What are cryogenic pumps?
Cryogenic pumps are devices used to pump gases and vapors at low temperatures, usually below -150 °C. Cryogenic pumps are generally used in applications where a high degree of cleanliness and purity is required in the working environment, such as in semiconductor manufacturing and high energy physics studies. These industrial pumps are mainly based on the adsorption and desorption of gases on solid surfaces, which allows them to acquire an extremely high vacuum in closed systems.
How do cryogenic pumps work?
Cryogenic pumps use an adsorbent material, usually activated carbon, which is cooled at low temperatures by a cryogenic refrigerator. When gases and vapors come into contact with the adsorbent material, they adhere to its surface and are removed from the system. To regenerate the adsorbent material and remove the adsorbed gases, the material is heated at high temperature by electrical resistors or by injecting a hot gas. This adsorption and desorption process is continuously repeated to keep the vacuum in the system.
Types of Cryogenic Pumps.
There are different types of cryogenic pumps, each with its own characteristics and applications. The most common cryogenic pumps are centrifugal pumps, screw pumps, gear pumps, vane pumps and vacuum pumps. Each of these pumps offers unique features to meet the needs of a wide range of industries.
Screw pumps.
Screw pumps are equipment used for transferring cryogenic liquids. These pumps are characterized by high performance and low energy consumption. These pumps are mainly used for the transfer of oil and gas and other fluids at low pressures and extremely low temperatures.
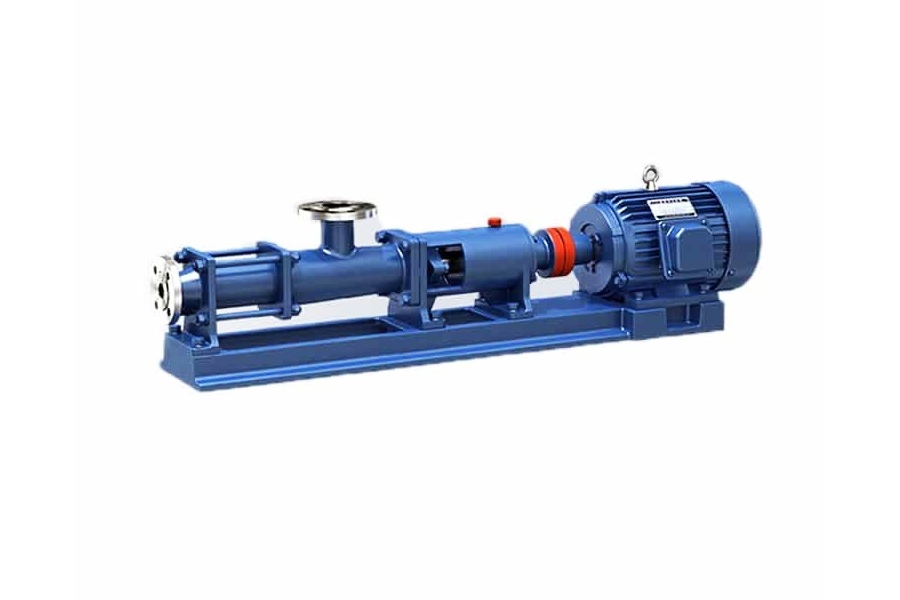
Centrifugal pumps.
Centrifugal pumps are the ideal tool for applications requiring constant flow. These pumps are suitable for transferring liquids at low pressures and high temperatures such as transferring liquefied gases to a variety of industrial applications, as in the process of regasification of natural gas in refueling and supply stations These pumps have a stainless steel housing to resist the aggressive environment of cryogenic liquids.
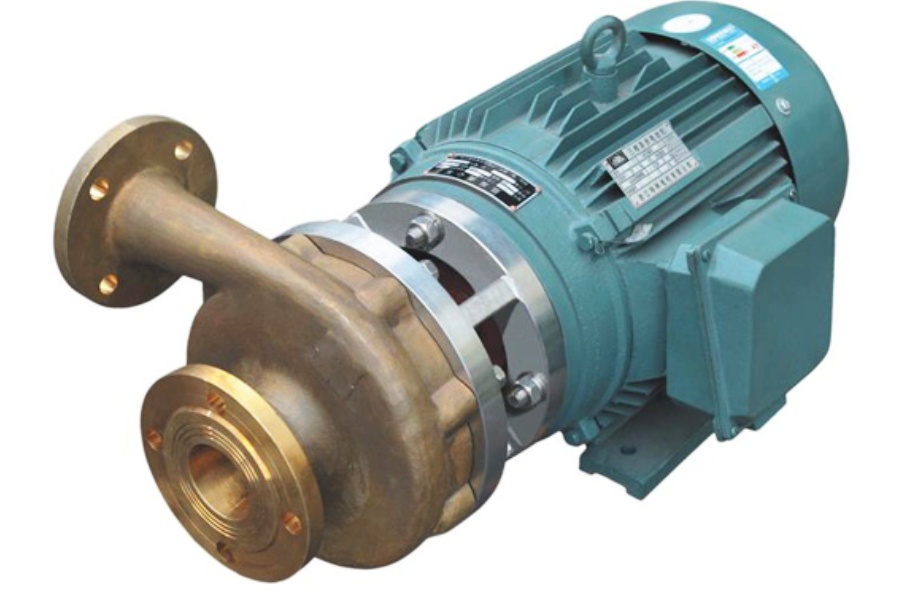
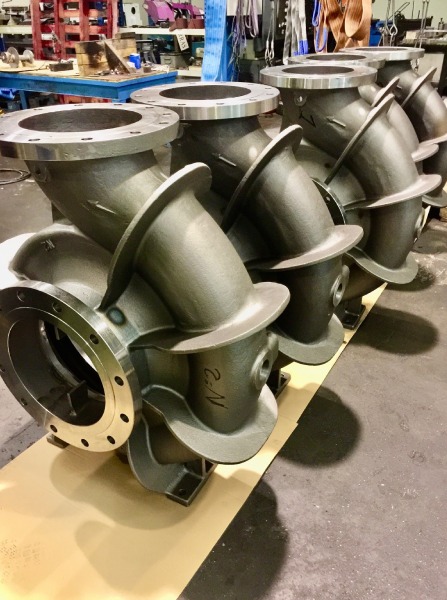
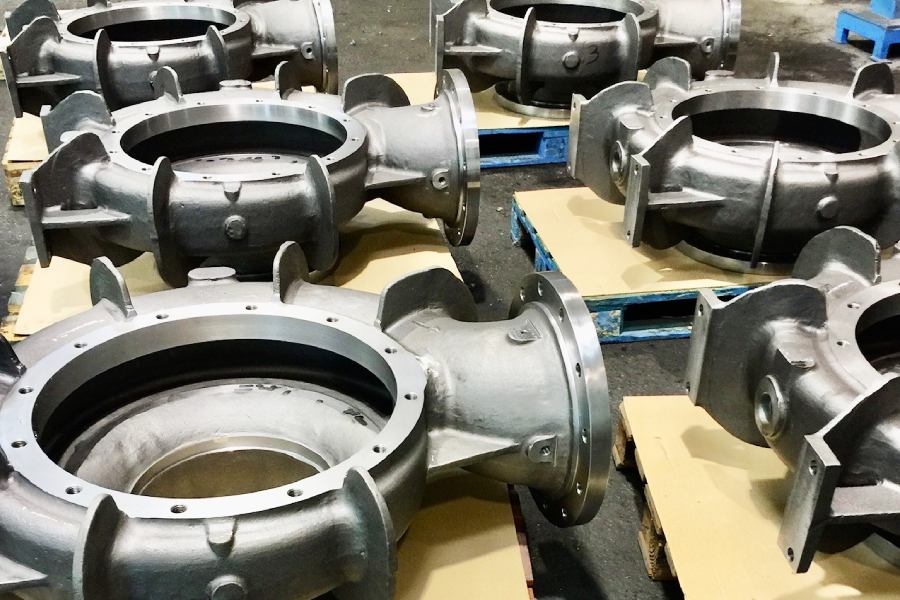
Vane pumps.
Cryogenic vane pumps are also commonly used for the transfer of cryogenic liquids at low pressures and extremely low temperatures. These pumps are a popular choice in the chemical industry for the transfer of chemicals and in the textile industry for the transfer of products. They are also used in oil cleaning in closed circuits and in water transfer in refrigeration facilities.
Cryogenic vane pumps are characterized by low noise and relatively limited maintenance compared to other types of pumps. Its pallet design allows smooth, pulsation-free fluid transfer, making them ideal for applications that require constant flow.
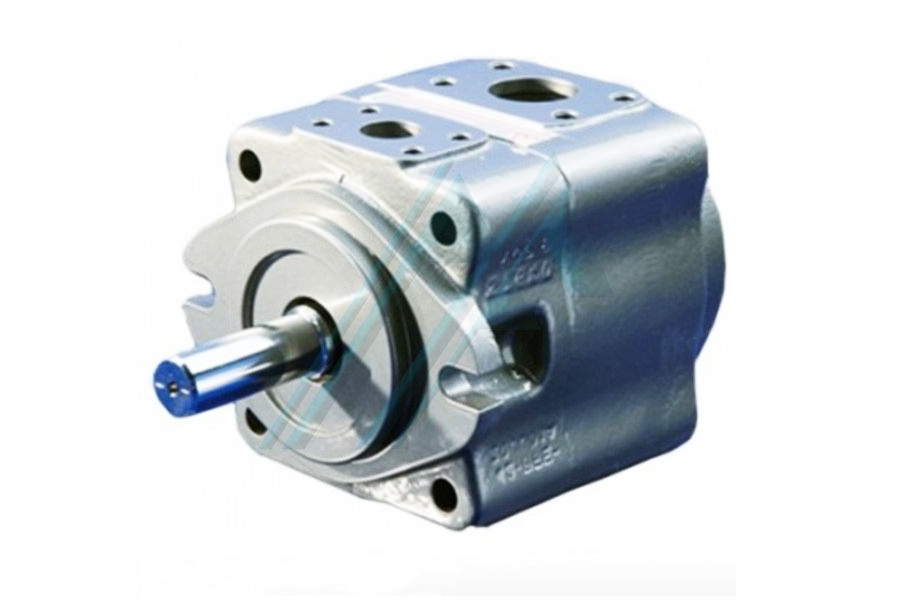
Gear pumps.
Gear pumps are also used for the transfer of cryogenic liquids. These pumps are characterized by high reliability, wear resistance and durability. These pumps are mainly used for the transfer of liquids at low pressures and extremely low temperatures.
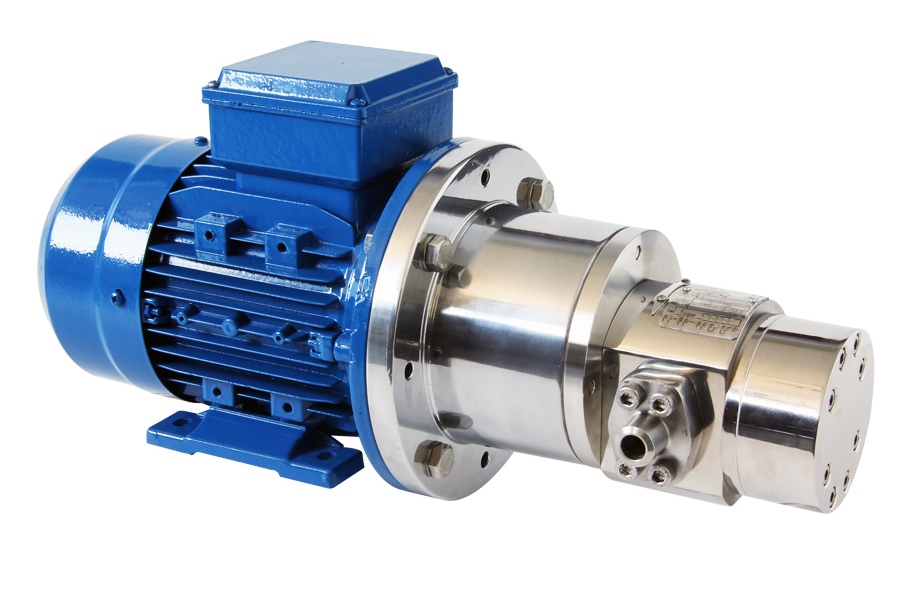
Vacuum pumps.
Vacuum pumps are used to create and maintain a vacuum environment in applications involving gases at extremely low pressures. Although they can be used in cryogenic applications, they are not considered as cryogenic pumps per se. These pumps have a robust and corrosion resistant design, and can operate with relatively high efficiency.
It is important to note that the use of vacuum pumps in cryogenic applications is common due to the need to create and maintain a vacuum environment in cryogenic chambers to minimize heat transfer by conduction and convection. However, its main function is to create and maintain a vacuum environment, and not the handling of cryogenic gases.
In short, we could say that cryogenic pumps, same as cryogenic valves, are a vital tool for the cryogenic liquid processing industry. These pumps offer a unique combination of performance and reliability, and are designed to meet the needs of a wide range of industrial applications. Therefore, it is important to understand the different types of cryogenic pumps available in the market to choose the right cryogenic pump for your needs.
Industrial applications of cryogenic pumps.
Industry 4.0 and the CNC Machining Revolution have brought about a significant change in the design and manufacturing of cryogenic pumps, completely transforming their efficiency and performance. The integration of advanced machining technologies and computer numerical control (CNC), as you can read in our article about our Trevisan machining center, is leading the way towards the production of cryogenic pumps that are more precise, reliable, and adaptable to industry demands. These innovations are shaping the future of cryogenic pump manufacturing, offering a unique combination of performance and reliability to meet the needs of a wide range of industrial applications.
Cryogenic pumps are widely used in the industry for various applications, including:
Semiconductor manufacturing:
In semiconductor production, an extremely clean and impurity-free working environment is required. Cryogenic pumps are used to remove unwanted gases and vapors from the working environment and maintain vacuum in closed systems.
High energy physics research:
In high energy physics research, particle accelerators are used to study the structure of matter. Cryogenic pumps are used to maintain vacuum in particle accelerator tubes and remove gases and vapors that may affect measurement accuracy.
Fabrication of pharmaceutical products:
In the manufacture of pharmaceutical products, a high degree of cleanliness and purity in the working environment is required. Cryogenic pumps are used to remove unwanted gases and vapors from the working environment and maintain vacuum in closed systems.
Aerospace industry:
In the aerospace industry, cryogenic pumps are used to simulate space vacuum in satellite test systems and other space equipment.
Scientific research:
Cryogenic pumps are also used in scientific research to maintain vacuum in closed systems and remove gases and vapors that may interfere with measurements, tests and experiments.
Advantages and disadvantages of cryogenic pumps.
Advantages.
- Ability to achieve an extremely high vacuum.
- High efficiency.
- Low maintenance.
- Clean vacuum without risk of oil contamination.
In addition, these pumps are capable of handling large volumes of gas and steam, making them ideal for use in industrial applications.
Disadvantages.
However, there are also some disadvantages associated with the use of cryogenic pumps:
- They require continuous cooling by a cryogenic cooler, which can result in significant energy consumption. In addition, regeneration of the adsorbent material can take a long time and can result in long system downtime.
- They can be expensive compared to other types of pumps used in vacuum applications.
- They may be sensitive to certain gases and vapors, which may limit their use in some applications.
Despite these disadvantages, cryogenic pumps are still widely used in a variety of industrial applications due to their ability to achieve high vacuum and maintain a clean and impurity-free working environment. In addition, continuous research and development in the field of cryogenic pumps have led to improvements in the efficiency and durability of these pumps, making them even more attractive for use in the industry.
Conclusions.
Cryogenic pumps are key devices in a wide variety of industrial applications where a high degree of cleanliness and purity is required in the working environment. Although they present some disadvantages, their advantages in terms of efficiency, ability to handle large volumes of gas and steam, and ability to achieve a high vacuum make them an attractive option for use in the industry.
The field of cryogenic pumps continues to evolve and improve, leading to the creation of new applications and increased use in the industry. Over time, cryogenic pumps are likely to become an increasingly important part of industrial and research technology, helping to drive development and innovation in a variety of fields.