machining:
- In welding, cryogenics is used to reduce the stress and distortions that are generated during the process, which allows higher quality welds and avoid deformations in the parts.
- In machining, cryogenics are applied to improve the hardness and strength of cutting tools, allowing for more precise cuts and longer tool life.
Aerospace engineering uses cryogenics to improve the quality and durability of parts used in manufacturing industrial pumps and valves. This technique is used in both welding and machining, allowing higher quality components to be obtained and increasing the service life of the cutting tools used in the process.
Cryogenics is an innovative technology that has proven its effectiveness in the aerospace field and will continue to be used in the future to improve manufacturing processes in this industry. Cryogenics is also an environmentally friendly technique, as it reduces the use of lubricants and refrigerants that can be harmful to the environment. In addition, by improving part quality and extending tool life, it reduces the consumption of materials and energy in the manufacturing process.
The use of cryogenics in aerospace engineering requires a breakthrough in the field of parts manufacturing technology for the aerospace industry. This technique allows to improve the quality of the parts and prolong their useful life while reducing costs and minimizing the environmental impact of the manufacturing process. Cryogenics is one of many innovative techniques being developed to improve the efficiency and sustainability of the aerospace industry.
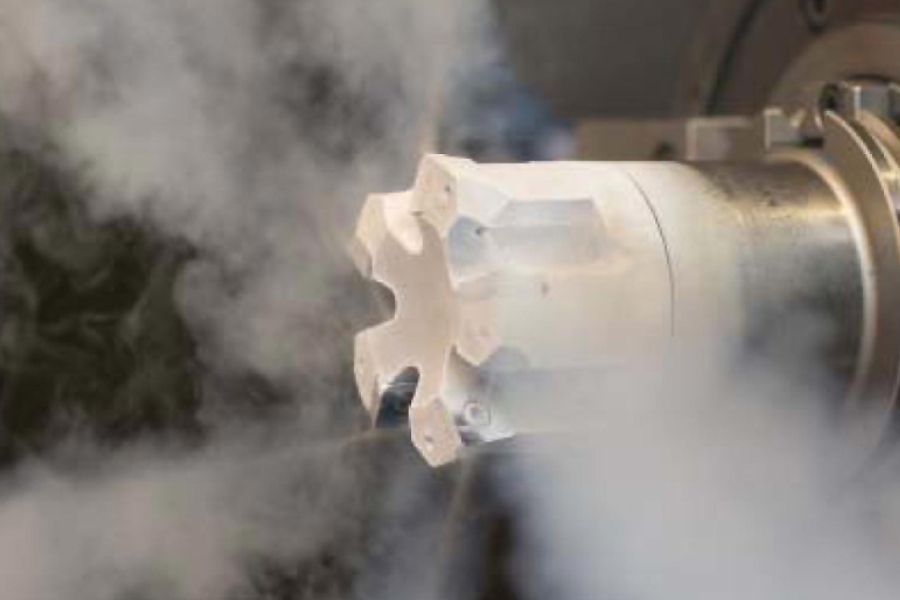
Cryogenics in rocket manufacturing: A key process for success.
Rocket manufacturing is a complex process that requires high precision and reliability. Cryogenic technology has become essential in this field, as it can improve the quality and performance of rocket components. Rocket manufacturing uses cryogenic technology to cryogenically cool critical components such as fuel tanks and pipelines. This makes the fuel cooler and denser, which improves the rocket’s performance and efficiency. Cryogenic technology is also used in the manufacture of rocket engines to improve the quality of parts. Cooling parts to cryogenic temperatures can reduce internal stresses and improve the homogeneity of alloys used to manufacture engines, resulting in more reliable and durable engines.
Another application of cryogenics in rocket construction is pre-launch testing of critical components. By exposing components to cryogenic temperatures, it can simulate extreme conditions in space and ensure component reliability and performance during launch.
In short, cryogenic temperatures are a critical process for successful rocket manufacturing. Improve component quality and performance, ensure engine reliability and durability, and ensure successful launches. Cryogenic technology has become an essential technology for rocket construction and will remain essential for space exploration.
Improving the efficiency of the aerospace industry with cryogenic technology.
Cryogenic technology has become indispensable in the aerospace industry due to its numerous applications that improve the efficiency of parts manufacturing and performance of aeronautical systems.
Cryogenic temperatures are used in the manufacture of aerospace components to improve material quality. Cryogenic cooling can improve the homogeneity of the alloy and reduce the internal stress of the material. This makes the part more durable and durable, helping to reduce wear and improve performance.
Cryogenics is also used to inspect and test components. By cooling components to cryogenic temperatures, manufacturing defects can be detected and corrected, ensuring quality before use in aircraft systems. Cryogenics is used in aerospace systems to improve their performance.
In aircraft propulsion, cooling the air entering the engine increases its density, improving thrust and combustion efficiency. In aircraft cooling systems, cryogenic temperatures can reduce energy consumption and improve system efficiency.
The aerospace industry has significantly benefited from advancements in cryogenics, especially in areas such as rocket propulsion and cooling of electronic systems. Now, with the advent of Industry 4.0 and the CNC Machining Revolution, a new horizon of possibilities opens up in aerospace component manufacturing.
In addition, cryogenic technology is environmentally friendly, as it reduces the consumption of materials and energy in the manufacture of components and aviation system operations. In short, cryogenic technology is critical to improving efficiency in the aerospace industry. Its various applications improve the quality and durability of components and the performance and efficiency of aeronautical systems, increasing the safety and profitability of the industry.
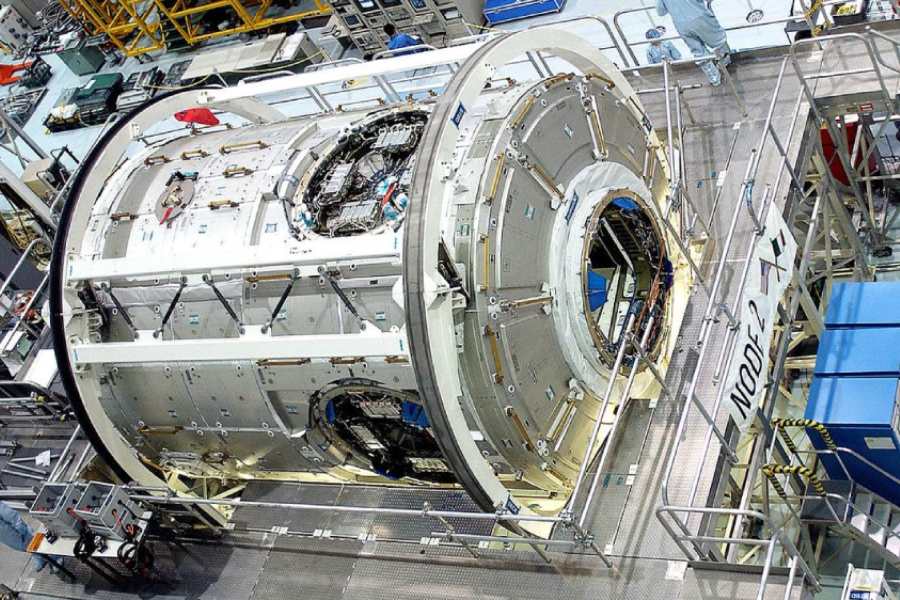