What is an axial flow check valve?
An axial flow check valve is a kind of silent check valve. The check valve is actuated by the medium itself, automatically opening and closing the valve disc. The axial valve is a flexible device generally designed to prevent the reflux of fluids or gasses such as; gas, air, nitrogen, carbon dioxide, propane vapor, other non-corrosive gasses, or water in a wide range of flow rates.
Axial flow check valves are fundamental in various markets, and their effectiveness is largely due to CNC machining. This method ensures the manufacturing of high-quality industrial valves, enhancing their performance and reliability in a variety of industrial applications, as in the cryogenic or petrochemical industry.
Axial flow valves have been adopted throughout the petrochemical industry in severe-service, high-integrity, and critical applications. They are best suited for applications where minimal downstream turbulence, low fixed pressure drop, fast shut-off, control precision, and reliability are important. It has the advantages of small flow resistance, significant flow coefficient, compact design, etc. It is the best valve for oil collection and transmission piping systems, especially for oil transmission pump outlet.
Thousands of axial flow valves are installed in upstream, midstream and downstream applications, with exceptionally good service records.
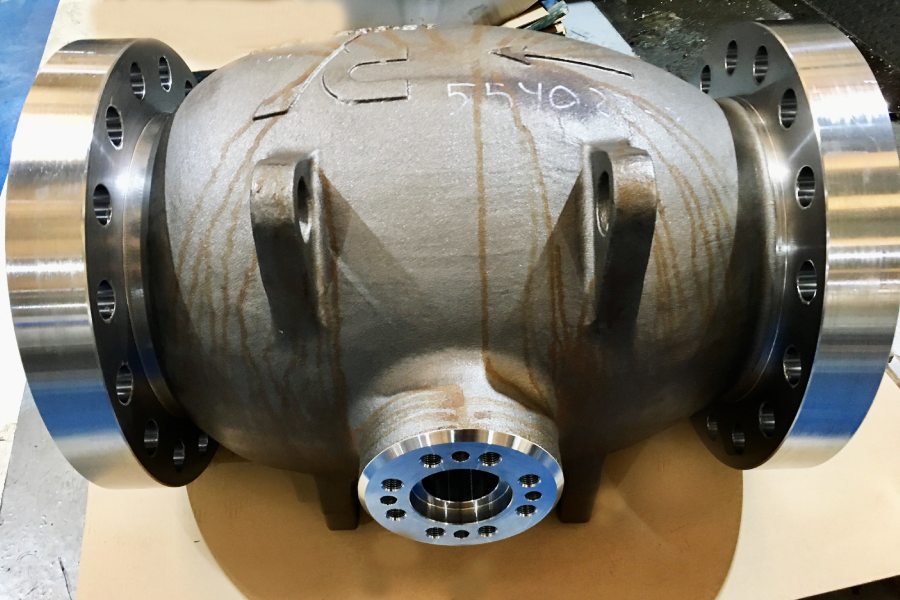
Axial flow check valve types
There are several types of axial flow check valves
- Axial opening and closing valve.
- Axial check valve.
- Axial overpressure relief valve.
- Axial control valve.
- Axial throttle valve
Why is an axial flow check valve used?
As we mentioned earlier, axial flow control valves are a type of control valve designed to prevent rapid flow reversal in a pipeline, known as “water hammer”, which can cause serious damage to various equipment in the pipeline. This type of valve closes quickly enough without causing excessive pressure peaks, avoiding blows.
The axial flow control valve´s streamlined design allows full opening at low flow and fluid velocities, achieving low pressure drop. Its spring-loaded system and sealing properties ensure trouble-free, low-maintenance closure.
Based on the Venturi effect, the reduced flow area allows a fast full opening and the disc remains in position against its stop under normal flow conditions. In a reduced flow situation, the spring reacts quickly, overcoming the force of the fluid and rotating the disc back to a fully closed position with a short stroke. This system greatly reduces reaction time, with a shock-free response that protects critical pipeline elements.
These types of valves are an alternative to quick-closing non-return valves, assisted with an actuator and are used in systems with higher protection requirements.
Innovative technology
Today, with axial flow check valves we achieve:
- Achieve sustainability goals, thereby reducing energy consumption achieving zero fugitive emissions over the entire life of the valve
- Precise control and high regulation range
- Lower operating cost
Main markets for axial check valves
Although axial flow check valves can be used in a multitude of applications, they are used primarily by a growing number of industries for the following:
Oil and gas production, including midstream:
- Regasification
- Liquefaction
- Centrifugal compressor discharge
- Fire water lines
- Oil/steam separation
- Steam and CO₂ injection
- Oil and gas collection systems.
Chemical and pharmaceutical:
- Chlorine
- Phosgene
- Aromatics
- Polymers
- Acids
- Air gap
- Caustics
Petroleum refining and petrochemicals:
- Hydrogen
- Cracking
- Vapor
- Raw oil
- Ethylene
- Propylene
- Vapor
Energy:
- Vapor
- Condense
- Boiler feed pumps
- Cooling towers
- Service water recirculators
- River water intake
- Renewable
Applications
- Water hammer prevention system
- Pump discharge application
- Cooling water systems (ethylene, LNG)
- Water supply and transmission systems
- Drinking and raw water
- Transmission Line Compressor Discharge
- LNG compressor train
- Multiphase pumping
- Subsea Pump and Flowline Application
Asimer Group experience
Throughout the last 14 years, Asimer Group has participated in the development of Axial type valves together with the Technical Department of many of its most important customers, since this type of axial control valves combine an excellent capacity (low loss of pressure) with very high controllability over a full range of valve strokes.
These valves have a very low life cycle cost and still perform well. By selecting axial control valves, the end user will ensure safe and reliable operation of the associated fluid delivery and transportation system.
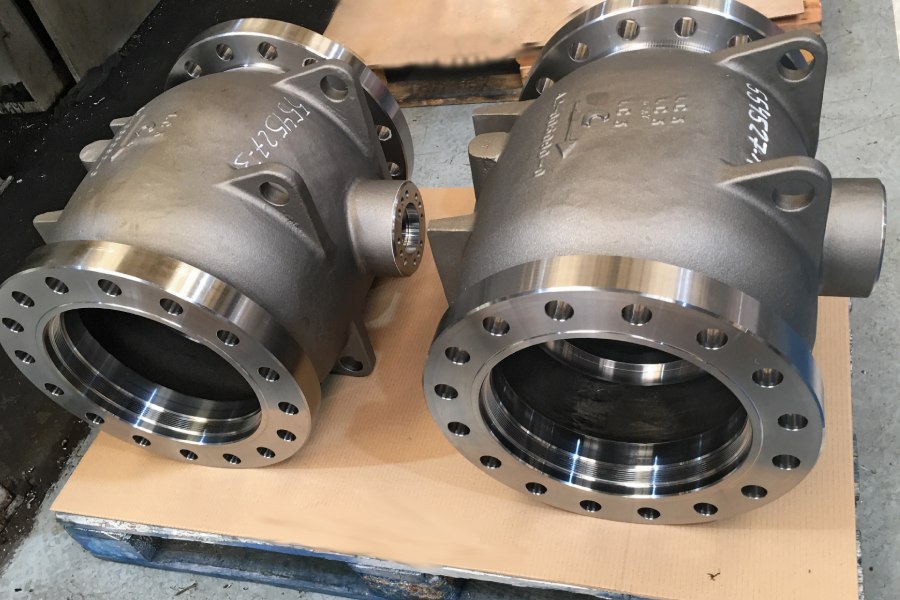
Conclusion
Research and development of innovative and optimized flow control products and services are essential for the growth of the global hydrocarbons industry, for upstream, midstream or downstream applications. Companies that maintain full control over the design, manufacturing and development process have a key advantage, in terms of product quality, and are well-positioned to meet the demand for highly reliable and precise equipment and keep up with the future market growth.
In the dynamic universe of axial flow check valves, where efficiency and precision are crucial, it is essential to understand how technology is shaping every aspect of our industry. The fusion of Industry 4.0 and the CNC Machining Revolution emerges as a guiding beacon, redefining the design and manufacturing standards of these innovative valves.
This technological marriage has not only optimized the effectiveness of check valves but has also revolutionized how they are conceptualized and produced. Industry 4.0 has introduced process interconnectivity and artificial intelligence, establishing a new paradigm in manufacturing. Simultaneously, CNC Machining has elevated precision and consistency to unprecedented levels, enabling the creation of high-quality valves that meet the rigorous standards of various industrial applications.